It is an exciting time to be working in horizontal directional drilling (HDD). Work is plentiful, and contractors are installing large-diameter product at incredible distances and in challenging ground conditions thanks to advances made to machinery, new technology and tooling, and skilled crews.
Projects thought to be impossible a few short years ago are now just another day for many crews. While it’s easy to praise the drill operator and the machine putting rods in the ground, these new levels of success wouldn’t be possible without the fluid pumping through the drill stem and individuals managing the mud that’s flowing.
Drilling fluid is an essential ingredient to HDD success, and on large-diameter, long-distance projects, or ones with rocky conditions, crews will use a lot of it. The volume of drilling fluid required and the rising costs associated with fluid management has led to the widespread use of reclaimers/mud recycling systems on many jobsites. The trend first started with the pairing of large maxi rigs, and now reclaimer usage is working its way down to larger utility drills because of the fluid demands required when drilling in rock.
According to John Cope, applications engineer at Vermeer, contractors consider many factors when determining when to employ a reclaimer on a jobsite. “The old rule of thumb used to be that if a crew is using more than 8,000 gallons (30,283.3 L) of fluid a day, adding a reclaimer could offset the labor and costs associated with fluid disposal. However, when dump fees are high or there isn’t a disposal site nearby, using a reclaimer on projects where less fluid is needed may still make sense,” he explained.
HDD contractors across Canada are using reclaimers almost every day all year long to reduce fluid disposal costs and because many projects require it. Justin Babcock, Western Canada service manager with Vermeer Canada, said that on large-diameter projects, many engineers are setting parameters around how much fluid can be used on shots. “Operating reclaimers is a big part of how contractors are adhering to these limitations,” he explained. “Of course, depending on the time of year and ground conditions, crews are challenged to keep fluid flowing through their recycling systems — especially with how cold it gets in some parts of the country.”
Operating habits
Cope and Marv Klein, Vermeer applications specialist – pipeline segment, tell contractors that daily operating habits are essential to getting the most from mud recycling systems. Cope said step one is changing the mindset of the drill operators. “HDD operators sometimes try to get by with using a minimum amount of fluid in an attempt to make what they have last longer and reduce the number of disposal trips,” he explained. “This mindset could reduce productivity. A properly paired reclaimer should be able to keep up with the needs of the drill and allow HDD operators to turn up the flow.”
For the crew members overseeing the mud recycling process, Klein said it is essential to maintain an adequate amount of fluid and perform viscosity, sand content and mud weight tests regularly. “Not all of the fluid pumped through the drill string will return back out of the bore path due to filtration into the formation. The fluid that does return now has native soil, rock and sand particles (solids) mixed with it,” he said. “The reclaimer’s job is to separate these solids; however, it needs to have the correct ratio of fluids to solids in order to separate properly. Too thick of mud can lead to inadvertent returns and reduce the overall efficiency of a reclaimer.”
Cope added that elevated pump pressure is a good indicator that mud weights have increased. “When pump pressures increase, the operator should be checking the mud weight to determine if the mud weight needs to be adjusted.”
