If you’ve owned a brush chipper (or several), you know they come in many different shapes and sizes. At the same time, there’s been a variety of features added and improvements made to them over the years. One of the changes has been between horizontal and vertical feed rollers. Some brush chippers have horizontal feed rollers and some have vertical.
There are benefits to both, and it largely depends on your preference, but let’s take a look at the difference between the two. That way, you can decide which type of feed roller would be best for your operation.
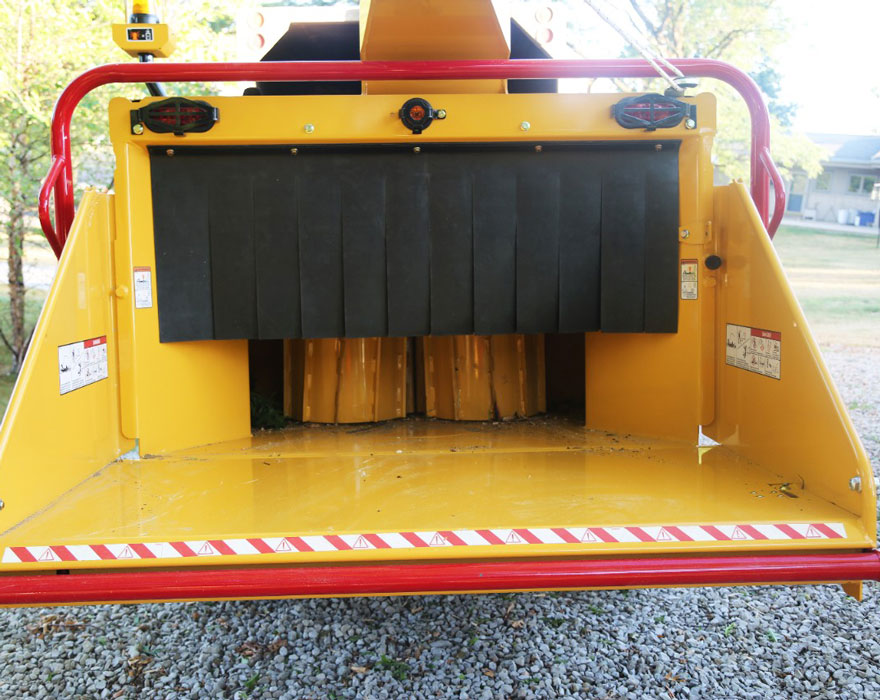
Vertical feed rollers on brush chippers
Vertical feed rollers on a brush chipper are designed for hand-feeding brush and branches into the machine.
With a vertical orientation, the material that’s fed into the brush chipper is not likely to move up and down. Because the feed roller is up and down, there is not a crush feature. The way that the hydraulics work in a vertical feed roller doesn’t allow it to crush.
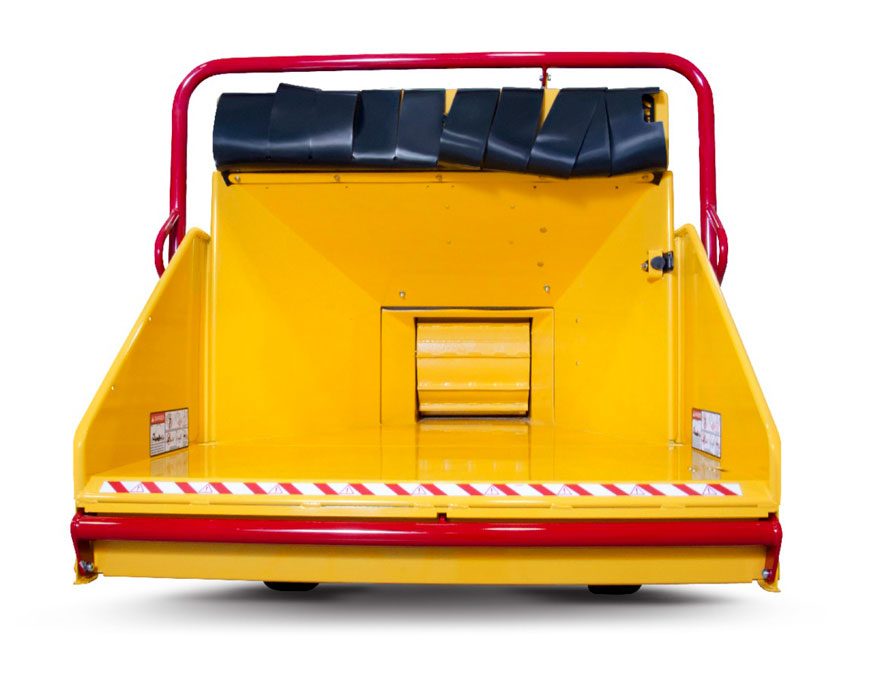
Horizontal feed rollers on brush chippers
Then there’s horizontal feed rollers. These are found on some Vermeer brush chipper models, and some of them come with fixed infeed tables, such as the BC1000XL brush chipper. These are designed for machine feeding, not hand feeding.
