Hard Rock Directional Drilling completes 30-inch pipeline bore spanning nearly 15,000 feet underwater
At the moment when project supervisors with NuStar Energy LP finished sharing details of the Nueces Bay underground pipeline project with Tom Forconi, division manager at Hard Rock Directional Drilling, Forconi was already envisioning how his team of horizontal directional drilling (HDD) experts would approach the job. Even if the assignment were to take place all on land, he knew the sheer length — 15,000 feet (4,572 m) — would require two bores intersecting at a point near the middle. But this job, positioned beneath the ecologically sensitive Nueces Bay and within proximity to the famed Corpus Christi, Texas, shoreline, presented additional challenges.
NuStar Energy, based in San Antonio, Texas, tapped Hard Rock Directional Drilling to tackle the project as an extension of one of three of the company’s South Texas Pipeline Systems designed to move increased volumes of West Texas Intermediate (WTI) crude from the Mid-Continent Oil Field Province, located in the West Texas Permian Basin, to the NuStar Energy Corpus Christi terminal. The Nueces Bay connection would complete the second stage of the NuStar Energy export project, an 8-mile (12.9-km), 30-inch (72.6-cm) pipeline from the existing Cactus II pipeline located in Taft, Texas, to the NuStar Energy Corpus Christi terminal. Completing this final link beneath Nueces Bay would allow NuStar Energy to increase capacity of WTI crude from the Permian Basin, hence enhancing the growth of Gulf Coast crude exports from the Port of Corpus Christi to global markets.
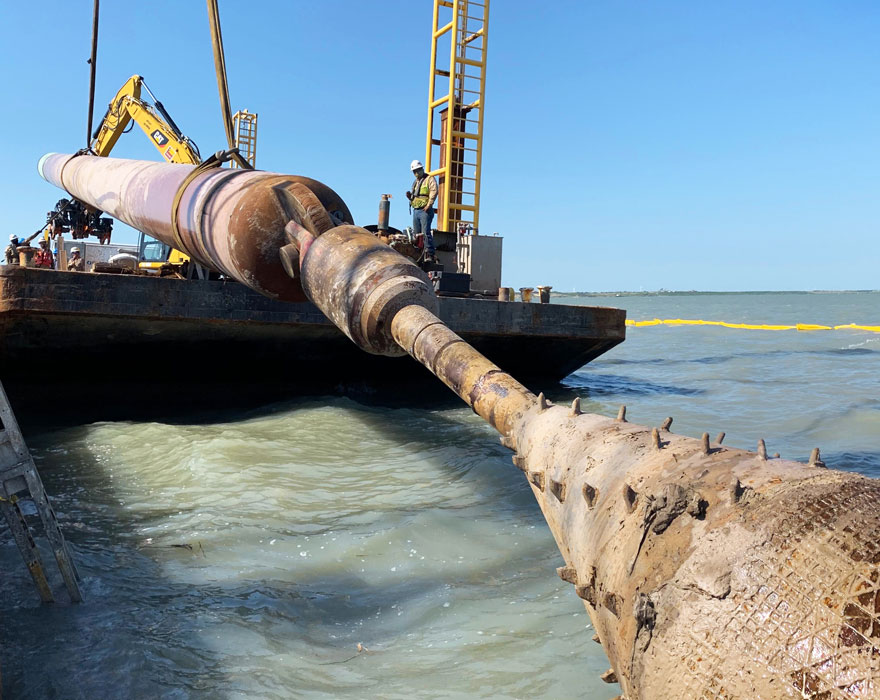
Plotting the bore course
As with every job, Forconi began by assembling his exceptional team of HDD bore planning and engineering experts to draw up design/build specifications according to the directions provided by NuStar Energy. The first step involved completing a geotechnical analysis and collecting data, including a soil composition analysis, to identify which layers would be best for drilling. From the geotechnical data, Forconi and his team determined the appropriate drilling depth of between 100 feet and 120 feet (30.4 m and 36.6 m). With the soil composition data identified, Forconi’s team then specified an annular pressure plan, completed a hydro fracture analysis and determined product pipeline specifications. Given the length, two bores were required, intersecting at a midway point beneath the often-turbulent waters of Nueces Bay.
