Maximize your grinder’s productivity by replacing wear parts at the optimum time
Diligent daily inspection of your horizontal grinder wear parts is one of the essential steps in maximizing its productivity. Your horizontal grinder can cut and size solid hardwoods one minute and soft stringy yard waste the next. But, to get the optimum production out of your grinder and consistent material sizing, you need to make sure you’re inspecting the wear parts involved with the grinding and cutting process daily, and in some cases, even more frequently. Refer to your machine’s maintenance manual for safety messages and further instructions.
“There are several wear parts working together to grind and size material on a horizontal grinder,” said Jeff Bradley, product manager for Vermeer Environmental Solutions. “Cutter tips, screens, the anvil, wear plates and mill bearings are the top five grinder wear parts that work together to size organic wood waste material properly. Neglecting any of these wear parts can cause premature wear to other grinder components or worse — a more costly repair.”
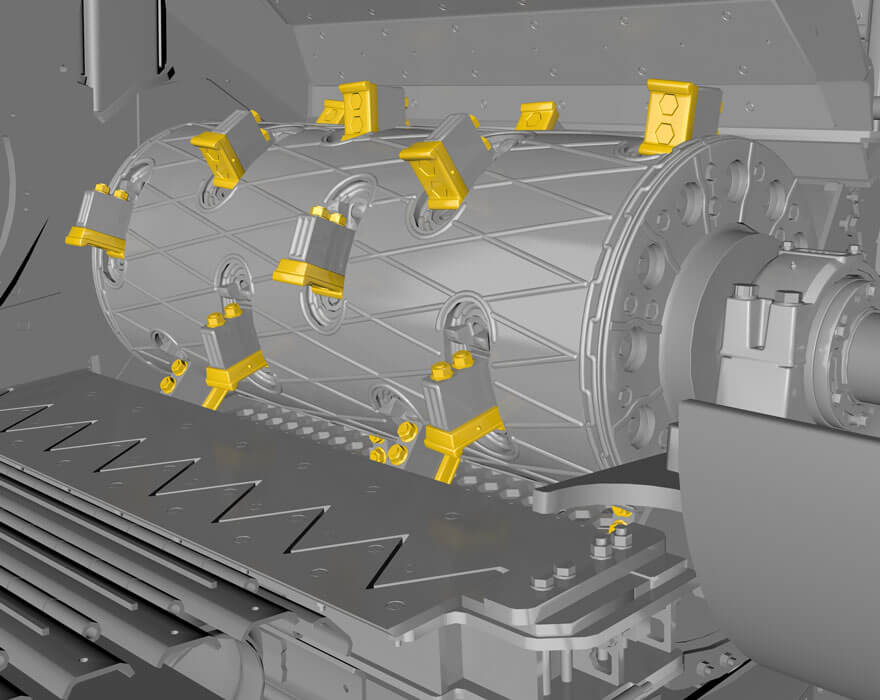
Grinder cutter tips
Cutter tips should be inspected, turned and replaced frequently. “It’s not just the type of organic waste sent through the grinder, but also what’s mixed in with it,” said Bradley. “Sand, small rocks and leaves are all common abrasive material that causes tips to dull. So, when working in areas where this type of material is common, it’s important to inspect and flip tips often.”
- What to look for: You want to flip the cutter tips when the carbide wears down and before it gets into the base material.
- When to replace: You need to replace the tips before they start to wear into the mount or hammer. A visual inspection is the best way to determine the condition of the tips. But, changes in material sizing is also an indicator to look out for when the machine is running.
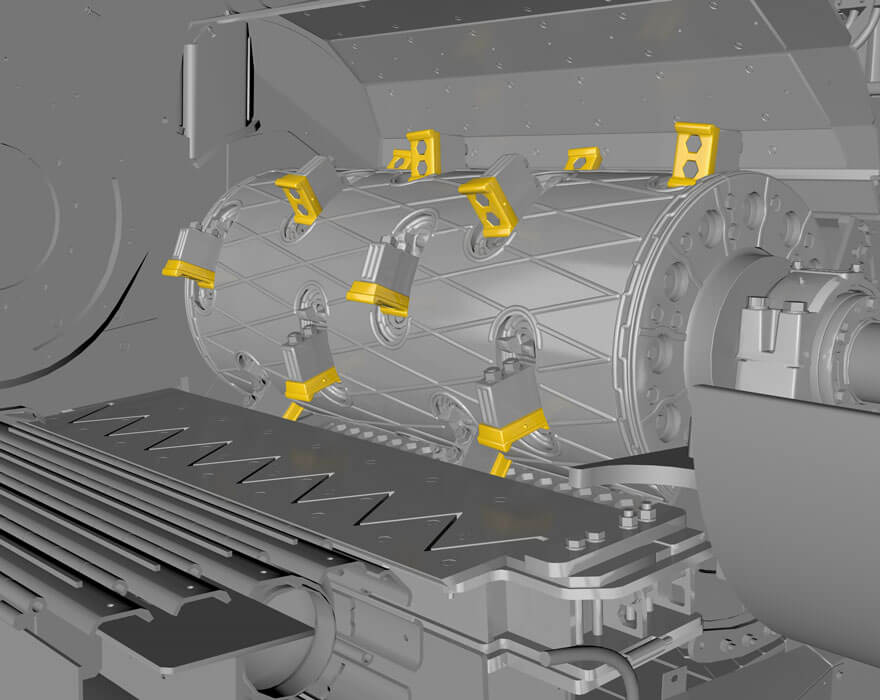
- Why it’s important: “Excessive wear to the tips can cause damage to tip mounts and the grinder’s hammer,” said Bradley. “If the tips get too thin, they can break off and potentially lead to more significant damage.”