“With a horizontal opening, the material is funneled to the feed roller, allowing brush and branches to be placed on the machine at once,” said Cole Chesnut, Vermeer applications specialist.
The feed rollers move the material up and down, instead of side-to-side. Unlike vertical feed rollers, some horizontal ones are equipped with SmartCrush. The feed roller efficiently climbs up and onto material to start the feeding process; then automatically increases down pressure. With material securely gripped by the infeed system, the operator can release the grapple and concentrate on the next load of material.
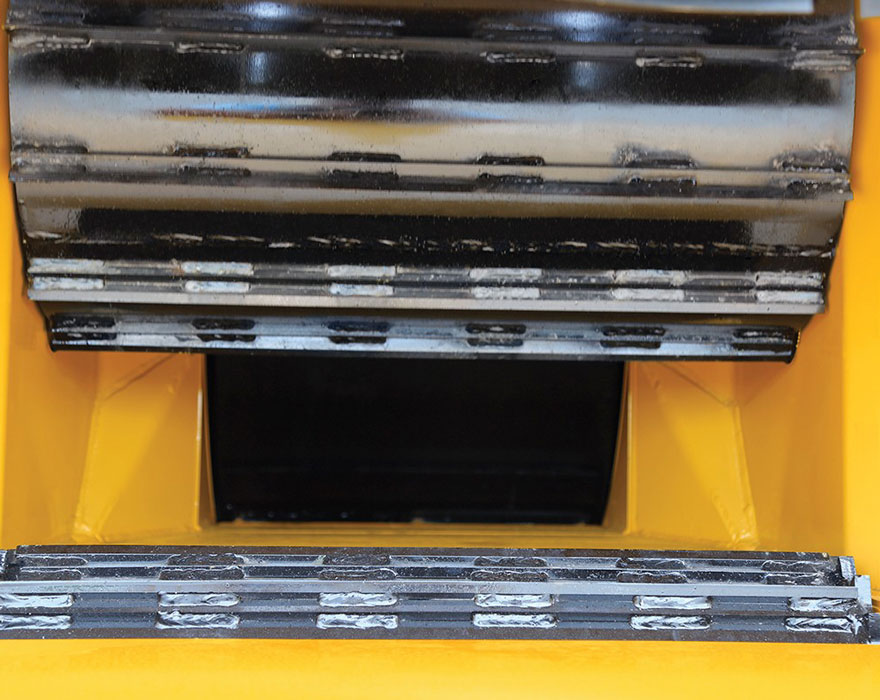
Another option
Beyond the standard vertical and horizontal feed rollers, there are also dual-horizontal feed rollers on the Vermeer AX19, BC2100XL and BC1200XL brush chippers. On these, the offset position of the two horizontal feed rollers allows the bottom roller to introduce the material to the upper feed roller. A two-stage feed roller system allows for standard operation on lighter weight material, while also providing maximum pulling force, up to 12,000 lb (5443.1 kg), on difficult limbs and branches.
“This can reduce the need for your crew to reposition the material while it’s being fed,” explained Chesnut.
Instead, they can trust that the rollers will introduce the material to the drum on its own, without needing any further assistance. “This can keep your crew running efficiently and maximize their productivity on the jobsite,” said Chesnut.
Whether you prefer vertical, horizontal or even dual-horizontal feed rollers, the important thing is that you know the differences and make the right decision for your operation. For more information about feed rollers and Vermeer brush chippers, reach out to your local dealer today.
Vermeer Corporation reserves the right to make changes in engineering, design and specifications; add improvements; or discontinue manufacturing at any time without notice or obligation. Equipment shown is for illustrative purposes only and may display optional accessories or components specific to their global region. Please contact your local Vermeer dealer for more information on machine specifications.
Vermeer and the Vermeer logo are trademarks of Vermeer Manufacturing Company in the U.S. and/or other countries. © 2021 Vermeer Corporation. All Rights Reserved.