With the design/build plan completed and approved by NuStar Energy, the Hard Rock Directional Drilling team got to work. They selected the Vermeer D1000x900 Navigator® horizontal directional drill rig for the job because of its sheer power and capability of pulling back the immense weight of the 30-inch (76.2-cm) steel casings that would be welded together in one continuous length. This assembly approach required excavation of a 30-foot (9.1-m) ditch in the bay to create a hole for the exit and intersection tie-in point. Depth of the bay water at the location was approximately 5 feet (1.5 m), which was sufficient enough to support the barges that would position continuous lengths of pipeline to be pulled back once the bores were completed.
Two methods of excavation were implemented; clam on a crane positioned on a barge and a hydro lift with the divers down below. The intersection hole was dug using the clam bucket situated on the barge with follow-up excavation using a pump to hydro-lift more material out to achieve the necessary depth. Orion Marine Group, based in Houston, Texas, provided the marine equipment and cranes needed to support pipeline material and excavation equipment.
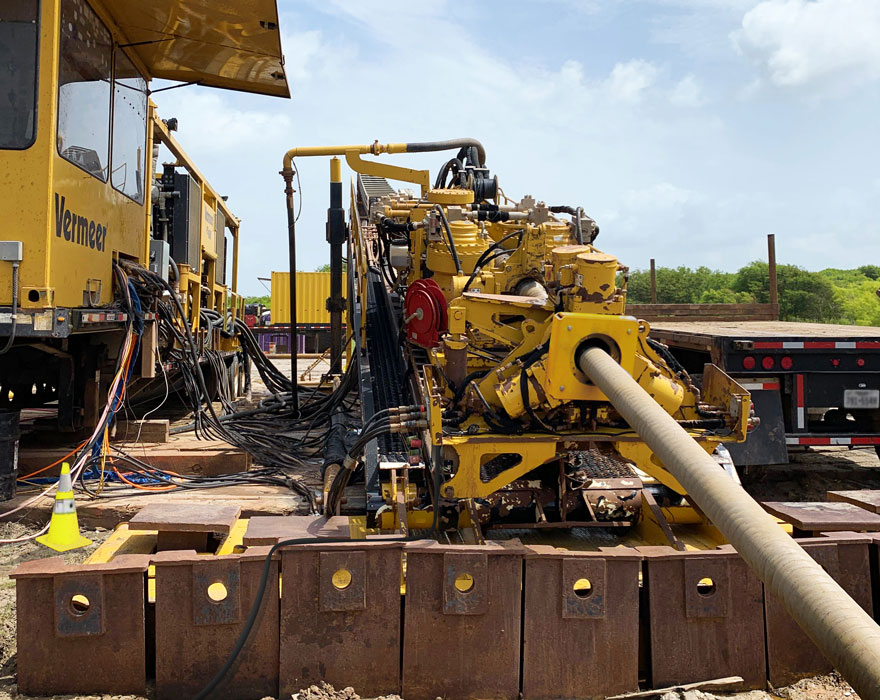
Two Vermeer D1000x900 drills were employed to complete the bores; one positioned on the south shore and the other directly across the bay on the north. Shallow exit angles of 4° (.1 rad) were calculated by the Hard Rock Directional Drilling team to assist in making the tie-in less complicated. The south side bore was a bit more challenging due to resistance from an oyster reef composition that extended approximately 7,300 feet (2,225 m) beneath the bay. A tong hammer was used to break and add stem.
Drilling fluid used for each bore consisted of 100% bentonite, selected for its composition properties that are ideal given the soil composition and potential influence of bay water during bore exit and intersection tie-ins. The project required three passes originating from each shore beginning with a 12-1/4-inch (31.1-cm) pilot bore, followed by a 30-inch (76.2-cm) ream pass and the final 48-inch (121.9-cm) pass.