- Proactive recommendation: Changing cutter tips should be done frequently, so Bradley recommends stocking these grinder wear parts.
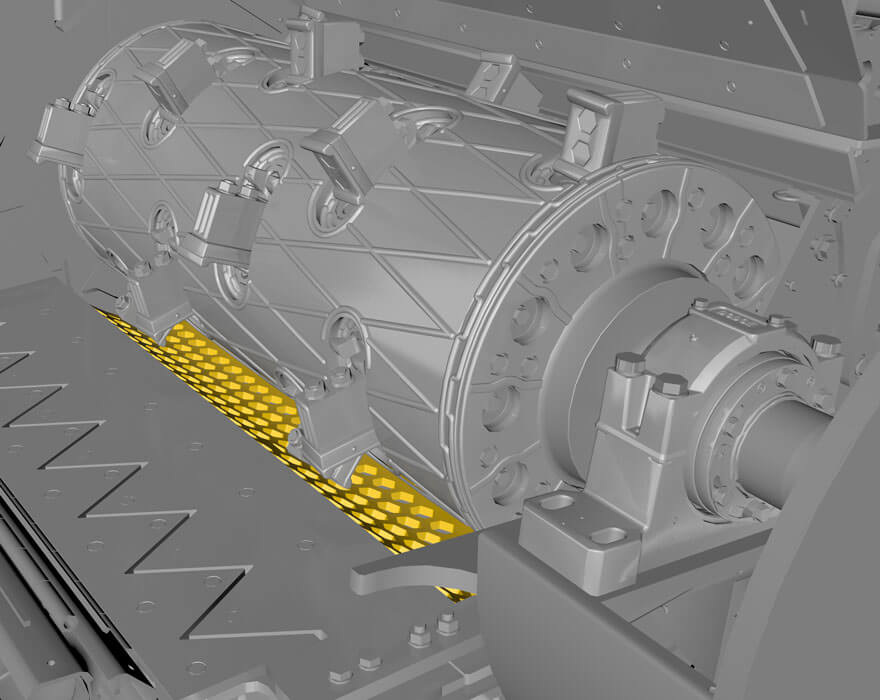
Grinder screens
Screens are responsible for helping to cut and size material. Screen wear over time will impact end product sizing.
- What to look for: Bradley said grinder operators should keep an eye on the material coming off the discharge conveyor to make sure the sizing is consistent. “Inconsistent sizing or larger sizing than what should be coming off the conveyor is a good indicator of worn-down screens. While visually inspecting the screens, the operator should measure the hole openings and look for damage.”
- When to replace: It’s time to replaces screens when hole sizes begin to stretch, screens are thinning, or there is damage to a section.
- Why it’s important: When screens become too worn, material will circle the drum more before it is sized and discharged, resulting in more fines and sizing inconsistencies. Also, if screens wear too thin, they can break, and you will lose your ability to control product size.
- Proactive recommendation: “Whenever the material or weather changes, grinder operators should ask themselves if the screens on their grinder are the right ones for the conditions that day depending on how critical your end product sizing requirements are. This is one grinder wear part that companies should stock in several different sizes and patterns,” recommends Bradley.
