Wood waste recycling makes sense for Langley, British Columbia, propagated plants producer
Simple math — that’s the answer Leo Benne of Bevo Farms provides when asked why North America’s top propagation company got into the wood waste recycling business. With 48 acres (19.4 hectares) of greenhouses in Langley, British Columbia, and another 5.5 acres (2.2 hectares) in Pitt Meadows, British Columbia, it takes an incredible amount of energy to keep Bevo Farms’ facilities at the right temperatures during the colder months of the year. So when natural gas prices began to rise in the early 2000s, the company began considering alternative fuel sources and added a wood boiler for its heating system — a decision that eventually led Bevo Farms into the wood waste recycling industry.
Who is Bevo Farms and what is propagation?
The words “farm” and “propagation” are two terms not typically associated with the wood waste recycling and biofuel industries, and Leo Benne, president and general manager at Bevo Farms, wouldn’t classify his organization in those industries either. Instead, Benne is focused on producing hundreds of thousands of tomato, pepper and cucumber plants, more than 65,000 chrysanthemums, 100,000 poinsettias, plus thousands of annuals such as geraniums, begonias and dahlias each year. After Bevo Farms’ staff nurture the plant seedlings to an ideal level of development, the plants are distributed to greenhouses, field farms, nurseries and wholesalers across the continent, and that’s what a propagation plant producer does.
Bevo Farms has been in the propagation business for more than 30 years, and over that period of time perfected its craft of producing quality and healthy plants. Benne says the company has also developed new types of plants and unique machinery. “We’ve never been an organization to shy away from a challenge and are constantly looking for ways that we can improve our processes,” said Benne. “For example, we developed a cubic farming machine that can hold up to 2,700 lettuce or basil plants at one time, growing them to maturity every 21 days. It’s an innovation that helps us produce more plants for less money — something our customers certainly appreciate.”
It’s that level of customer focus that led Bevo Farms to invest in a wood boiler and eventually its own Vermeer® HG6000TX horizontal grinder.
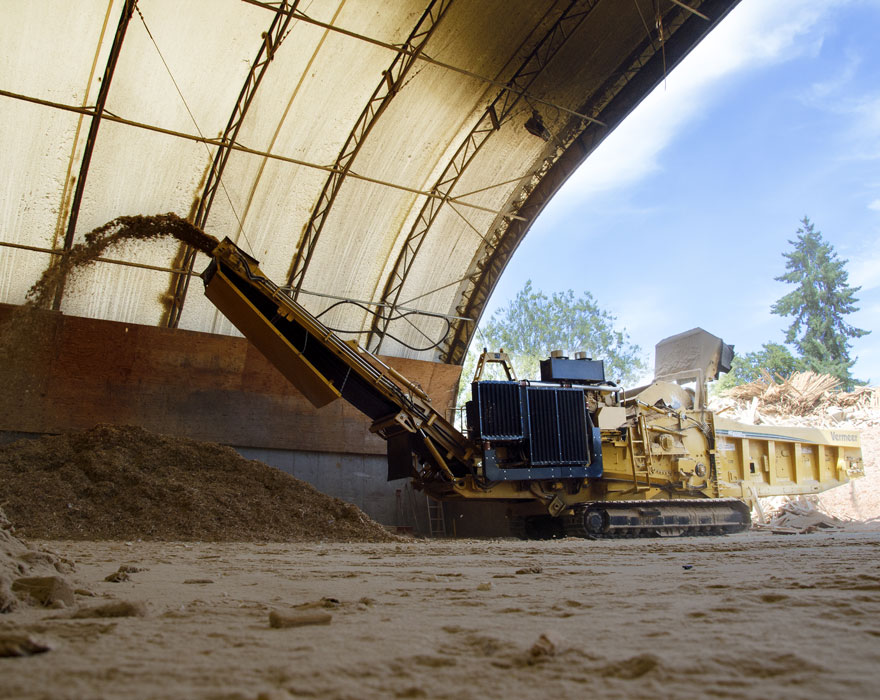
Getting into wood waste recycling
“Natural gas prices are what got us looking at wood as an alternative fuel source,” said Benne. “We started off buying and burning primarily cedar shavings for the first five to six years. We weren’t happy about the effect the cedar shavings were having on our boilers. There was a lot of maintenance because it’s quite a harsh fuel to burn. Around that time there were a lot of companies in the area investing in wood boilers, which put a strain on the availability of cedar and drove up the cost. It was then we decided to take the process in-house.”
