Embracing changes help lead to K3 Directional Drilling, Inc.’s success
In the wee hours of the morning, long before the sun comes up and tourists line up to visit “The Happiest Place on Earth(SM)”, the crew of K3 Directional Drilling, Inc., was up working on installing water lines to the water bridge at Walt Disney World® Resort, where ferry boats float over buses.
The Stuart, Florida-based, horizontal directional drilling (HDD) company is responsible for many of the utility upgrades at the Orlando Walt Disney World theme parks. According to K3 Directional Drilling vice president Lewis Krantz, his team executes a lot of water, sewer and electrical installations at Walt Disney World Resort. “We’ve done 2-inch, 4-inch and 6-inch (5-centimeter, 10.2-centimeter and 15.2-centimeter ) electrical installs for roller coaster rides and attractions at the parks,” he explained. “All of the work is done at night — the 3rd shift.”
On this particular project, K3 Directional Drilling is installing two 18-inch (45.7 cm) water mains to run water to the bridge and a 16-inch (40.6 cm) reclaiming line to help circulate the water. Spaced about 10 feet (3 m) apart, each bore is roughly 1,100 feet (335.3 m) long and between 60 to 80 feet (18.3 – 24.4 m) deep through some rock formations.
Choosing the right machine
K3 Directional Drilling’s Vermeer drill fleet includes: D100x140 S3 and D40x55 S3 Navigator® horizontal directional drills; a D60x90 Series II and two D20x40 Series II Navigator® horizontal directional drills and a D9x13 Navigator® horizontal directional drill.
For the water bridge project, K3 Directional Drilling upgraded from an older D100x140 HDD to the latest S3 model. “I bought our older D100x140 HDD used when we first started three years ago, and we put a lot of hours on it — around 1,200 per year, so it was time to retire it,” Krantz said.
Along with a horizontal directional drill, Krantz also added a Vermeer R250C reclaimer to help reduce the volume of drilling fluid that needed to be disposed of. “Finding a dumpsite around Southern Florida is a real challenge,” Krantz stated. “We’re near the Florida Everglades so there aren’t a lot of options, and it can get expensive to dispose of drilling fluids, especially on these large-diameter water and sewer jobs.”
With a backlog of large-diameter work, Krantz felt the timing was right to invest in a reclaimer that could help control his fluid management expenses, and the Walt Disney World project is where he first put the R250C to work.
“At the beginning of the job, we were just demoing the Vermeer R250C along with another recycling system,” Krantz explained. “It was a contractor’s dream scenario – two systems onsite running the same material and using the same drilling fluid pump. After the first day, it was an easy decision for us — the Vermeer R250C reclaimer was more convenient to operate and outperformed the other unit. So, we bought it.”
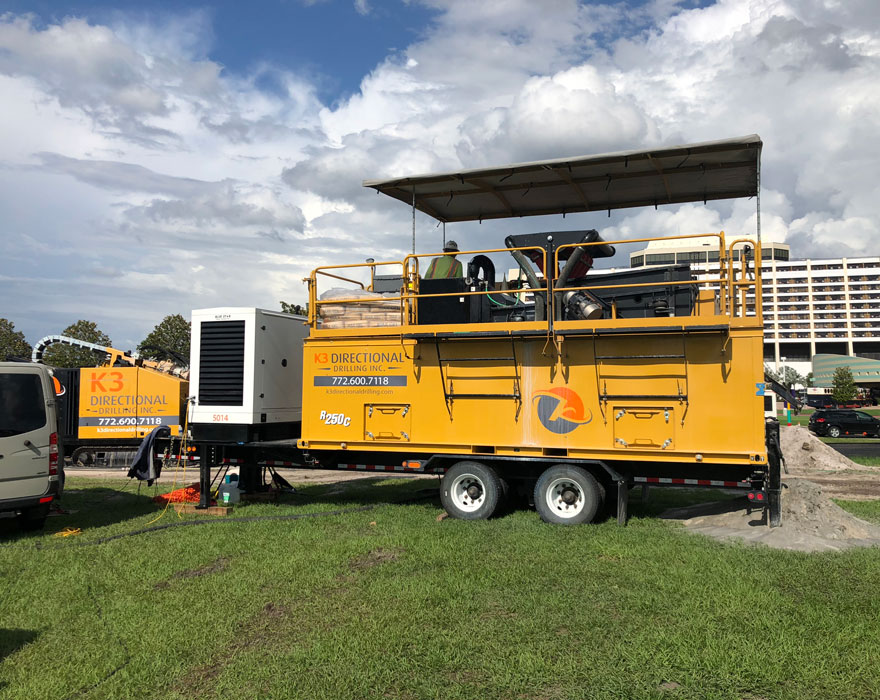
Getting to work
Given all of the obstacles on theme park properties, it can take a little longer to plan and complete a job there. K3 Directional Drilling must first locate old and unmarked utilities running under the parks using ground-penetrating radar (GPR). “Over time, we’ve been able to help document previously undocumented utility lines using GPS and diligent potholing,” Krantz added.
Krantz uses the Vermeer BoreAid® design tool to plan and design large-diameter jobs like this one. He can plug-in information about the soil conditions, product type, the machine they plan to use and other job-related information. Using the inputted data, the program helps Krantz more efficiently plan the job and estimate drilling fluid requirements.
Diligent planning meant the K3 Directional Drilling crew could get right to work on the Walt Disney World Resort water bridge project. The team used a drilling fluid motor with the D100x140 S3 on the pilot bore. “The rock wasn’t very dense, and we were able to navigate through it pretty efficiently, which helped make reaming more efficient,” he explained. “After the pilot bore, we used a Vermeer 16-inch (40.6-centimeter) fluted reamer, then made two additional passes with a 22-inch (55.9-centimeter) and a 26-inch (66-centimeter) reamer, before pulling pipe back. All three of the bores took around four days to complete.”
