Over the last decade, reclaimers (recyclers, mud recycling systems) have become a staple for mid-sized to large-diameter horizontal directional drilling (HDD) installation work. Traditionally, pairing drills and reclaimers happened on heavy pipeline projects involving maxi rigs, but in recent years, this combination has become more common on bores involving mid-sized drills.
According to John Cope, application engineer at Vermeer, a general rule of thumb that many HDD contractors apply today is that if bores require more than 8,000 gallons (30,283.3 L) of drilling fluids per day, recycling used drilling slurry may be a better choice than pumping and dumping it. “There are a lot of factors that weigh into when and where to employ a reclaimer, but the expense of drilling fluid additives and water, plus transporting and dumping used slurry, has certainly resulted in more widespread usage of this option in rural and urban areas.”
Sizing
As reclaimers have made their way into the mid-sized HDD market, so has the number of models available for contractors to choose from. To determine which size to use, Cope said contractors need to consider the maximum rate they will be pumping fluid down the drill string. Knowing that, they then will be able to pick out a reclaimer that can keep up with the particular HDD model they are using. For example, a Vermeer D100x140 S3 Navigator® horizontal directional drill has an onboard pump with a maximum flow of 230 gallons per minute (870.6 L/min), so the Vermeer R250C reclaimer, which can clean up to 250 gallons per minute (946.4 L/min) of fluid, would be the best match.
For projects that require higher fluid volume, Vermeer recently introduced the R600T reclaimer, which is capable of cleaning up to 600 gallons per minute (2,271.2 L/min) of used drilling fluid per minute. “This model is designed to keep pace with maxi rigs using high-pressure mud pumps like the Vermeer SA400 high pressure mud pump, which can pump up to 550 gallons per minute (2,082 L/min),” explained Cope. “These two Vermeer reclaimer models do a good job of covering the needs of most mid-sized and maxi rig drills.”
On massive projects that exceed the capacities of the R600T, running a pair of reclaimers is becoming common practice for contractors. “A significant amount of thought is put into how used drilling slurry gets moved around on long boring projects,” explained Cope. “One way or another, slurry or clean drilling fluids need to be transported back to the drill from the exit side. So, when higher volumes of fluid need to be cleaned, contractors will place a reclaimer on the bore’s exit side with larger screen sizes to quickly clean material on that side of the bore. Then, they will pump it back to the entry side, where it will be recycled again with slurry from the entry pit for a deeper cleaning. The fluid coming for the exit side helps dilute the slurry on the entry, which helps maximize the drill side reclaimer’s cleaning efficiency.”
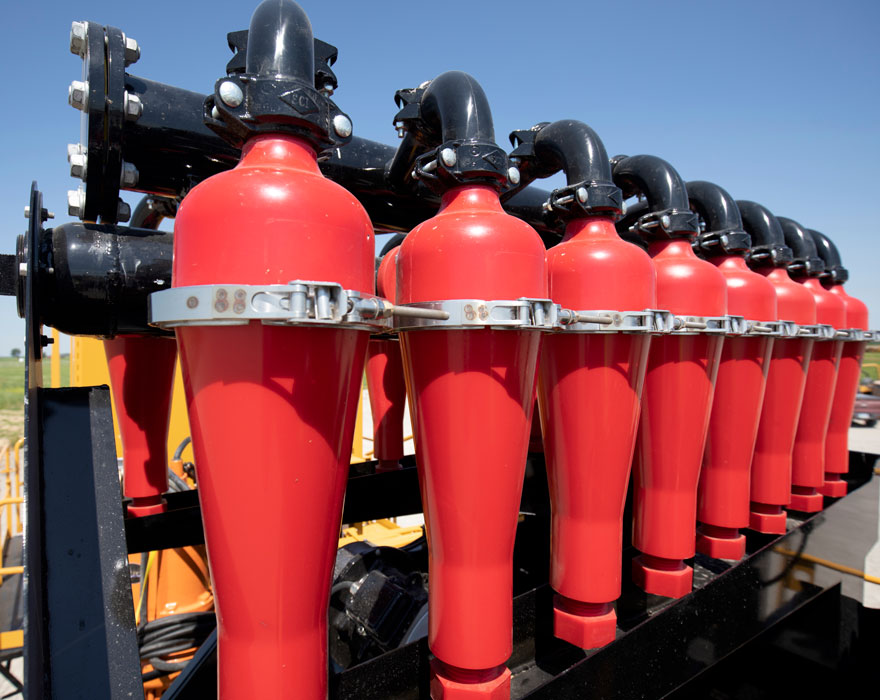
Placement
Since no two jobsites are the same, contractors need to be flexible about the right drill and reclaimer setup that will best suit their jobsite conditions. Cope said the number one consideration when it comes to determining the correct configuration for a job is the available space. “In rural areas where there is plenty of space, crews can arrange their equipment however they want,” he explained. “However, in urban areas, sites are often much tighter — sometimes there isn’t room for a reclaimer on the drill side, so it needs to be positioned on the exit side. The entrance pit’s slurry would then need to be transported to the other side of the job before being pumped or hauled back to the drill. Other times, there may not be any room for the reclaimer on either side, so a separate site would need to be established and all of the drilling fluids would have to be transported back and forth to the job.”