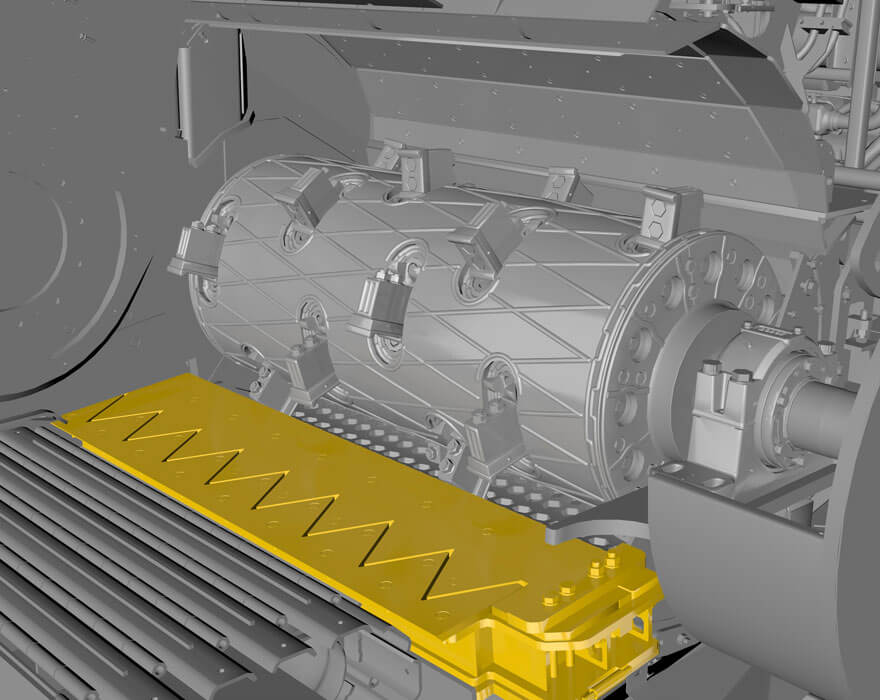
Grinder anvil
The anvil works in conjunction with the hammers and tips to cut incoming material. A dull anvil edge can change the grinder’s sizing capabilities and increase material recirculation.
- What to look for: You need to do a visual inspection of the anvil to make sure the edge looks smooth and ready to cut. The sharper the edge the better product sizing it will do. Some anvils are adjustable, and as the edge wears, it may need to be repositioned closer to the mill.
- When to replace: When the anvil appears to be dull, the hard facing is worn off, or it is wearing thin, it’s time to replace or rebuild this grinder wear part.
- Why it’s important: Using a worn-out, dull anvil can hurt production rates and lead to more fines in your end product. And eventually, if the anvil wears too thin, there can be damage to the support structure underneath, which would require a much more extensive repair.
- Proactive recommendation: Bradley recommends that horizontal grinder owners have an extra anvil on hand. “Often, anvils can be rebuilt and put back on the machine,” he said. “So, keeping an extra one on hand to swap out with the one on the grinder can help maximize efficiency.”
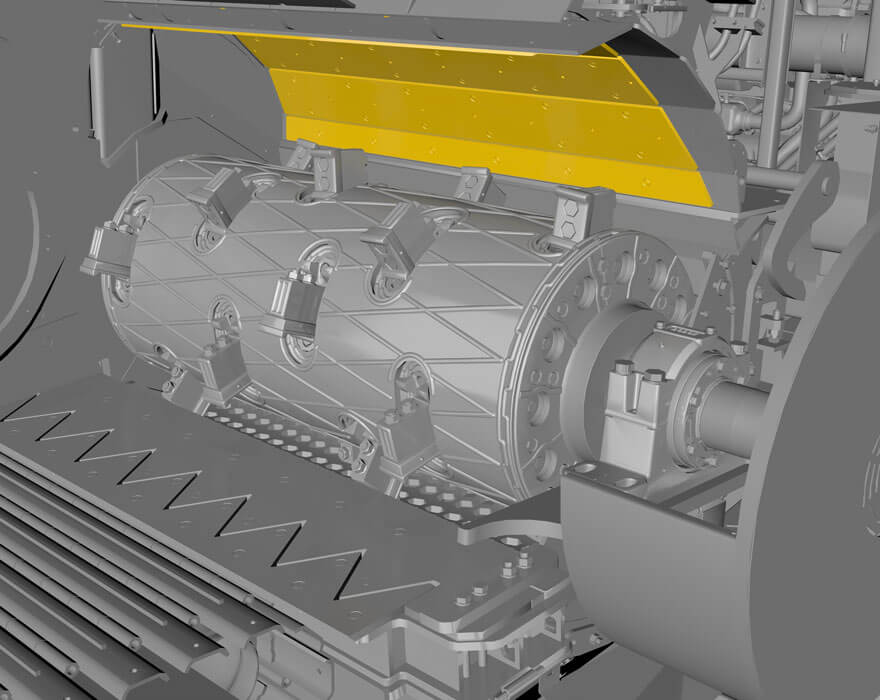
Mill wear plates
All materials will be processed through the mill of a horizontal grinder. Over time the mill’s metal wear plates will wear down. Located on each side of the mill, wear plates help prevent damage to the mill structure, so you may only need to replace wear parts instead of rebuilding the whole milling area.