The product pipe from the south side was welded in one continuous length on the shoreline and positioned on floats over the bay waters. The south side pipeline was completed first before the north side began. The HDPE material for the north bore was welded in one continuous length and positioned in the bay waters on floats in the same way as the south side.
South meets north…right on target
With the bores completed, it was time for the Hard Rock Directional Drilling team and Orion Marine Group crews and divers to complete the intersect.
“The tie-in is accomplished by setting up a support apparatus approximately 120 feet (36.6 m) in front of our work barge,” Forconi said. “The divers then go down after we punch out and rig us to our downhole tooling. It’s basically a support post that looks like a football goalpost and we push out far enough to get the tooling to lay flat on the deck. The crane lifts the tooling up and we push out and up over the goalpost. And then we have two tong handlers out there, one for each side.
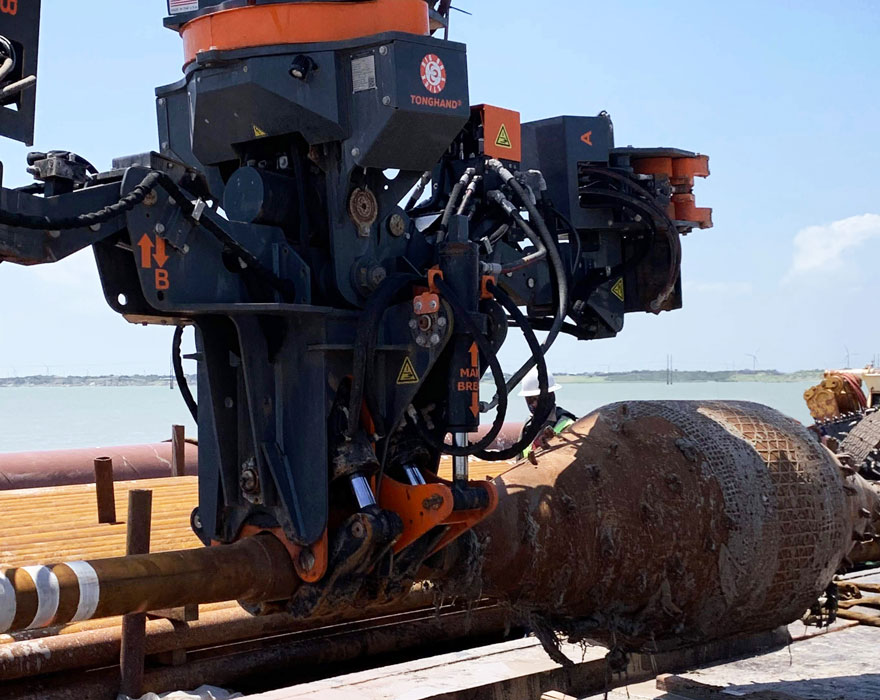
“The same tongs are used to remove our steering tools and the bottom hole assembly. A jointed drill stem is then mounted on the back of that with a plugin. As the drill operator pulls it down to the bottom, we support the stem with the crane barge. When the assembly reaches the bottom, the divers take the rigging off and keep adding stem as the drill operator pulls it back.”
Once connected, the north shore drill operator skillfully pulled back the pipeline to eliminate slack. Sections of both pipelines needed to be coated with concrete to control the buoyancy created by the bay waters during install. Also, the team determined that the HDPE lines that would be housed inside the steel casing could not be safely added after the pipe string was in place as originally planned out of concern of breaking inside the product pipe. So, it was floated into position inside of the product line and then blown out with compressed air to excavate the water and become buoyant inside the 30-inch (76.2-cm) line.
The project was completed in 37 days. Soon after, WTI crude was flowing freely to the NuStar Energy Corpus Christi terminal. It was the final leg in a vital pipeline system for transporting the oil-rich reserves of the Permian Basin to the Port of Corpus Christi, and on to markets around the globe.
