If you ask people who run quarries what their biggest pain point is, they’re likely to say it’s transporting their product. It’s expensive, and the logistics involved can be challenging.
Because the products excavated from quarries are mostly used as building materials, the goal has traditionally been to locate quarries near roads and other construction jobsites. This is typical in urban areas — and is becoming an increasingly bigger pain for aggregate mining companies because the industry is facing more regulations on drill and blast methods due to environmental concerns. Compounding this is the fact that the world is becoming more urban as cities expand into rural areas. Many quarries are turning to surface miners to produce aggregate. These mobile units use a cutting drum to mechanically excavate materials. This method can be used in conjunction with drill and blast, or replace it.
Surface miners offer many advantages:
- Give access to areas in quarries that have physical or permitting limitations.
- Produce minimal noise, dust and vibration.
- Cut precisely.
- Produce a small, consistent particle size.
- May remove steps from the mining process, such as the use of a primary crusher.
- Can be used for site preparation and haul-road construction and maintenance.
At Vermeer, we’ve seen these benefits in action. We have a customer who chose not to use a primary crusher because the surface miners could consistently produce a 6-in (15.2-cm) minus particle size.
Another customer, a South American company, had a million tons of mineable product they couldn’t drill and blast because of nearby pipelines, powerlines and roads. A surface miner was able to get the last remaining valuable aggregate.
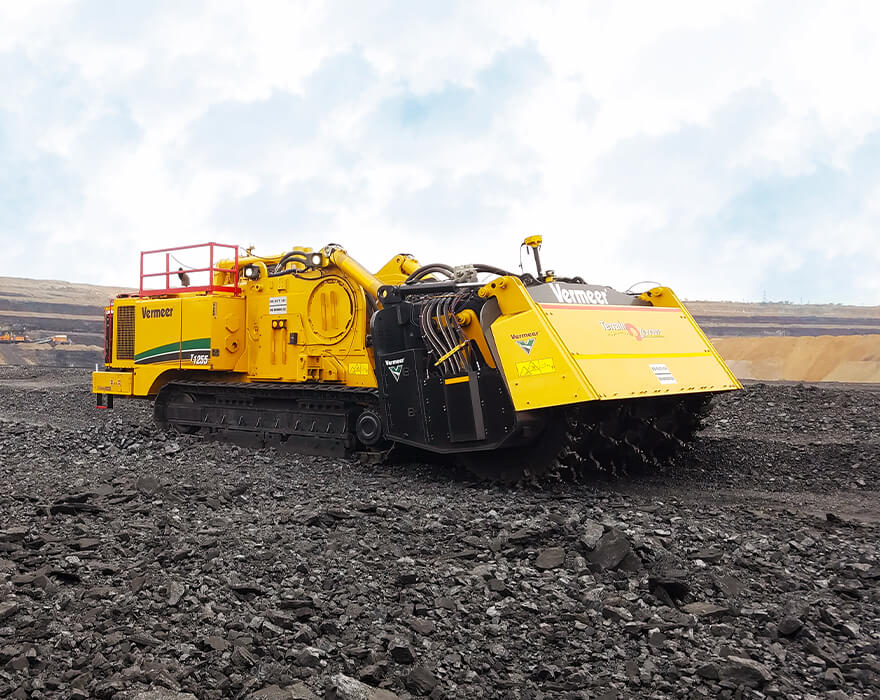
How surface miners work
Awareness of surface miners is growing, but an explanation of their technology is still helpful. Machines vary by manufacturer, but most move on tracks while a cutting drum with teeth cuts material into a consistent-sized product as it rotates. An operator can control product size by adjusting the depth of the cut and the speed of the machine. There are machines on the market that can cut a swath 15 ft (4.6 m) wide and nearly 30 in (76.2 cm) deep in a single pass.
Some surface miners can be equipped with GPS for precision cutting, allowing an operator to use the full length of the drum and minimize the overlap with each pass. Additionally, quarries can be surveyed and a flitch plan can be created.
Quarries face restrictions on explosives
Surface miners are making a name for themselves as regulations surrounding drill and blast methods grow globally. The United States has always maintained high restrictions that are always increasing. Other countries, including China, Brazil and most European nations, are rapidly becoming more restrictive about where drill and blast can be used.
Many of the reasons for this are environment related, including efforts to reduce noise, vibration and dust.
First, surface miners machines are quiet compared to drill and blast methods and create minimal vibration.
Dust is another major concern at many quarries. Some surface miners, like Vermeer Terrain Leveler® surface excavation machines, can be equipped with a dust suppression system. It uses two large vacuums to continuously pull dust from the enclosed cutting head into baghouses. The collected dust is then purged to help minimize the amount that enters the air. This continuous vacuum system minimizes the need to source water for dust control, helping to gain productive time that was once spent filling a water tank.
