Trommel screens are efficient at sizing and separating compost, mulch, blended topsoils and aggregates. With only a few moving components involved with sorting material, these machines are also efficient to maintain.
Good maintenance practices, outlined in your trommel screen’s operator’s manual, will walk you through the details to help you maximize the life of your machine. Included within those pages are also details about replacing common wear parts.
According to Ted Dirkx, sales manager for recycling and forestry equipment at Vermeer, paying attention to the condition and performance of screens, brushes and flashing on a trommel screen will help optimize the quality of your end product and help minimize wear on other machine components. “These areas of a trommel screen should be inspected regularly and adjustments or replacements should be done when there’s an issue,” he said.
Here are a few tips on what to look for while operating your trommel screen and the corrective actions you should take.
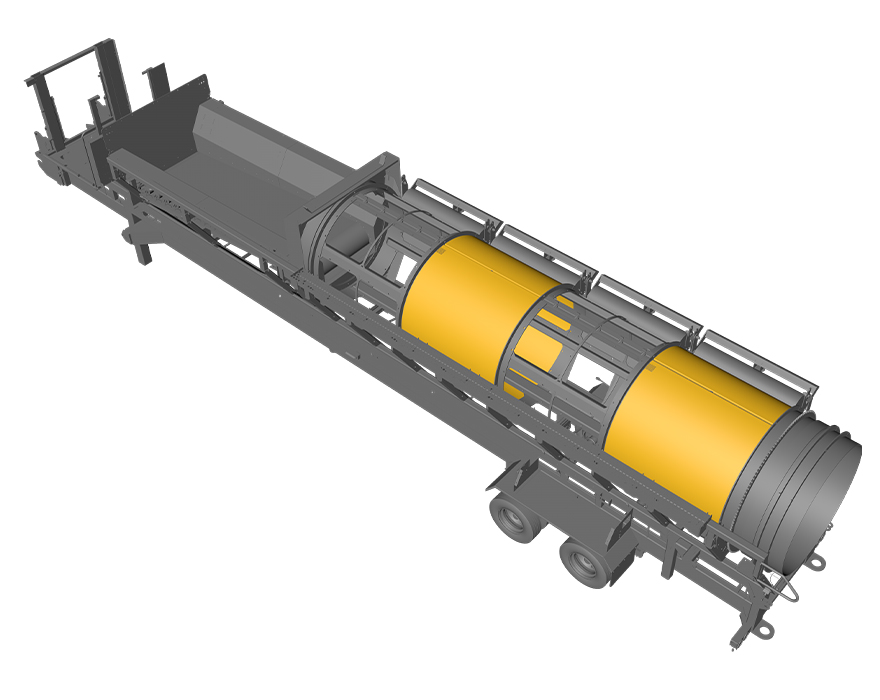
Screens
The screens of your trommel screen are crucial to producing quality end products, whether that’s compost, mulch, topsoil or aggregates. So, you need to prevent your screens from blinding and keep them free of rips and tears.
Screen blinding
When screening wet, dense material, screen holes can become covered and prevent fines from passing through. This can reduce the volume of fines separated since more of it exits with the overs.
- What to look for: You should pay attention to the moisture levels in the material being processed, and if you see that holes are being plugged up, it’s time to take corrective action.
- What to do first: Look at the position of the brushes on your trommel screen. Do they need to be adjusted or replaced in order to clear material from the screen?
- What to do next: When working with wetter material, sometimes having a good set of brushes isn’t enough to keep screens from blinding. If that’s the case for you, you should consider swapping out standard steel screens for stainless steel ones. The rough surface of regular steel gives wet material something to stick to, whereas stainless steel screens have a smoother surface, making them more efficient at keeping material moving. You may also want to consider using a thinner gauge of wire since there will be less surface area for material to build up on, which also means material has more hole openings to pass through.
Screen rips and tears
While screen blinding can result in fines not getting through screen holes, rips and tears in the screen can allow too large of material through onto your fines pile.
