The process you employ to recycle organic waste to produce landscaping materials like compost, mulch and soil blends can significantly impact your overall operating efficiencies. The more times material is moved and the way you move it can hurt your business’s productivity. So, the key to optimizing recycling organic waste and producing landscaping materials is minimizing your efforts in moving material throughout the process.
According to Ted Dirkx, sales manager for recycling and forestry equipment at Vermeer, the top compost, mulch and soil producers he’s visited throughout his career all have one thing in common — they scrutinize every step in their production process. “From optimizing the layout of their facility to minimizing the number of times organic material has to be handled to employing more efficient ways of moving it, producers are always looking for the best way to improve the process,” he said. “This quest to streamline everything has resulted in the reduction of the number of machines and people needed while speeding up production times and/or compost curing times.”
Vermeer recycling and forestry specialists and the Vermeer product development team have helped many landscaping material producers and organic wood waste recycling operators streamline their process over the last three decades. Their efforts include developing a range of horizontal grinders, tub grinders, trommel screens and compost turners to match the specific needs of producers and partnering with MGL Engineering, so Vermeer dealers can deliver an even broader range of equipment solutions.
Introducing Vector material handling equipment
Vector material handling equipment built by MGL Engineering is now available at select Vermeer dealerships throughout North America. The Vector product line includes wheeled and tracked stacking conveyors ranging from 50 to 80 ft (15 to 24 m) in length, the 80-ft (24-m) Site Boss feeder/stacker, the 725 ColorMax coloring system for mulch and rock, and the VacMax air separator.
“The Vector product line complements Vermeer environment equipment and is supported by Vermeer dealers,” said Dirkx. “Now, our dealer network has even more ways they can support organic waste recyclers and landscaping material producers.”
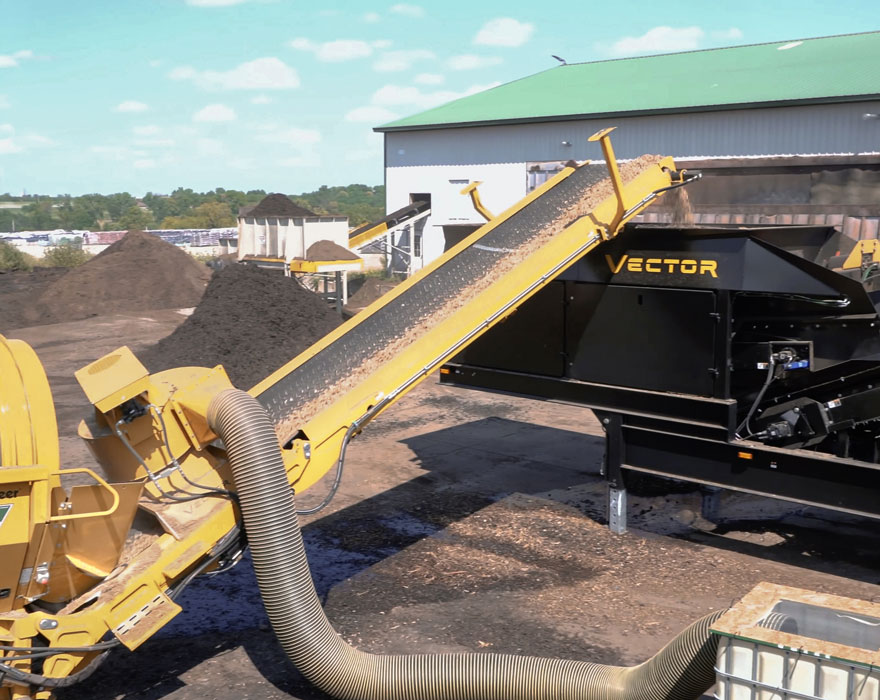
Moving landscaping materials
Wheel loaders are a necessity for landscaping material producers throughout the production process. Loaders are often used with excavators to help sort and load organic waste into a grinder’s infeed, as well as transport and stack the material after it’s sized. If additional processing is required (screening and/or colorizing), wheel loaders usually are employed to handle the bulk of the work. The challenge is that all these steps are often happening all at once, so multiple wheel loaders and operators are required to make the whole process run smoothly.
But it doesn’t have to be that way.
Stacking conveyors can help you minimize the number of wheel loaders operating at your facility. Instead of moving processed material one bucket at a time, a stacking conveyor can move much more material with far less movement and labor involved.
