From pilot bores to reaming, HDD drilling fluid is working hard downhole to allow a successful installation. While the only thing you and your crew get a chance to see is the slurry returns, you should still know the purpose of common drilling fluid additives and how they work.
What to consider with drilling fluids
Before diving into details about the additives that make up a drilling fluid, here is what you need to think about when mixing mud.
- Viscosity — This term is used to describe the drilling fluid’s ability to flow downhole. The thinner the mixture or lower the viscosity, the higher fluid will flow downhole. However, thicker or higher-viscosity muds are more efficient at carrying cuttings from the drill hole.
- Gel strength — This term directly addresses the drilling fluid’s ability to support, suspend and carry cuttings. Gel strengths need to be high enough to efficiently flush cuttings from the drill hole to help maintain fluid circulations. If pressures build and flow are slowed or stopped altogether, the result can be an inadvertent return and/or a stuck drill string.
- Filter cake — This term describes a protective barrier between the drill string and bore walls. The filter cake helps prevents fluid loss in porous soil conditions and helps desired fluid pressures to be maintained.
From here, it’s time to talk about HDD drilling fluid ingredients/additives.
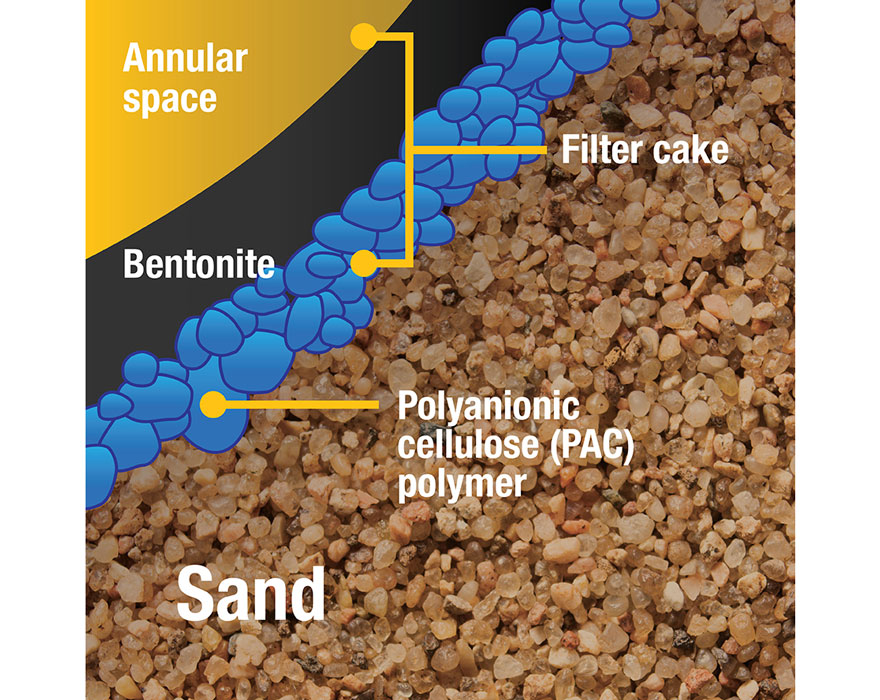
Water
The main ingredient of HDD drilling fluid, water, is sometimes used alone in certain soil conditions. However, water offers very little in the way of lubrication and lacks viscosity to maintain hole integrity and gel strength to float cuttings out of the hole. What water does do is provide a good base for additives and help cool HDD tooling.
Soda ash
Not all water is the same — its acidity/alkalinity pH levels can vary depending on the source. The optimal pH level for mixing HDD drilling fluid is between 8 and 9. Adding soda ash to water is an easy way to raise pH levels to that desired range, helping attain optional product hydration/yield.
Bentonite
A staple of almost all HDD drilling fluid mixes, bentonite helps create higher viscosity downhole, provides some gel strength for flushing cuttings and creates a filter cake to help reduce fluid lost into surrounding formations.
Think of it this way — bentonite helps produce a thicker water mix. The more you add, the thicker it gets, which slows flow and increases its weight. Thicker/higher-weight mixes can carry more cuttings and create a good filter cake but flow slower through the drill path, which may not be optimal depending on the ground conditions. So, bentonite alone is not ideal for every bore. This is why HDD polymers exist.
Polyanionic cellulose (PAC) polymer
PAC polymers should be added to the drilling fluid mix when working in porous zones in loose ground conditions like sand. The main benefits that PAC polymers provide are helping prevent fluid loss downhole and avoiding oversaturation to the bore formation, which can result in the hole collapsing. It also helps to lubricate the bore path and prevents bit balling (cuttings that stick to the drill bit).
Partially hydrolyzed polyacrylamide (PHPA) polymer
PHPA polymers should be used in reactive clays and shale. Downhole, PHPA bonds with the outer layers of the ground material and cuttings to help prevent fluid from absorbing and swelling, which also helps reduce it from sticking to HDD tooling.
Other HDD drilling fluid additives to consider
- High molecular weight (HMW) polymer should be used in cobble, sand and gravel ground conditions. It increases the drilling fluid’s gel strength so heavier cuttings can be flushed from the bore path.
- Detergents are used to lubricate downhole and keep tooling clean.
- Xanthan gum is used to boost the drilling fluid viscosity without increasing its density.
- Foam can be a good option to consider when drilling through rock formations more prone to chip instead of cut. The foam helps to float these chips and flush them from the drill path.
Now that you have a little better understanding of the common additives used to mix up a great batch of mud, it’s time to get mixing. For more information about this process, be sure to check out the Pro Tips three-part series “Making Sense of HDD Drilling Fluid.”
- Part 1: Why drilling fluid is essential to HDD and the mixing process
- Part 2: Calculating reamer pullback drill rates
- Part 3: Making sense of HDD drilling fluid additives
If you need any help in the process, give your local Vermeer dealer a call. In the meantime, learn more about Vermeer HDD mix systems.
Vermeer Corporation reserves the right to make changes in engineering, design and specifications; add improvements; or discontinue manufacturing at any time without notice or obligation. Equipment shown is for illustrative purposes only and may display optional accessories or components specific to their global region. Please contact your local Vermeer dealer for more information on machine specifications.
Vermeer and the Vermeer logo are trademarks of Vermeer Manufacturing Company in the U.S. and/or other countries. © 2021 Vermeer Corporation. All Rights Reserved.