Social distancing, e-learning and work from home (WFH) are a part of the common phrases being used by everyone since the middle of March 2020. While this new “normal” sure doesn’t feel normal, everyone is adjusting to life during the COVID-19 pandemic. One thing that is keeping people connected and productive is the high-speed fiber connectivity in both large cities and rural areas.
The team at High Speed Crow, based in Lockport, Manitoba, is a trusted name in providing high-quality fiber and wireless internet services for much of rural Manitoba. Company President Bryan King said it has been his mission to deliver the same levels of internet access to his rural neighbors as people living in the city. “From businesses in smaller communities competing with large companies to giving our young people access to the same educational tools that city kids have, high-speed internet access isn’t a luxury — it’s a necessity no matter where a person lives,” he explained. “Our job at High Speed Crow is to deliver access to over 7,000 square miles (18,130 km2) of rural Manitoba using fiber and wireless broadband.”
High Speed Crow beginnings
King started High Speed Crow in 2003, after growing up in rural Canada and spending the early part of his career working and living in several technology hubs throughout North America. When he decided he wanted to move closer to family and friends, frustration over the lack of having a stable internet connection led him to build his own network. “I was working on projects for companies from South America to China, and I needed a reliable internet connection,” said King. “When I wasn’t able to get a good connection, I found myself asking, ‘Why can’t I get internet as crows fly?’ From that day forward, I’ve made it my mission to answer that question for myself, as well as everyone living in the area.”
In High Speed Crow’s early years, the company only delivered wireless service. However, in 2015, King decided to expand the company’s services as the demand for higher internet bandwidths grew, and wireless service would no longer be enough in more densely populated areas. After exploring his options for installing fiber in the area, King concluded it was in his customers’ best interests to perform the work themselves.
“Oil prices were at a record high, and utility contractors had plenty of work to do,” King explained. “I didn’t want our customers to have to wait on the schedule of other busy contractors for the fiber build-out to begin, and since I grew up with a farm background, along with several other people that work at the company, heavy machinery and hard work didn’t scare us. We staffed up and purchased a small Vermeer LM42 vibratory plow and got to work.”
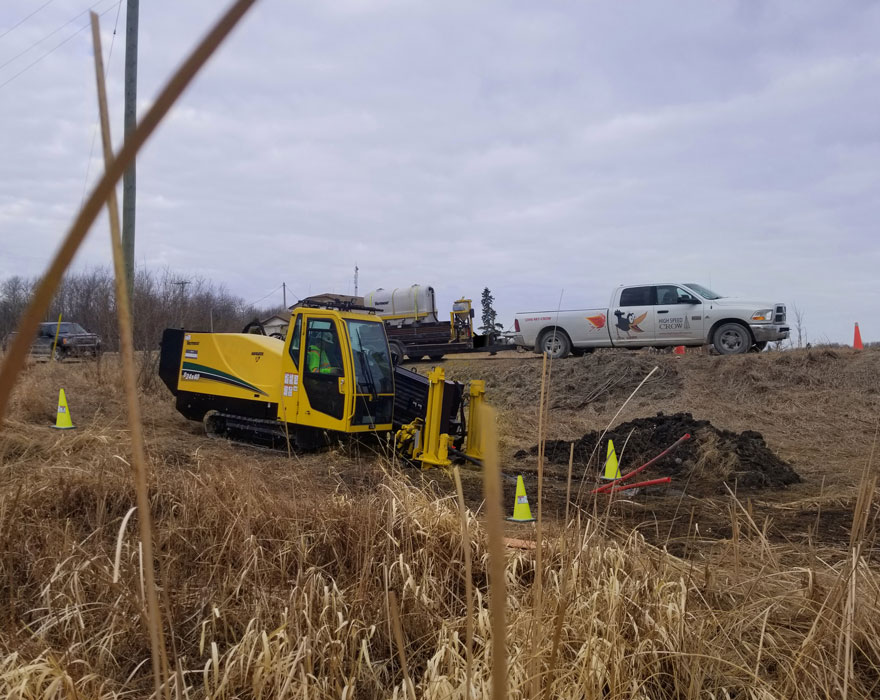
Expanding operations
It didn’t take long for High Speed Crow’s workload to outgrow what they could do with a single vibratory plow. Within a few months, the team added a Vermeer RTX1250 ride-on tractor, a Vermeer V500 vacuum excavator and a Vermeer D9x13 S3 Navigator® horizontal directional drill. The big vibratory plow is used to install the system’s backbone, the small plow is used for short drop and the D9x13 is used in more sensitive ground conditions, hooking businesses as well as homes. The vacuum excavator is also an essential part of the process to help them avoid existing buried infrastructure and support their drilling crew.