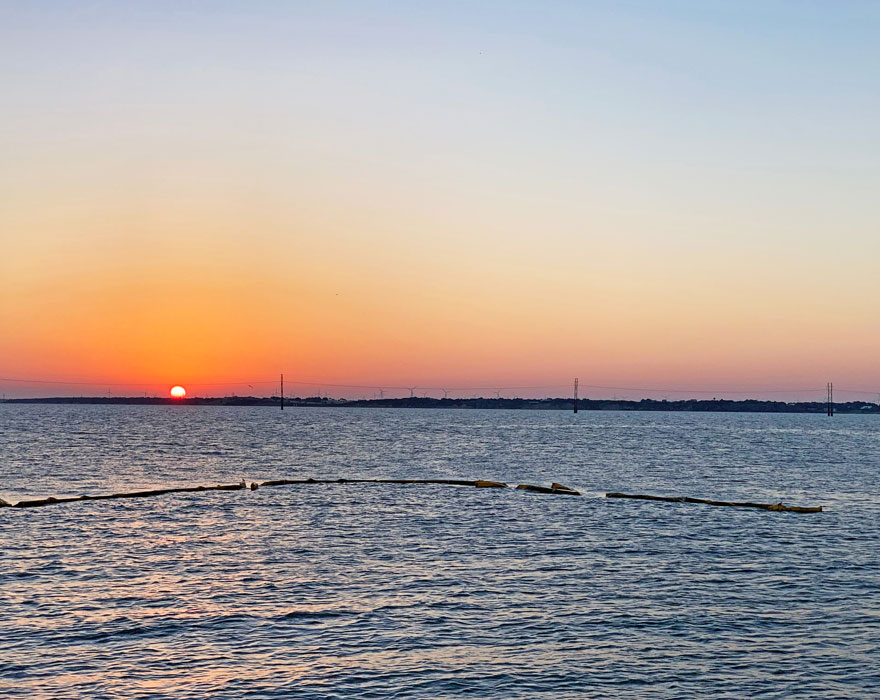
Design, planning and experience
“The key to the success of this project all started with the design, then securing Orion Marine Group to assist in determining what kind of equipment would be required out in the bay,” Forconi said. “Orion Marine Group was responsible for getting the product and pulling it out there with their barges into the bay with Hard Rock Directional Drilling team support. We were positioned offshore to handle fabrication of the pulling assembly, and then just install it from there.
“Hard Rock Directional Drilling has tremendously skilled, competent and talented people. We have an impressive safety record and trusted relationships with the gas companies and general pipeline contractors. With our experience, and all our people that we have on board here, we can basically figure out the best approach to even the most challenging projects. We come together as a team. It starts with the design and then just kind of snowballs from there. We have all the resources, track record and experience to get the most complicated and difficult jobs.
“Other than the tides being low at a certain time the project went amazingly smooth. We really didn’t have any issues. We put a lot of time and thought into the type of product carrier pipe for the south bore, especially the 450-foot (137.2-m) concrete-coated section of it that needed to be fabricated on land before being placed on floats and set in the water. It took a lot of engineering to get that set into the water safely and able to float that concrete-coated section. We were pleased with how well the job went overall.”
This article contains third-party observations, advice or experiences that do not necessarily reflect the opinions of Vermeer Corporation, its affiliates or its dealers. Testimonials and/or endorsements by contractors in specific circumstances may not be representative of normal circumstances experienced by all customers.
Vermeer Corporation reserves the right to make changes in product engineering, design and specifications; add improvements; or discontinue manufacturing or distribution at any time without notice or obligation. Equipment shown is for illustrative purposes only and may display optional accessories or components specific to their global region. Please contact your local Vermeer dealer for more information on machine specifications. Vermeer, the Vermeer logo and Navigator are trademarks of Vermeer Manufacturing Company in the U.S. and/or other countries.
© 2020 Vermeer Corporation. All Rights Reserved.