The rising costs associated with fluid management and volume of drilling fluid required on horizontal directional drilling (HDD) projects has led to the widespread use of reclaimers and mud recycling systems on many jobsites. To get the most from these powerful machines, Vermeer Application Engineer John Cope and Vermeer Application Specialist Marv Klein offer up these operating and routine maintenance tips.
Operational advice
- Let the fluid flow — A common mistake crews make is trying to get by with the least amount of drilling fluid to do the job. However, reclaimers can be more efficient when more fluid is being circulated because it helps keep the liquid-to-solids ratio lower.
- Perform regular viscosity, sand content and mud weight tests — Not all of the fluid pumped through the drill string will return back out of the bore path due to filtration into the formation. The fluid that does return now has native soil, rock and sand particles (solids) mixed with it. To separate the solids, the reclaimer needs to have the correct liquid-to-solids ratio to do its job properly. If the mud is too thick, it can lead to inadvertent returns and reduce the overall efficiency of the reclaimer.
- Watch your pump pressures — Elevated pressure is a good indication that mud weights have increased. When that happens, the operator should check the mud weight to determine if adjustments need to be made. Also, a low inlet pressure reading at the manifold can be a result of aeration or a wear to the impeller on the mud recycling system’s centrifugal pump, which means it’s time to replace it. The pressure of the manifold should be checked at startup, with water.
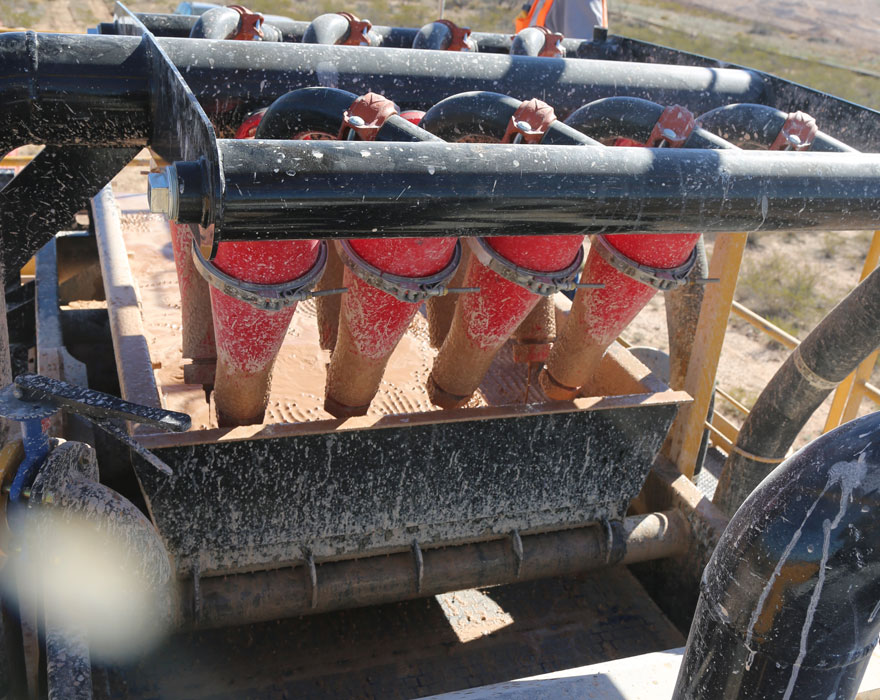
Ongoing maintenance guidance
- Keep an eye on the screens and cones — A change in sand content can be an indication of an issue with the recycling system’s screens or cones. Holes or tears in a screen will allow larger particle sizes through, which can lead to higher sand content levels. Plugged or worn cones can also lead to higher levels of solids into the clean drilling fluid.
- Rinse screens regularly — During operating hours, continuous screen rinsing can help optimize performance.
- Thoroughly wash screens at the end of a shift — Caring for the screens before shutting down for the day can help prevent solids from caking, improve screen performance and help make screens last longer.
- Inspect the cones — A change in the underflow spray pattern or increase in sand content levels could be an indicator that excessive cone wear has occurred. To inspect each cone, remove the apex bushing at the bottom of the cone and feel the inside walls on the cones. It should be a smooth conical wall and not coarse, rough or grooved. If not, it is likely time to replace it.
- Follow machine’s operator manual — Greasing and other preventative maintenance needs are outlined there.
Cold weather care
- Plan for fall and spring temperature dips — To help prevent fluids from freezing from one day to the next, tanks should be drained, and environmentally-friendly antifreeze should be circulated through the pump.
- Care for screens and cones — To help keep screens and cones operating correctly in cold weather, flush screens at the end of the day and make sure the cones drain correctly. Frozen clumps of material can impact the system and how it separates the liquids from the solids.
- Prevent tank fluid from freezing up during operations — Make sure the pit or trash pump is completely submerged so there is continuous circulation.
- Adjust for extreme weather conditions — Many contractors will keep an operator on the job around the clock to keep everything in liquid form with continuous circulation. Other operations will add heater and tarp areas and close off some pump compartments.
- Prep for storage — Before shutting a reclaimer down for the season or an extended period, crews should also take the time to drain the tanks and pumps, flush the lines, wash everything and add environmentally-friendly anti-freeze into pumps casings, which helps with corrosion.
Be sure to share these tips with everyone on your crew and reach out to your local Vermeer dealer with any questions. Also, if you want to learn more about Vermeer reclaimers, visit vermeer.com/reclaimers.
Refer to your operator’s and/or maintenance manual for further instructions and safety information. Vermeer Corporation reserves the right to make changes in product engineering, design and specifications; add improvements; or discontinue manufacturing or distribution at any time without notice or obligation. Equipment shown is for illustrative purposes only and may display optional accessories or components specific to their global region. Please contact your local Vermeer dealer for more information on machine specifications. Vermeer and the Vermeer logo are trademarks of Vermeer Manufacturing Company in the U.S. and/or other countries. © 2020 Vermeer Corporation. All Rights Reserved.