“Using a Vector VX (wheeled) conveyor or VT (tracked) conveyor can help minimize the number of steps involved in producing compost, mulch or soil blends,” explained Dirkx. “Conveyors can be paired with a grinder to stack material higher and closer to your compost rows or retail yards, helping streamline the production process. Also, since the units are diesel powered and on wheels or tracks, they can quickly be moved from one area of operation to the next.” In addition to operating efficiently, once these Vector conveyors are in position, there’s very little input required from an operator. In most situations, the operator feeding material into the grinder can also monitor material moving on the conveyor and make adjustments when needed.
Optimizing mobility
For optimal mobility when handling material, there is the Vector Site Boss feeder/stacker. This unit features a large infeed hopper with a working length of 88 ft (26.8 m) and a maximum working height of 33.7 ft (10.3 m). An optional anti-bridging auger for the hooper is also available for efficient mulch production.
“The tracked Vector Site Boss can be moved around a facility using a handheld remote, making it more efficient to use one conveyor for every step of the production process,” Dirkx explained. “The machine’s large infeed hopper allows it to keep up with higher-production grinders and screen equipment, so producers can create end products fast and move them efficiently.
Coloring mulch
If you’re coloring larger volumes of mulch or aggregates at your landscaping material facility, you may want to check out the Vector 725 ColorMax. It can quickly process large volumes of material with minimal waste of colorant dyes. It’s powered by a diesel engine, so it can be transported to work where you need it, unlike many fixed-point electric colorant systems.
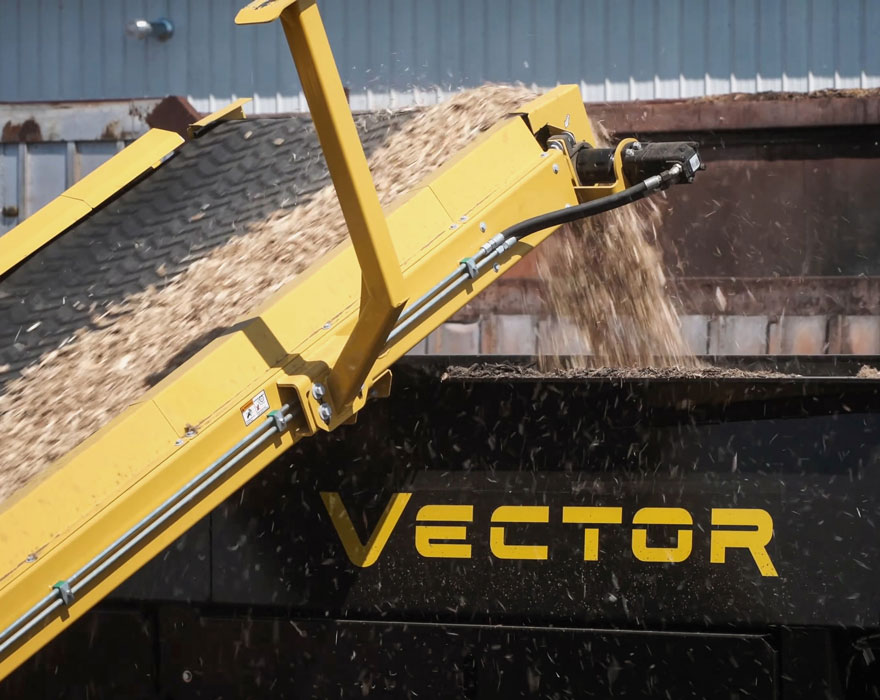
“Many mulch producers we’ve visited say the volume of colorant used impacts their operating efficiencies,” said Dirkx. “The design of the 725 ColorMax thoroughly mixes incoming material with the colorant for optimal dye coverage and helps minimize oversaturation. This results in a quality end product that stays light and efficient to transport.”
Minimizing plastics
For optimal contamination control while recycling organic waste and producing landscaping material, there’s the skid-mounted Vector VacMax air separator. “Light plastics are a major hassle at every recycling facility,” Dirkx said. “Customers don’t like opening a bag of mulch or compost and finding small pieces of plastics mixed in. The Vector VaxMax can help minimize the volume of plastic containments that find their way into finished end products. And it makes an ideal companion to Vermeer trommel screens.”
Find Vector equipment at Vermeer dealerships
Smartly designed and quality built, Vector material handling equipment can be found at your local Vermeer dealership.
Vermeer Corporation and MGL Engineering, Inc. reserve the right to make changes in product engineering, design and specifications; add improvements; or discontinue manufacturing or distribution at any time without notice or obligation. Equipment shown is for illustrative purposes only and may display optional accessories or components specific to their global region. Please contact your local Vermeer dealer for more information on machine specifications.
Vermeer and the Vermeer logo are trademarks of Vermeer Manufacturing Company in the U.S. and/or other countries. Vector is a trademark of MGL Engineering, Inc. © 2022 Vermeer Corporation. All Rights Reserved.