Planning, operational awareness keys to creating a proactive maintenance culture
There’s no getting around the fact that routine equipment maintenance and upkeep takes time. But savvy operators can help minimize the duration of work stoppages — both expected and unexpected — by taking a proactive approach to equipment maintenance management for machines like horizontal grinders.
But what exactly does that mean? Proactive maintenance is generally about being more attentive to both your equipment and operating conditions and setting yourself up to act quickly and nimbly when a maintenance need arises, according to Vermeer Recycling and Forestry Application Specialist Ted Dirkx.
Get organized
It starts with good organization. With the knowledge of recommended daily inspections, maintenance and service tasks, you can organize tools in a way that help streamline those jobs so you can start up your horizontal grinder and get to work.
Routine maintenance is better conducted when you have the proper tools on hand or close to the jobsite where your horizontal grinder is working. Dirkx advises you to think about what maintenance may be required while on the job and keeping those essential tools on hand to perform the task needed in a timely manner.
“You can make it much more efficient by providing the tools necessary to do the job. One best practice is having an entire maintenance trailer or truck readily available for operators to have the tools and means necessary to maintain a horizontal grinder the way it deserves to be,” Dirkx said. “But you can really benefit by having a well-organized set of tools necessary to conduct routine maintenance without a lot of excess. Sometimes you want to have only the tools you need to do the job; it may not do you much good to have every tool under the sun on the jobsite when you have to sort through everything to find one wrench you need, for example. That can really slow you down in taking care of routine maintenance.”
Go for a walk
The next step in a proactive maintenance strategy for your horizontal grinder is simple: Go for a walk. As you inspect the machine prior to beginning work on the jobsite each morning, keep an eye out for signs of things like minor hydraulic leaks that could become more substantial maintenance issues if not caught early on. Proactive fixes like tightening loose hydraulic fittings where there’s evidence of even small leaks can enable you to tend to them as minor maintenance issues before they may turn major, Dirkx said.
“It goes without saying that a machine’s cleanliness is directly correlated with how well it’s maintained. If covered in dirt or dust all the time, it’s likely not being maintained well,” Dirkx said. ”Piles of debris will not only hide potential warning signs of an early failure but could cause corrosion issues. Discoloration or paint peeling in the frame or other components around a bearing indicates it’s getting hotter than normal and could foreshadow a more major maintenance issue that a proactive walkaround can expose.”
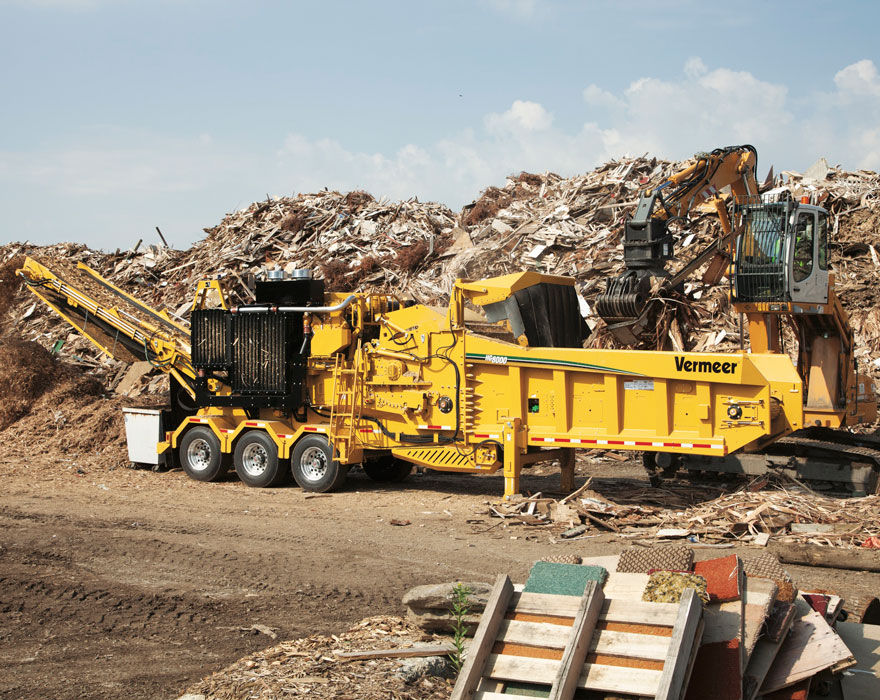
Operate by feel
A good operator uses all of his or her senses to tell if a horizontal grinder is functioning optimally. Oftentimes, even slight damage or wear to parts like the drum, hammer or conveyor will make its presence known in different vibration or output sizing. Damage like this can affect overall productivity. In building a proactive maintenance strategy, it’s typically best to assign one or a small number of operators to each grinder so that the subtle operational differences that precede a potentially disruptive issue will be repaired before reaching that point.