To further speed up the process of building out High Speed Crow’s fiber network, the company also added a Vermeer D20x22 S3 Navigator® horizontal directional drill and then added a D24x40 S3 Navigator® horizontal directional drill. “These two drills give us the ability to do longer shots and work in more challenging and rocky ground conditions,” stated King. “Another handy machine we added to our fleet is the Vermeer SPX25 vibratory plow. It’s a small, remotely operated unit that gives us the ability to plow in fiber in tight working quarters. It’s quick, easy to use and requires very little restoration work after a drop is done.”
From the start of High Speed Crow’s expansion into fiber, the company has relied on Vermeer Canada for its utility equipment needs. “I picked Vermeer machinery because we needed dependable equipment that would maximize our working time every summer,” King said. “Vermeer has always had a great reputation, and I have always heard from utility contractors working in the area that Vermeer Canada is a reliable partner. We’ve certainly had a wonderful working experience with our dealer and Vermeer over the years.”
Ongoing operations
The bulk of fiber installation work for High Speed Crow happens during the summer months, which means crews need to be ready to roll each spring when the weather gets nice. On average, crews install 150,000 feet to 180,000 feet (46,720 m to 54,864 m) of fiber each year, one town at a time. The amount of work done ranges because the soil conditions in the area can be a bit unpredictable. Most of the time, crews work in softer soils, but every now and again, there are some patches of hard rock.
“This past summer, we had a particularly challenging 2-mile (3.2-km) stretch of bad rock that we brought in an excavator with a breaker to work our way through,” King said. “In hindsight, we should have swapped out the vibratory plow on the Vermeer RTX1250 with a rock saw attachment. I think that would have been more efficient. We’re always learning on the job and identifying ways we can get better. It’s what makes it fun for our crews and helps us improve.”
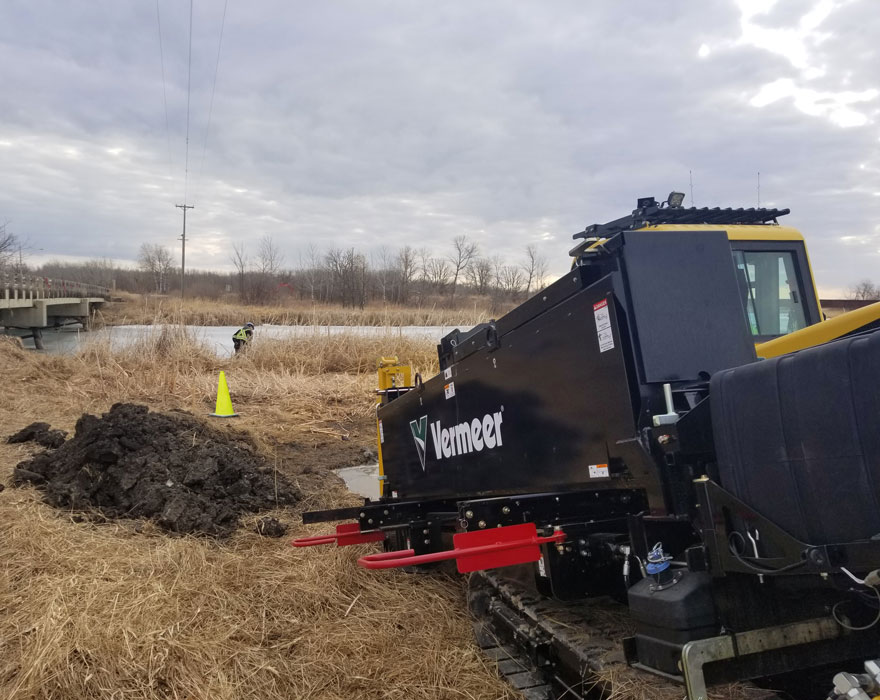
Focus on safety
King pushes his team to do the best job they can for the customers they serve. “We aren’t just providing services to communities,” he explained. “Our customers are also our neighbors. So, if we leave a mess or don’t do right by them, we hear about it on the street, the grocery store, at church or wherever we’re at. It’s that level of connections that makes all of this so rewarding.”