- What to look for: Whenever you’re sorting aggregates or material with contaminates, you should check the conditions of your screens frequently. Seeing overs in your fines pile is a good indicator that there may be a rip or tear in your screens.
- What to do: Replace any screen panels that have rips or tears to maintain a quality end product. If rips and tears become a regular issue, you may want to consider using a heavier gauge screen on your next set of screens, but keep in mind this could slow material throughput.
- Preventable actions to consider: Keeping contaminates and oversized rocks from entering the trommel in the first place is another effective way to get the most from your screens. In addition to pre-sorting material for objects that can damage screens, you may also want to add a set of grizzly bars to your trommel screen’s hopper. Many Vermeer trommel screen models offer grizzly bars as an option for those working with aggregates that have contaminates like concrete and metals.
Expert advice: “Screen material and wire gauge can impact production rates,” said Dirkx. “Smaller gauge wire gives trommel screens more openings for shorter throughput times. Choosing stainless steel screens can also help optimize production time because the smooth surface helps prevent material from sticking while tumbling through the trommel.”
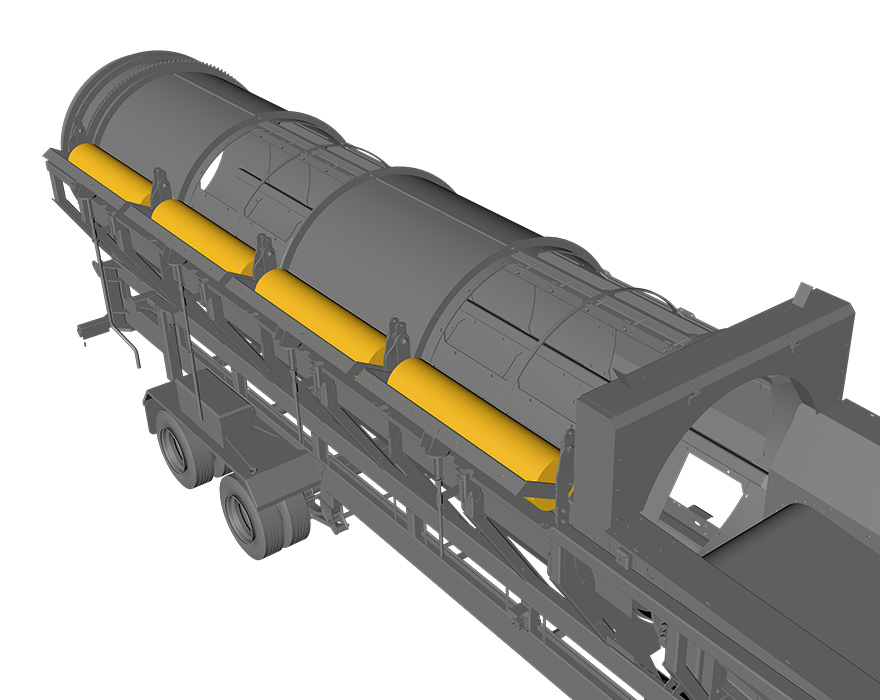
Brushes
The brushes on your trommel screen are another essential wear part to pay attention to in order to optimize production. Trommel screen brushes help prevent material from blinding screen holes when working with wet material. Worn-out brushes or ones not properly adjusted can affect production rates and fines volume.
- What to look for: You should look at two things to determine whether it’s time to replace or adjust your trommel screen’s brushes. First, look at the bristles. You don’t want them to be frayed or folded over because that can impact how well they penetrate screen holes to dislodge stuck material. Second, you want to check how they align inside of the drum. You want about 1/4 in (6.4 mm) of the bristles sticking through the drum to effectively clean each opening. Anything more could result in premature wear.
- What to do: When it’s time to replace brushes, consider choosing ones with poly-tipped bristles instead of nylon brushes that tend to fray, soften and bend over time. Poly-tipped brushes provide rigidity for clearing screen openings and can keep their shape longer. Remember, brushes aren’t there to sweep the outside of the drum — they’re there to help prevent wet material from plugging up screens.