“You can tell a lot about drum and hammer wear and tear by the material coming off the conveyor. It just takes a good operator who spends a lot of time with his or her machine and who will check components like cutter tips two or three times a day. Good operators can absolutely feel, see and know the difference between the output of a machine with brand-new cutter tips, for example,” Dirkx said. “As a component of proactive management, the fewer the operators, the better the health of the machine. A single operator who grinds with that machine every day will know the nuances, whereas if you have five people taking turns on a machine, it may be harder for them to understand. That understanding is key to helping prevent minor issues from becoming major issues.”
Know your wear parts
Another area of focus in a proactive maintenance strategy is attention to wear parts, especially how different components fit together operationally and from a cost standpoint. Running cutter tips beyond their expected lifespan can inflict damage to the more expensive hammer component. Being attentive during operation and proactively replacing cutter tips before they reach that point is one tactic that contribute to a proactive overall maintenance strategy.
“I can be risky for an operator to try to milk out an extra four or six hours from a cutter tip because he or she doesn’t want to shut down to change the tips. You can push through that point in the name of productivity, but as soon as those tips are beyond their wear point and you start chewing into the hammer, you can do more long-term harm and add cost,” Dirkx said. “It’s hard to rationalize that in the short term because you’re being more productive. But over 5,000 hours, that can add up to significant additional operating costs.”
Another wear part that calls for frequent monitoring is the set of screens within a horizontal grinder. As they wear, openings expand, resulting in output that’s not sized accurately. Staying on top of screen condition and replacing when the operator notices grindings aren’t consistent in size is part of a proactive maintenance strategy.
“If your screens have 4-in (10.2-cm) squares when they’re brand new, output should be 4-in (10.16 cm). As they wear, those openings can stretch to closer to 5-in (12.7 cm), so your output will start to get bigger and stringy and you lose vital cutting surfaces,” Dirkx said. “The bars and metal around the screen will be rounded over and won’t be sharp cutting edges, so you can lose productivity and product quality.”
How are you loading your grinder?
More attentive, proactive equipment maintenance isn’t confined to the horizontal grinder itself. The equipment you use to load that grinder — and attention to how the machines interact in the process — can have a lot to do with its performance over time. Wheel loaders and excavators, for example, load material differently, and the process can have varied impacts on the long-term performance of belts, cutter tips and other wear parts.
“Typically, the heaviest contaminants shuffle their way to the bottom, so using a wheel loader with a grapple bucket loads in more of those contaminants. An excavator works from the top of the pile. The operator can see what he or she is grabbing,” Dirkx said. “An excavator with a bucket and thumb doesn’t load as many of those contaminants, and it’s even better with a rotating clamshell bucket that takes a more precise grab. You always want to avoid longer, larger-diameter branches hanging off the side of the grinder where it can scuff panels and potentially break off hydraulic lines.”
Create checklists and labels
A lot of work goes into a proactive equipment management strategy, especially for a machine with the number of components and systems like a horizontal grinder. As a way to get organized and streamline the process, Dirkx recommends referring to your operator’s manual to help create a daily checklist with only the high-priority components to check when conducting walkarounds prior to beginning work each day. The same is true with component labels; having things clearly labeled on the machine can help operators be more efficient with routine maintenance so they can get to work more quickly and efficiently.
“A checklist in a format that you can print off or apply as a decal on the machine near the operator’s station can make for a quick reference,” Dirkx said. “And it can be a big help to label everything on the machine — things like where to grease, how much fuel to add or where the operator should pay extra attention to cleanliness or lubrication. Labeling is a really inexpensive way to be more proactive with routine maintenance.”
Brush up on the different components of your Vermeer horizontal grinder. Contact your dealer to get your proactive maintenance strategy off the ground.
Vermeer Corporation reserves the right to make changes in engineering, design and specifications; add improvements; or discontinue manufacturing at any time without notice or obligation. Equipment shown is for illustrative purposes only and may display optional accessories or components specific to their global region. Please contact your local Vermeer dealer for more information on machine specifications.
Vermeer and the Vermeer logo are trademarks of Vermeer Manufacturing Company in the U.S. and/or other countries.