From there Bevo Farms purchased an electric high-torque, low-speed grinder, before making the upgrade to the current Vermeer HG6000TX horizontal grinder.
“As we grew, so did our needs,” said Benne. “Doing the math, we determined we would be a lot more efficient with the Vermeer horizontal grinder than what we were getting from the electric one. Not only do we get more production out of the unit, but it does a much better job of producing consistent material sizes which gives us a better, cleaner fuel source.”
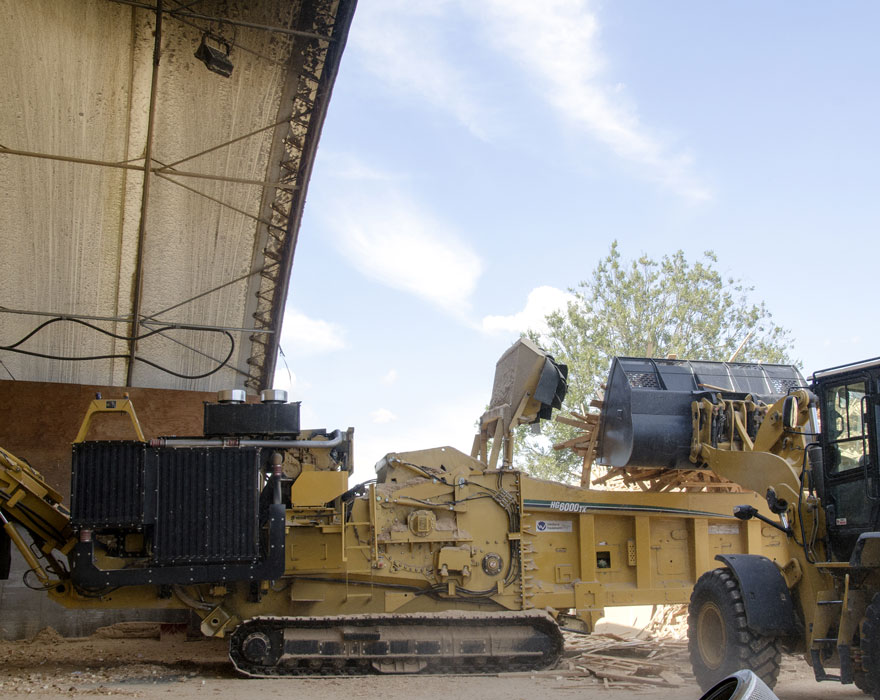
The efficiency of the Vermeer HG6000TX grinder helped reduce Bevo Farms’ costs and overall maintenance expenses. “We get our material from a local trucking company that hauls away waste wood from area mills and other businesses,” explained Benne. “The scrap material we’re working with includes pallet and sawmill waste primarily. Most of it is relatively clean, but occasionally there can be some metal debris mixed in. With our previous grinder, if we didn’t catch that material, we would have spent the next two hours changing teeth — that got old quick. Our Vermeer horizontal grinder does a much better job of handling the variety of materials we process through it.”
The Vermeer patented Series III duplex drum with reversible hammers and cutter blocks is one of the reasons Bevo Farms’ HG6000TX horizontal grinder provides better performance. This proven design can nearly double the wear life contractors get from hammers and cutter blocks, which helps to simplify and extend required maintenance. The thrown object deflector (TOD) helps to limit the amount and distance debris is thrown during operations – something that Benne says is important to them while running the machine.
While Bevo Farms’ horizontal grinder primarily operates onsite, the company did select to go with a track-driven model. “Having tracks just makes maneuvering the grinder much easier,” said Benne. “Having the ability to reposition the machine quickly and with less people saves us time and money.”
