You can’t rush the composting process. It takes months of diligently turning the material to produce a nutrient-rich, raw mix that’s ready to be separated and sold. When it’s time to screen that mix, selecting the right type of trommel screen will help you better meet the needs of your customers and maximize the value of your end product.
Trommel screens have become one of the preferred methods of separating different material sizes at composting facilities. While options for screening include deck screens and disc and star screens, trommel screens are the preferred method at many facilities because of their efficiency and ease of maintenance. Compared to disc and star screens, trommels don’t require as much maintenance because the technology heavily relies on gravity to move and screen material versus more mechanical means.
Drum options
The industry offers two configurations of trommel screens — a tensioned screen drum or an auger drum. Trommels with a tension screen drum use a lift-and-throw action to separate material. As compost is cycled through the drum, the smaller material passes through the holes of the screen while larger material exits at the end of the trommel. The slope of the machine dictates the rate at which the material flows through the drum as it’s tumbled. Using tensioned woven-wire screen panels allows the use of smaller gauge wire to increase the total open screen area, which helps increase production. However, tension screens are more susceptible to material spearing and more vulnerable to heavy contaminates like large rocks and concrete.
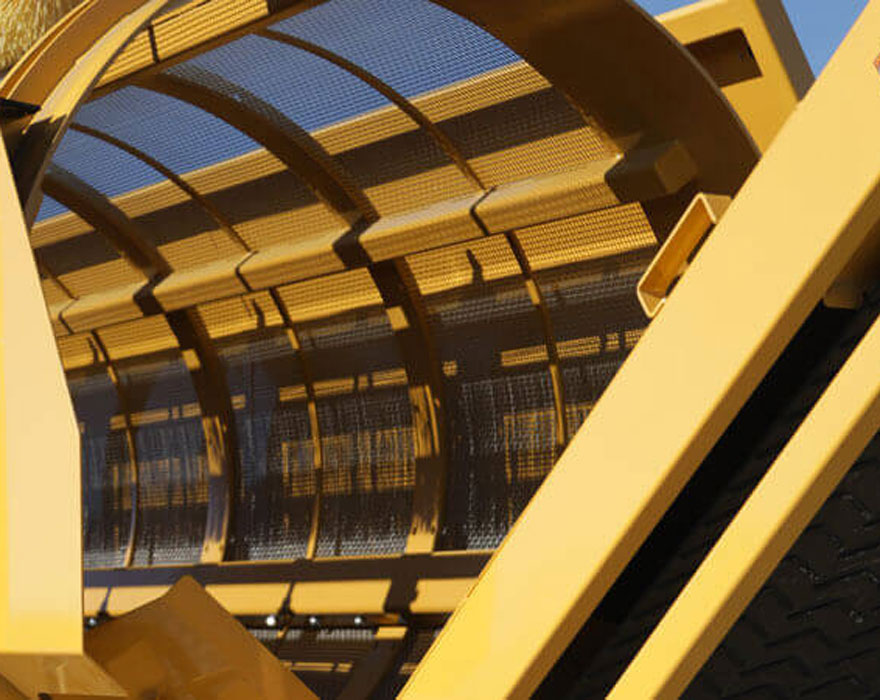
Trommels with an auger drum separate material using tumble-and-roll action, which reduces the chance of material spearing the screens. However, auger drums have less open surface area and are more prone to having wet material build up in the drum, and it can be more expensive to change product size due to needing an additional drum.
“When Vermeer first started looking to add trommel screens to our lineup, we did a lot of research as to what type of screen would deliver the best end product for our customers, while still being productive,” explained Ted Dirkx, applications specialist for Recycling and Forestry at Vermeer Corporation. “Based on that research, we began manufacturing a line of trommel screens that use tension screen drums, because they deliver a good balance of quality and quantity.”
Swapping out screens
One of the main benefits of a tension screen drum design is the ability to quickly and cost-efficiently swap or replace screens, rather than replace an entire drum. Depending on the make and model of the trommel screen, each tensioned screen can be changed out in as little as 30 minutes. On many auger drum trommels, the whole drum needs to be removed to change material sizing.
“At many composting facilities, changing screen sizes only happens every few weeks,” said Dirkx. “The design of the drum and tension screen system on Vermeer trommel screens help make that job more convenient. Operators only have to loosen five bolts to adjust the tensioning hook.”