Quarries can also encounter issues with water tables. For example, a quarry may want to lower its floor, but drilling and blasting carries the risk of fracturing the layer between the floor and a water table. This could flood the pit and render it useless. A surface miner can more precisely undertake that process.
Additional benefits of using surface miners
Not only can surface miners help quarries extract maximum material, but this aggregate mining method also has several ancillary benefits.
A big one is a reduced need for, or even elimination of, primary crushers. The large material left after drilling and blasting must be processed by a primary crusher. But a surface miner creates smaller particles that may not need to go to a primary crusher. This, in turn, lowers the need for large loaders and haul trucks to transport the material to crushers.
A surface miner may allow for more material to be placed in trucks and loaders because the small, consistently sized product uses less space than the larger materials from drilling and blasting. Plus, using a surface miner may help a quarry to get to market faster. The infrastructure and planning needed for drill and blast — conveyer systems, purchase and setup of large equipment like primary crushers, and permits — can take years.
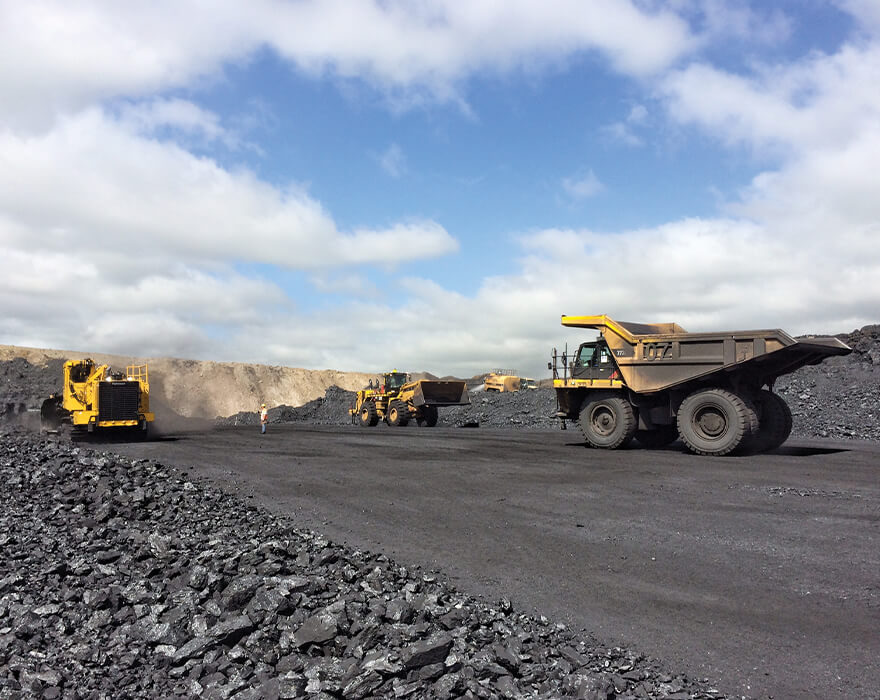
Evaluating aggregate mining methods
A quarry can take several steps if it wants to explore the possibility of using a surface miner. First should be analyzing rock samples to determine whether a surface miner is a good fit.
Next is a more in-depth analysis, with a specialist sent to the quarry to survey the site to do a point load test and perform other inquiries to further determine if a surface miner will fit the quarry’s needs. Information also is collected to help estimate production and the cost per ton.
Surface miners work best in long pits because that minimizes turnaround. It’s recommended that quarries look for machines that can turn on their axis instead of taking long, dramatic turns.
Another thing to consider is whether a machine can cut along a highwall. If drilling and blasting was used at a site, it probably has a highwall. Not all surface miners can extract material close to a highwall.
Aggregate mining options
As there is a growing interest from quarries from around the globe that are seeking alternatives to drilling and blasting, surface miners can help those customers maximize their productivity and efficiency.
For information about Vermeer Terrain Leveler surface excavation machines, contact your local Vermeer dealer.
Vermeer Corporation reserves the right to make changes in engineering, design and specifications; add improvements; or discontinue manufacturing at any time without notice or obligation. Equipment shown is for illustrative purposes only and may display optional accessories or components specific to their global region. Please contact your local Vermeer dealer for more information on machine specifications.
Vermeer, the Vermeer logo and Terrain Leveler are trademarks of Vermeer Manufacturing Company in the U.S. and/or other countries. © 2023 Vermeer Corporation. All Rights Reserved.