Help control costs
After completing a few projects using a reclaimer to recycle drilling fluids, Krantz said there are several efficiency benefits of incorporating it into his operations. “On average, we’ve reduced the amount of bentonite we’re purchasing by around 40 percent,” he said. “On a 1,000-foot (304.8 meter), 18-inch (45.7-centimeter) fusible PVC in rock job, we would generally use 10 pallets of bentonite. Now, we only use 5-6 pallets”
“Using a reclaimer is also helping us optimize production,” Krantz added. “The drill operator isn’t waiting for a vac unit to return from a dumpsite, which can sometimes take a couple of hours in this part of the state. No waiting means the operator can increase his reaming time.”
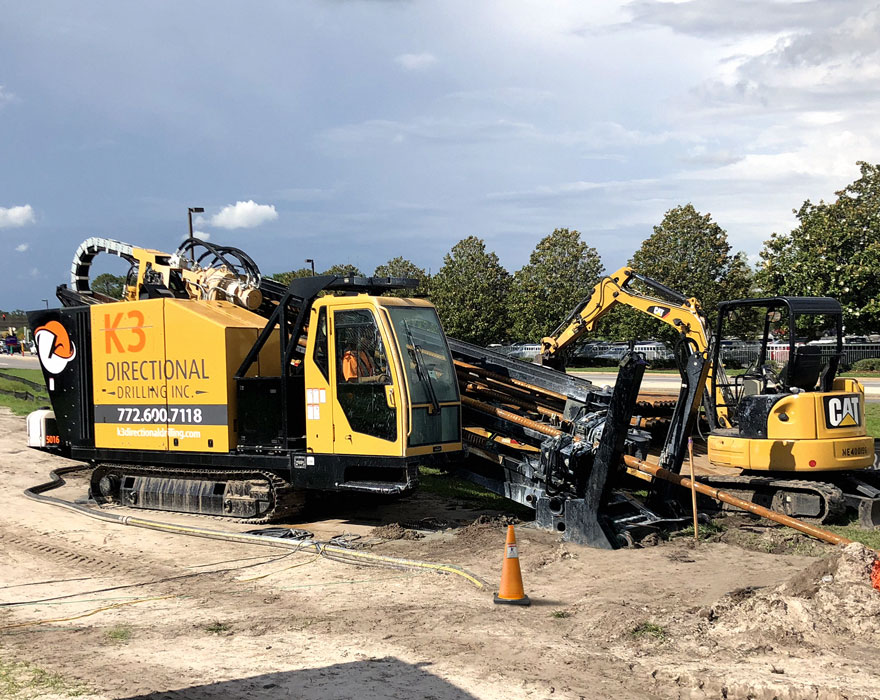
Changing environment for HDD
The limited number of HDD fluid dumpsites in Southern Florida and high disposal fees are not the only reasons why Krantz added the Vermeer R250C reclaimer to his fleet. While bidding on a municipality project, there was a clause mandating the use of a drilling fluid recycling system. It was a first for Krantz, but he also doesn’t expect that it will be the last time he will see a bid like that. “Even though we primarily use only bentonite, runoff is a huge concern in the area,” he explained.
On this same bid, there was also a clause about using a locator equipped with GPS to provide more accurate data for future underground projects. Krantz believes project parameters like these will become more of the norm in the future. Since getting involved in the HDD market in the late 1990s, he’s served as an operator, ran an HDD business with his father and worked at an underground equipment dealership before starting K3 Directional Drilling. During that time, he’s seen machinery evolve and the introduction of several regulations that have impacted HDD contractors.
“There are a lot of job-related tasks that contractors must be able to do today that they didn’t have to worry about two decades ago,” Krantz added. “HDD contractors have to be able to plan and design a bore, navigate underground spaces, provide as-built GPS documentation, as well as have a fluid management plan to help control costs. It’s a lot to stay on top of.”
Staying in front of the competition
Krantz believes one of the reasons that K3 Directional Drilling has been successful is because they embrace innovative technology and are willing to learn. “We’ve been able to outpace HDD companies that have been in business longer than us because we don’t see changes and adversities as obstacles. Instead, we see those things as opportunities. That mindset is a big reason why we’ve managed to grow the way we have.”
Forward-thinking and a commitment to incorporating the latest advancements into their operations is working for K3 Directional Drilling. The company has almost a nine-month backlog of large-diameter work, and Krantz is looking forward to running up the hours on his Vermeer D100x140 S3 HDD and R250C reclaimer to help get it all done.
This article contains third-party observations, advice or experiences that do not necessarily reflect the opinions of Vermeer Corporation, its affiliates or its dealers. Testimonials and/or endorsements by contractors in specific circumstances may not be representative of normal circumstances experienced by all customers.
Vermeer Corporation reserves the right to make changes in product engineering, design and specifications; add improvements; or discontinue manufacturing or distribution at any time without notice or obligation.
Equipment shown is for illustrative purposes only and may display optional or global-region specific features, accessories or components. Please contact your local Vermeer dealer for more information on machine specifications.
Vermeer, the Vermeer logo, Navigator and BoreAid are trademarks of Vermeer Manufacturing Company in the U.S. and/or other countries. Walt Disney World and The Happiest Place on Earth are trademarks of Disney Enterprises, Inc.
© 2018 Vermeer Corporation. All Rights Reserved.