Mixing and matching
Tension trommel screens range from 1/8 inch to 3 inches (.3 cm to 7.6 cm) in grid size and have the ability to mix and match different sizes on the same drum. “Some facilities will install a 1/2-in (1.3-cm) screen on the front sections and 3/8-in (1-cm) screens on the back,” explained Dirkx. “This setup allows them to optimize productivity without sacrificing quality. As the material separates throughout the drum, oversized material has more of a chance to fall through the screen, which is why they start to restrict the hole openings toward the rear.”
Dirkx explained that Vermeer recycling and forestry specialists will work with composting facilities, mixing and matching screens to help them optimize their setup. “Swapping out screen sizes can be more cost-efficient than having to purchase multiple drum sizes — a set of screens can be a third of the cost and more compact for transport and storage,” he said.
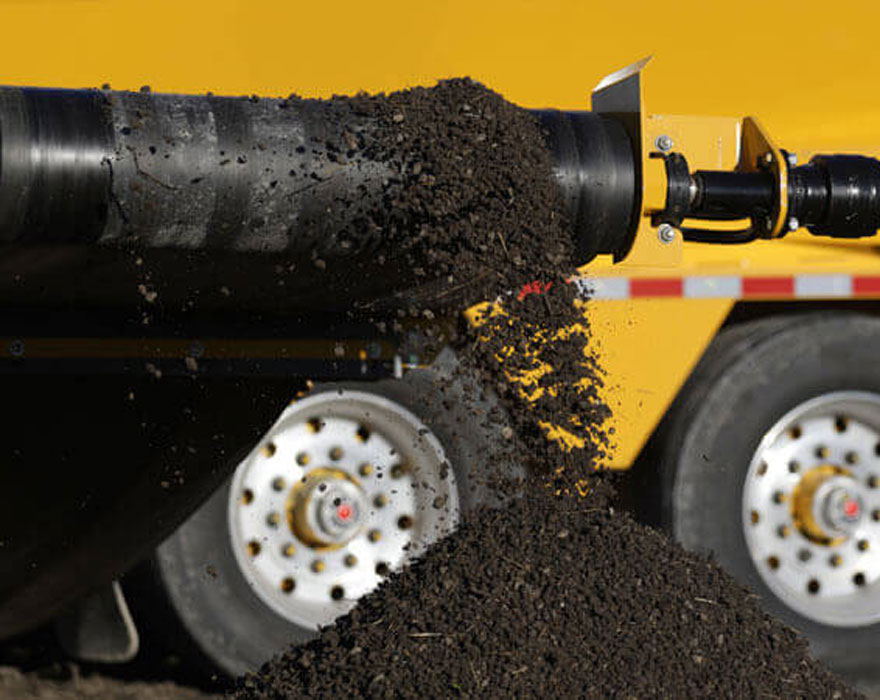
Screen construction
There are several reasons to choose a trommel with a tension screen drum, but you also want to make sure to select the right type. Woven together, the wire forms a panel that is available in a variety of sizes and wire gauges, depending on the desired end product and presence of heavy materials.
Several trommel screen manufacturers use bolt-on screens that get their strength and integrity through the use of thicker gauge wire, reducing the open screen and potentially impacting production rates. Vermeer trommel screens use a woven wire mesh that attaches to the drum and a tensioning system that pulls the screen tight — giving it greater rigidity to carry the load as it tumbles through the trommel. This design allows Vermeer trommels to use smaller gauged wire and get more open screen area for optimized throughput.
“We also offer stainless steel wire on our screens,” Dirkx added. “Finished compost is typically high in moisture — anywhere from 40% to 60% in most cases. Wet material is more likely to build up on screens, and we’ve found that stainless steel wire has a smooth surface that helps reduce the chance of material sticking.”
Choosing the right one
To choose the best trommel screen for your operations, Dirkx recommends starting the vetting process by researching manufacturers and the reputation of their dealer networks. “It’s always good to have the support of an expert when trying to get a trommel screen set up in your operation,” he explained. “On-the-job support is something people don’t have to worry about with Vermeer. We have an extensive global dealer network, and many locations have highly-trained recycling and forestry specialists on staff ready to help.”
Vermeer recycling and forestry specialists spend hundreds of hours every year visiting composting facilities to help keep their customers working as efficiently as possible. They can help you, too!
To learn more about Vermeer trommel screens, contact your local Vermeer dealer or visit vermeer.com/trommelscreens.
Vermeer Corporation reserves the right to make changes in product engineering, design and specifications; add improvements; or discontinue manufacturing or distribution at any time without notice or obligation. Equipment shown is for illustrative purposes only and may display optional accessories or components specific to their global region. Please contact your local Vermeer dealer for more information on machine specifications.
Vermeer and the Vermeer logo are trademarks of Vermeer Manufacturing Company in the U.S. and/or other countries.