- What to look for: “Operators should look for how thin the wear plates are and if the that hold them in place are thinning. If there is more than a 1/4 inch (6.4 mm) of wear, it’s time to replace them,” said Bradley.
- Why it’s important: Mill wear plates are there to wear out to help prevent the structure behind them from being damaged. If the mill plates become too thin, bolts can break and may send the wear plates through the mill itself.
- Proactive recommendation: According to Bradley, stocking mill wear plates is a good idea for horizontal grinder owners working with a lot of abrasive material. However, if the operator is inspecting these grinder wear parts regularly, there should be plenty of time to contact your local Vermeer dealer to order replacements.
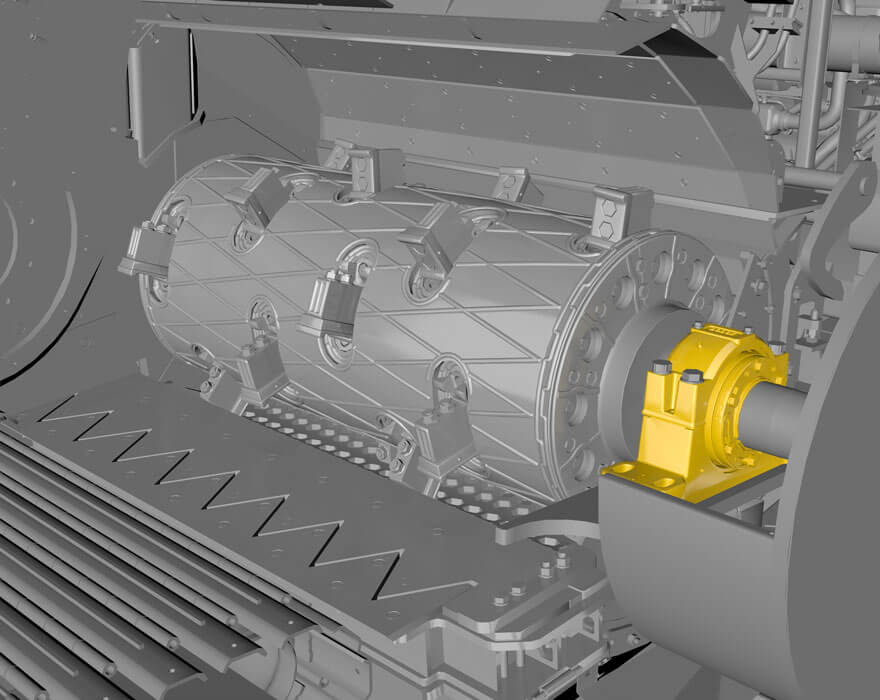
Mill bearings
Harder to inspect but vital to your grinding operation, the temperature of your horizontal grinder’s mill bearings should be checked daily.
- What to look for: You’re looking for temperature consistency. Temperature fluctuations can be an indicator of under or over greasing the bearings. “Regularly taking temperature readings can help alert the operator to potential issues with mill bearings,” said Bradley. “If the temperature starts to climb, it may be an indication of a few potential issues such as not enough grease, too much grease or bearing issues. It is critical to follow the manufacturer’s suggested greasing intervals as well as volumes to maximize the bearing life. If the temperature doesn’t come back into a normal range after greasing the mill bearings, further inspection of the bearings should be done to determine if they need to be replaced.”
- Why it’s important: “If a mill bearing ceases, it can weld itself to the drum shaft,” said Bradley. “When that happens, the drum shaft will also have to be replaced.”
- Proactive recommendation: Bradley recommends talking with your dealer about their grinder wear parts inventory when it comes to mill bearings. “Bearings wear out over time, so if the grinder operator is checking temperatures daily, there should be plenty of time to get replacement parts ordered.”
Monitoring the conditions of these five horizontal grinder wear parts and proactively replacing them when necessary will help maximize productivity and help prevent more extensive repairs down the road. Bradley’s final recommendation is to have an ongoing dialogue with your Vermeer dealer to determine which common wear parts they have in stock and which ones you should keep on hand.
For more information about horizontal grinder maintenance, refer to your machine’s maintenance manual or contact your local Vermeer dealer.
Always refer to the product’s maintenance and/or operator’s manual for safety messages and further instructions. Vermeer Corporation reserves the right to make changes in product engineering, design and specifications; add improvements; or discontinue manufacturing or distribution at any time without notice or obligation. Equipment shown is for illustrative purposes only and may display optional accessories or components specific to their global region. Please contact your local Vermeer dealer for more information on machine specifications.
Vermeer and the Vermeer logo are trademarks of Vermeer Manufacturing Company in the U.S. and/or other countries.
© 2021 Vermeer Corporation. All Rights Reserved.