Doing right by the team members working for High Speed Crow is also something important to King. “From day one, we instilled the importance of safety with everything we do,” he said. “We cross-train our crews so everyone knows the process required out of everyone on a team. Also, we hold morning tailboard meetings to review what’s on the schedule for the day and discuss any safety-related steps that need to be taken on a particular project. Ongoing open communications help keep everyone informed and doing their job safely and efficiently.”
The company’s commitment to safety was recently recognized when the team received the 2019 Manitoba North America Occupational Safety and Health (NAOSH) Award for its efforts in creating a healthy and safe work environment.
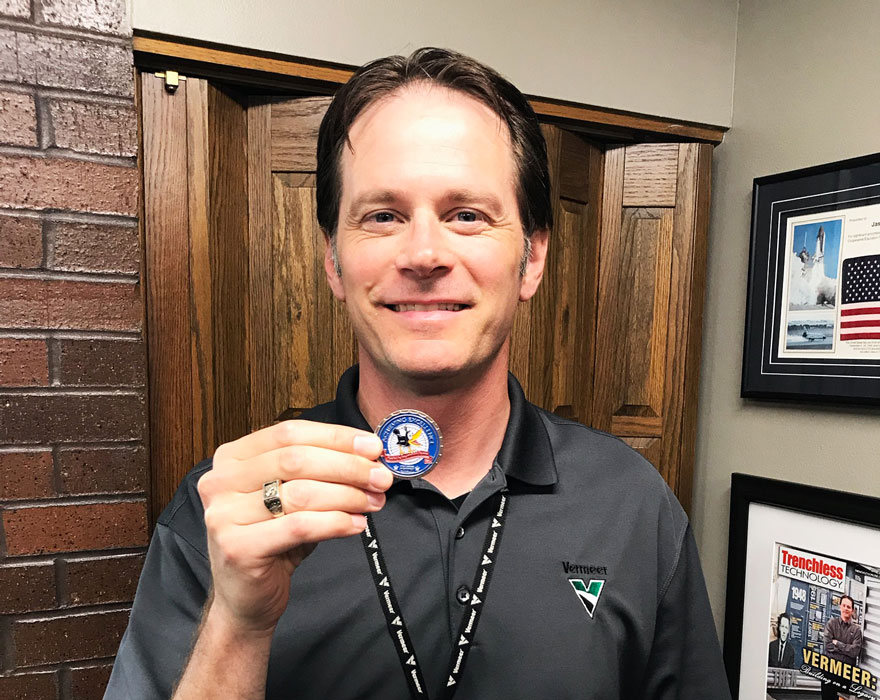
Challenge coin
Through the past 17 years of operating High Speed Crow, King has created a culture of innovation by challenging his team and himself. When an individual on his team goes above and beyond, King awards them with a “challenge coin.” The idea for the coin started after a conversation with a friend who was doing something similar in his business, King explained. “We came up with criteria for what we believed warranted receiving the coin and designed our own coin. We have a crow on one side and a digging Dutchman (similar to an older version of the Vermeer logo) on the other side. It’s an honor inside our organization to receive a coin and helps reinforce the kind of culture we’re trying to create.”
During a trip to Pella, Iowa, to visit the Vermeer manufacturing facilities, King had the chance to award Jason Andringa, president and CEO of Vermeer, with a High Speed Crow challenge coin. “I gave Jason a coin as a way of thanking everyone at Vermeer for continuing to innovate and improve on their equipment designs. They’ve been a great partner for us, and we appreciate what they do.”
Busy times ahead
The team at High Speed Crow moves forward every working season, trying to outdo what they accomplished the year before. King doesn’t believe they will ever be done with expanding their fiber network in the metro Winnipeg region. “As demand for high-speed internet grows, so will our responsibilities to our customers,” he said. “We’ve been here delivering on our promise during today’s uncertainties, and we’ll be there for them when life gets back to normal.”
This article contains third-party observations, advice or experiences that do not necessarily reflect the opinions of Vermeer Corporation, its affiliates or its dealers. Testimonials and/or endorsements by contractors in specific circumstances may not be representative of normal circumstances experienced by all customers.
Vermeer Corporation reserves the right to make changes in product engineering, design and specifications; add improvements; or discontinue manufacturing or distribution at any time without notice or obligation. Equipment shown is for illustrative purposes only and may display optional accessories or components specific to their global region. Please contact your local Vermeer dealer for more information on machine specifications. Vermeer, the Vermeer logo and Navigator are trademarks of Vermeer Manufacturing Company in the U.S. and/or other countries.