Expert advice: “To get maximum life from a set of brushes, operators should make sure they’re adjusted appropriately for the material being sorted,” said Dirkx. “Setting brushes too close to the drum can result in premature wear without any real added benefit. Also, if the material being run is dry, brushes may not be needed at all.” If you’re working with wetter materials, Dirkx recommends going with a double brush for twice the brushing action to clear screens when blinding occurs.
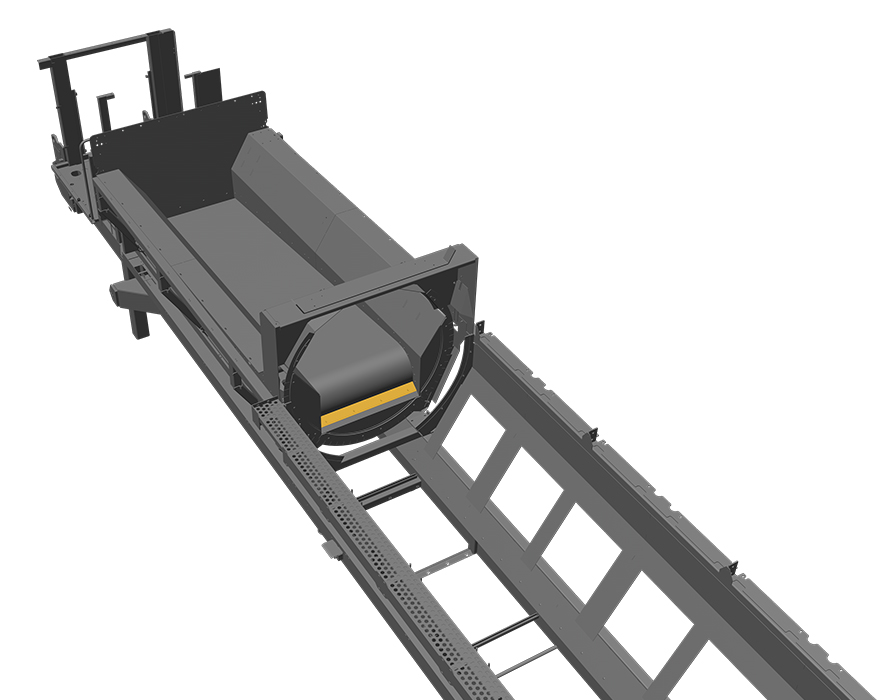
Flashing
Flashing is the rubber skirting along conveyor belts and the vertical sides of the machine. It acts as a barrier to keep material where it’s supposed to be. When flashing wears out, material can leak from the intake conveyor to the fines conveyor or build up under the machine. This can impact the quality of the end product and result in the loss of valuable material out the bottom of the machine.
- What to look for: If you see material building up under your trommel screen or overs in your fines pile, you may have an issue with flashing. If that occurs, look around your machine conveyors for gaps around the conveyors.
- What to do: If there are gaps between the belts and machine, you need to adjust how the flashing is sealing and replace it when adjustments can’t be made.
Expert advice: “If there’s an issue with flashing, operators should look into potential causes,” said Dirkx. “In some instances, damage to the flashing may have been caused by oversized material or other contaminants damaging the rubber seals when inadvertently being dumped into the hopper.”
Paying close attention to the performance of your trommel’s screens, brushes and flashing can help you optimize the throughput of your trommel screen to create quality end products. In most cases, adjustments can be made when there’s an issue, but sometimes, your next step may be to replace one of these wear parts. Taking these steps will help keep your team producing.
Vermeer Corporation reserves the right to make changes in product engineering, design and specifications; add improvements; or discontinue manufacturing or distribution at any time without notice or obligation. Equipment and depictions shown are for illustrative purposes only and may display optional accessories or components specific to their global region. Please contact your local Vermeer dealer for more information on machine specifications.
Vermeer and the Vermeer logo are trademarks of Vermeer Manufacturing Company in the U.S. and/or other countries. © 2022 Vermeer Corporation. All Rights Reserved.