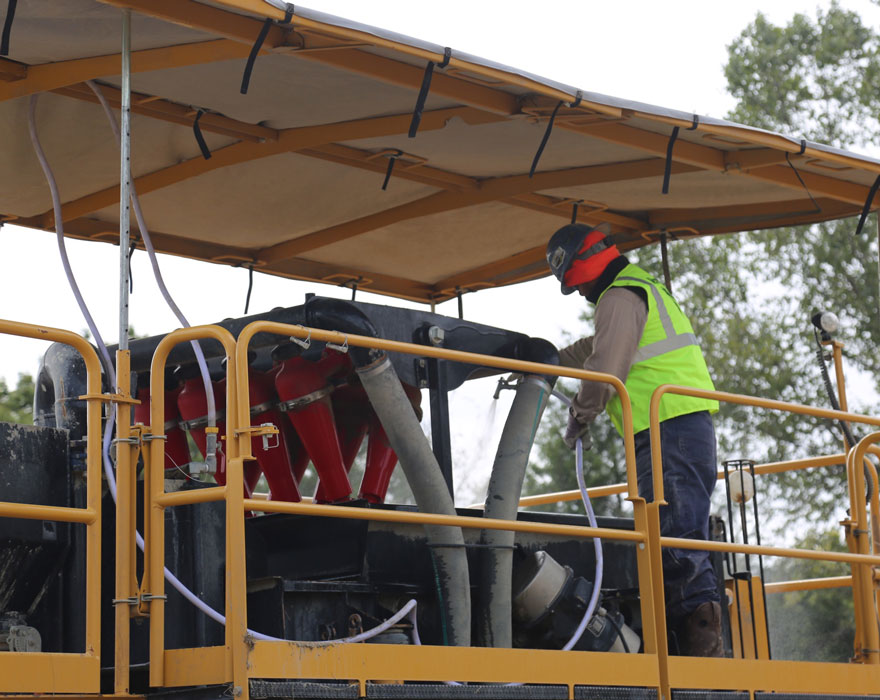
Regular care
Moving from operational guidance to routine maintenance, reclaimer operators need to keep a careful eye on the condition of their screens and cones to allow them to do their job correctly. While a change in pressure may be a reflection on mud weight, it could also be caused by an issue with a recycling system’s screens or cones. “Holes or tears in a screen will allow larger particle sizes through which can lead to higher sand content levels,” said Cope. “Plugged or worn cones can also lead to higher levels of solids into the clean drilling fluid.”
According to Klein, a quick visual inspection of the screens at the start of the day and a continuous rinsing of the screens during operation will help optimize performance. In addition, a thorough washing at the end of a shift to prevent solids from caking will help improve screen performance and screen life. He also recommends operators to regularly check the condition of the cones, especially when working in sandy or rocky grounds. “Hydrocyclones are preset at a specific diameter from the manufacturer for optimum performance,” he said. Over time, sand can cause internal wear of the cone walls affecting the cone’s performance. A change in the underflow spray pattern or increase in sand content levels could be an indicator that excessive wear has occurred.”
Inspecting cones can be an efficient process. Operators can remove the apex bushing at the bottom of each cone and feel the inside walls on the cones. It should be fairly smooth and not course/rough. If not, it is likely time to replace the cone.
Higher sand content levels can also wear down the impellers on a mud recycling system’s centrifugal pumps. Cope and Klein said the most likely tell of a worn-out impeller is a pressure drop at the hydrocyclone manifold.
In addition, to check the condition of screens, cones and impellers regularly, operators should also follow the maintenance recommendations found in their machine’s operator manual. Greasing and other preventative maintenance needs are outlined there.
Cold weather care
Just as with a horizontal directional drill, extra steps need to be taken to maintain reclaimers when temperatures drop below freezing. According to Babcock, keeping the flow starts with making sure the pit or trash pump is completely submerged for continuous circulation. “It can be a real chore to keep fluid in the tanks of the system from freezing, but all of that work doesn’t matter if the used slurry freezes and can’t be reclaimed,” he explained. “In extreme weather conditions, many contractors will keep an operator on the job around the clock to keep everything a liquid with continuous circulation. Other operations will add heater and tarp areas and close off some pump compartments.”
In the fall and spring, when temperatures may dip below freezing in the evening through the early morning hours, Babcock tells contractors to drain their tanks and circulate an environmentally friendly antifreeze through the pump, just like they would with their drill. “Allowing water to freeze inside a pump can result in damage and will certainly impact productivity,” he explained. “In addition to circulating antifreeze, the crew should also flush screens and make sure the cones are draining correctly. Frozen clumps of material will also impact the system and how it separates the liquids from the solids.”
Prepping for storage
Before shutting a reclaimer down for the season or an extended period, crews should also take the time to drain the tanks, flush the lines and wash everything.
Vermeer Corporation reserves the right to make changes in engineering, design and specifications; add improvements; or discontinue manufacturing or distribution at any time without notice or obligation. Equipment shown is for illustrative purposes only and may display optional accessories or components specific to their global region. Please contact your local Vermeer dealer for more information on machine specifications.
Vermeer and the Vermeer logo are trademarks of Vermeer Manufacturing Company in the U.S. and/or other countries.