Supplying others with biofuel
After adding the horizontal grinder to its equipment fleet, Benne said they began to produce more material than what they needed to heat their operations – that’s when they started selling the extra to other companies in the area. “We used to have to hire another company to come in to help us grind from time to time, just so we would have enough material to make it through the cold season,” he explained. “Now, we more than keep up and can fill our large storage areas and sell the rest, which helps offset the cost of having a dedicated person running that operation for us. It also helps keep our costs low and allows us to help other companies get what they need.”
Bevo Farms runs its grinding operation year-round, and has been able to work with its raw material provider to secure all the additional wood waste material they need to keep their grinder busy creating biofuel material. “We’re pleased with the end product the grinder produces,” added Benne. “It burns cleaner than the cedar shavings we used before, which helps reduce maintenance time and expenses on the wood boiler. I’m happy we made the switch.”
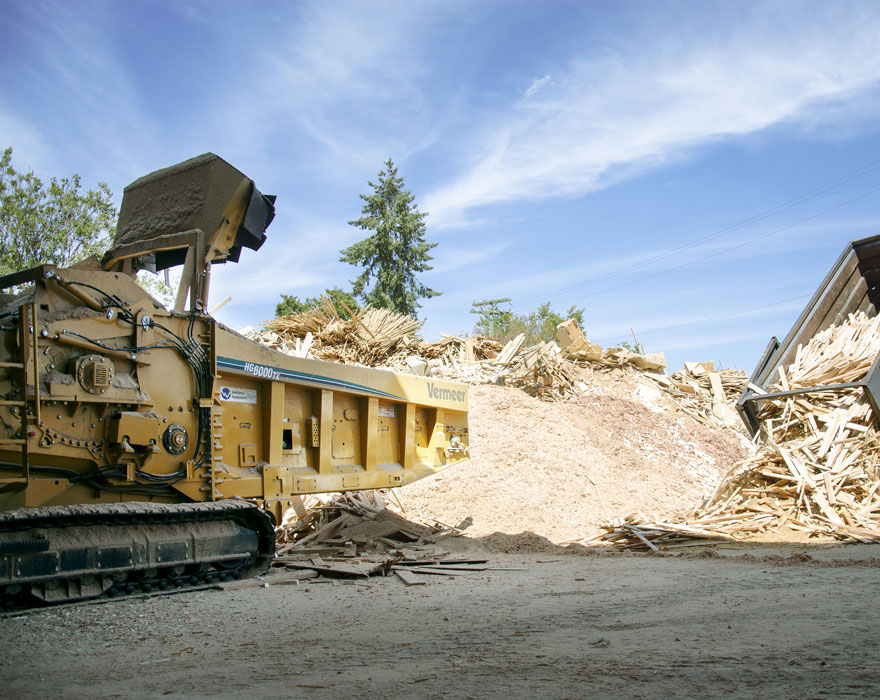
Fluctuating fuel prices
In recent years the price of natural gas has dropped significantly putting pricing more in line with what it costs to produce biofuels. It’s a trend that Benne has paid a lot of attention to. “By having both a natural gas and wood boiler, we can make decisions quickly depending on the price of natural gas at the moment,” he explained. “However, we all experienced how fast prices can change, which is why we will continue to produce biofuel material no matter what the current price is. We want to make sure we always have enough supply for our expanding operations, and whatever we don’t use, we can turn around and profit from.”
While Benne may never consider his organization to be a producer of biofuel, his innovative mindset has helped keep Bevo Farms’ operating costs low, so they can do what they are the best at — propagate high-quality plants for their customers.
“It all comes down to the math,” Benne concluded.
This article contains third-party observations, advice or experiences that do not necessarily reflect the opinions of Vermeer Corporation, its affiliates or its dealers. Testimonials and/or endorsements by contractors in specific circumstances may not be representative of normal circumstances experienced by all customers.
Vermeer is a trademark of Vermeer Manufacturing Company in the U.S. and/or other countries.
© 2017 Vermeer Corporation. All Rights Reserved.