After determining the jobsite conditions, the next step contractors should look at is where their nearest available water source is, as well as review what equipment they have available to them. “Whether it’s moving water or drilling fluid, there can get to be a lot of equipment involved with transportation,” said Cope. “Pumping fluid instead of trucking it is almost always more efficient. So, if the closest water source is located on one side or the other, and the drilling fluid will either need to be dumped or diluted frequently, it probably makes sense to position the reclaimer on that side of the site.”
Cope went on to say that if crews can have some control over the direction of their returns, they can further reduce the transportation of drilling fluid. “A growing number of contractors have started to avoid punching out on the pilot bore and using push-reaming methods to send the bulk of their returns to the entry side where the reclaimer sits,” Cope explained. “This method isn’t always possible, especially if higher downhole pressure is required or the ground conditions don’t support it, but when possible, it can certainly help minimize the movement of slurry.”
When there is no compelling reason to choose the drill side or the exit side for placing the reclaimer, Cope recommended that contractors consider pump and piping requirements. “It is a lot easier to pump clean drilling fluid back to the drill than heavy slurry,” he said. “So, a contractor may be able to get by with using a smaller pump and smaller-diameter pipe to move the clean fluid back to the drill if the reclaimer is placed on the exit side. However, they will likely have to have a holding tank on the drill side for temporary storage.”
Flexibility
With so many variables and factors to consider for recycling used drilling fluid, Cope recommended that contractors evaluate every project’s conditions ahead of time and then develop a mud management plan to address the job’s particular needs. “As with any work, people tend to employ certain methods and setups because it’s the way they’ve always done it. So, if a crew has always positioned their reclaimer in the same place on every job, they may end up spending a substantial amount of resources trying to create that same arrangement on the next project, when it may be much quicker and more effective to move the reclaimer. Those types of details can have a real impact on production rates, which is why being flexible with their equipment arrangement is so important.”
For help selecting the right reclaimer for your needs, or if you have questions about the best way to manage mud on your next HDD project, contact your local Vermeer dealer. For more information about Vermeer HDDs, reclaimers and mud pumps, visit vermeer.com.
Vermeer Corporation reserves the right to make changes in product engineering, design and specifications; add improvements; or discontinue manufacturing or distribution at any time without notice or obligation. Equipment shown is for illustrative purposes only and may display optional accessories or components specific to their global region. Please contact your local Vermeer dealer for more information on machine specifications. Vermeer, the Vermeer logo and Navigator are trademarks of Vermeer Manufacturing Company in the U.S. and/or other countries.