Large-diameter horizontal directional drilling (HDD) work in urban areas is on the rise as cities expand and upgrade their utility services, as well as move more electrical transmission lines underground. When space is tight or using pumps is not an option for moving mud, reclaimers and vacuum excavators are the perfect combination to complement larger HDDs.
Managing the mud on large-diameter HDD projects varies from project to project because no two jobsites are the same. In rural areas where there is plenty of room to operate, contractors have many options for setting up mud recycling systems and transporting it back to the drill. But when space gets tight on projects located near busy highways or in the city, and space is a premium, contractors need to be more creative with their mud management plan. In these scenarios, mud management engineers now recommend pairing up large truck vacuum excavators and reclaimers to keep fresh drilling fluids supplied to large HDDs.
“Vacuum excavators and mud recycling systems/reclaimers have been widely used for years by HDD contractors, but rarely in the combination they are being used today,” said Adam Bates, product manager for Vermeer. “Traditionally, vacs only served the role of hauling away used mud when the weight increased to a point where it no longer could be efficiently recycled by the reclaimer. Pumps, hoses and piping were used to move slurry and clean drilling fluids back and forth between the reclaimer and the drill. With more water, sewer, electrical and gas lines being upgraded via trenchless installation methods, large-diameter work in congested areas requires crews to employ vac trucks more frequently to transport drill slurry to the reclaimer.”
John Cope, applications engineer at Vermeer, echoed Bates’ observations about the increased pairing of vacs and reclaimers. “In most situations, it’s more cost effective to use pumps and temporary piping to transport drilling fluid back and forth between the pits, reclaimer and drill. When that’s not logistically possible, contractors and fluid management engineers need to consider which options are available to them.”
Controlling the flow
On bores where running drilling fluid hosing above ground is not an option because of existing obstacles, crews can reduce the volume of returns they have on the exit side through grade control and delaying punch out. “Depending on the ground conditions, some crews will avoid punching out on the pilot bore and use push ream as long as possible before pushing through on the exit side,” said Cope. “This practice will push returns back to the entry pit through most of the project so they can minimize the amount of fluid handling they have to perform. However, this approach isn’t advisable for many soil types because it could produce inadvertent returns.”
When space is limited on the drill side, the bore crews can try to minimize entry pit returns through grade control, depending on the contour of the land. “The effectiveness of controlling the flow of returns through grade control can vary greatly, but it can help reduce hauling fluid back and forth from both ends of the bore,” Cope said. “Often, crews will still have to suction slurry from the entrance pit and haul it to the reclaimer, but not as frequently as when the grade has not been controlled.”
When running pumps and hosing is not an option, both options can help reduce the volume of fluid being transported daily. However, on some projects in urban areas, crews may not have enough space for the reclaimer — or may be limited by other project restrictions.
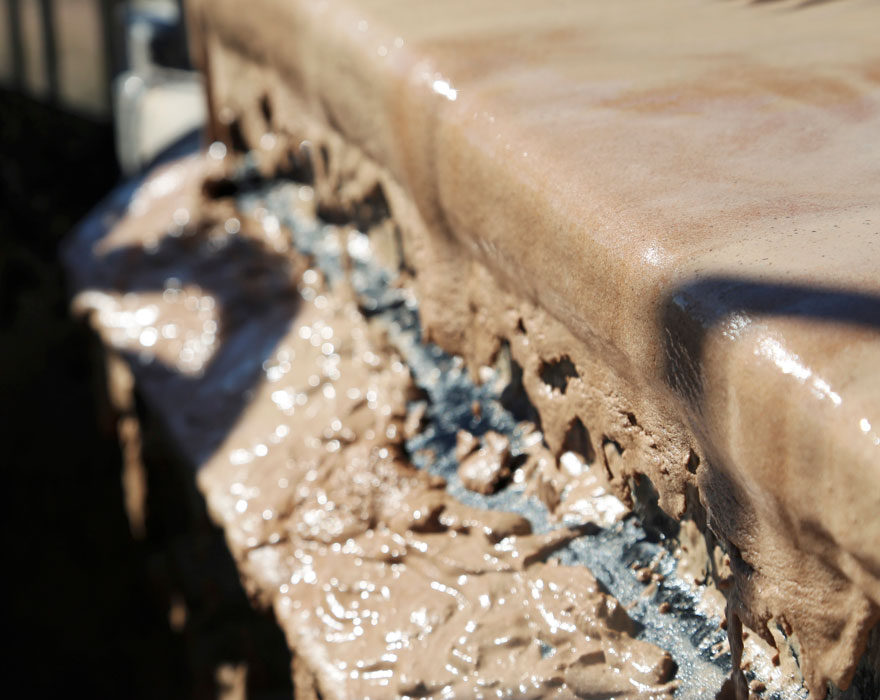
Mud management site
While not an ideal situation, space restrictions, or the need to move equipment frequently, may require drilling crews to establish an entirely separate mud management site on bores that require large volumes of fluid. According to Bates, this setup involves using vacs to collect the drill slurry from the entry and exit pits and transporting it to a nearby mud management site. There, it is recycled then hauled back to the drill. “Since there are more moving pieces involved, there certainly are added costs associated with this arrangement, but in many scenarios, it is still a more cost-effective option than not recycling drill fluids. Disposing of all the used slurry would require the use of vacuum excavators — likely more depending on the distance to the disposal cost — and there would be substantially more invested in additives and freshwater.”
Bates added that it is important for HDD contractors to secure a site that is as close as possible to where the bore is being performed and where there is minimal traffic interference. “Shorter round trips can reduce the number of vacs needed to support drilling operations and help keep the drill operation productive,” said Bates. “Also, when dealing with the amount of fluid involved with larger bores, truck vacs are more efficient than trailer-mounted units. But trucks may not be as easy to maneuver in and out of tight traffic, so that needs to be factored in when choosing where to establish a mud management site.”
Managing cycle times
For pipeline HDD work in rural areas, subcontracting out the vacuum excavation work is a common practice. In many instances, local or regional vac service companies are already working with other contracting crews on pipeline construction and can be shared resources.
Although it makes sense in rural areas, subbing out vac services may not be an efficient or cost-effective solution on bores in urban areas. “When trucks are involved with the mud recycling process, communications and timing are essential so the drill is never waiting on mud,” said Bates. “Trying to coordinate schedules with another company is often an extra step that can have a real impact on overall operations. This is why many contractors who do a lot of work in urban areas invest in their own vac and water trucks, which gives them the ability to control their time and costs on projects better. This is especially important for jobs that demand mud recycling efficiency.”
Managing drilling fluids on any large-diameter HDD project in urban areas is no easy task. However, by thoroughly exploring all the fluid transportation options available and employing the right equipment, contractors can develop an efficient fluid management plan no matter what challenges a jobsite may present.
For more information about Vermeer reclaimers and vacuum excavators, contact your local Vermeer dealer or visit vermeer.com.
Vermeer Corporation reserves the right to make changes in product engineering, design and specifications; add improvements; or discontinue manufacturing or distribution at any time without notice or obligation. Equipment shown is for illustrative purposes only and may display optional accessories or components specific to their global region. Please contact your local Vermeer dealer for more information on machine specifications. Vermeer, the Vermeer logo and Navigator are trademarks of Vermeer Manufacturing Company in the U.S. and/or other countries.