Horizontal directional drills are rugged machines designed to handle challenging situations. They are engineered to function in tough ground conditions and environments. Nonetheless, HDD rigs are still susceptible to the normal wear and tear that comes with any piece of hard-working equipment. When a contractor or operator inspects an HDD rig, one of the many checkpoints should be the drill rods.
“The drill rod is one of the most important components of an HDD rig, besides the driving components and engine. Without quality, well-maintained rods, you aren’t going anywhere. They are designed to bend and flex throughout the boring process to help achieve a pilot bore and a backream,” says Chris Fontana, BORESTORE sales manager for Vermeer.
First, it is important to understand the different designs and technology of drill rods. Commonly, drill rods are either three pieces welded together or one-piece forged rods. Fontana recommends the latter option for smaller-sized drills. The one-piece forged rods are created from raw tube with each end subjected to a heating and upsetting process to gather enough material to create a tool joint. The tube is also subjected to a final heat treatment to give the rod a consistent hardness from end to end.
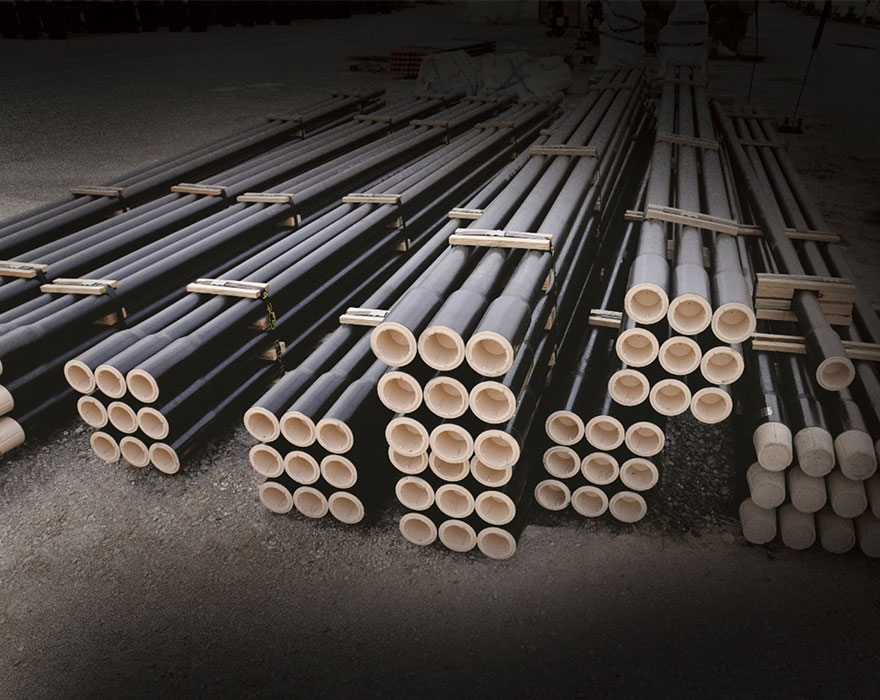
The box and pin ends — sometimes referred to as female and male ends — are threaded. This creates a robust, tapered tool joint that when properly torqued on make-up, flushes the internal and external shoulders and carries the force on the rear load flank, thus creating the strongest joint for HDD applications.
Drill rods are engineered to provide a combination of flexibility, strength and durability, which is needed for a wear part that endures the demands drill rods encounter. In order to meet those demands, such as extreme bending and torque, drill rods are manufactured from special material alloys.
“It’s important to choose the right processing, the right material. You need to have a material that can be wearable and durable, but also has that bend and flexibility needed for HDD,” says Fontana.
The drill rods are unique to the HDD world and must be monitored and maintained differently than other components. With the consistent forces of thrust, torque and friction that wear on a drill rod, they face different maintenance demands.
The most important practice to help the longevity for each drill rod is rotating the lead rod in the rack. With the variety of materials that can be found underground — from challenging cobble to solid limestone — relying on one rod to be the first underground at each jobsite can cause that rod to wear at an unnecessarily rapid pace. By rotating the lead rod in the rack weekly, an operator can minimize the risk of a single rod suffering the most damage.
The ends of the drill rod also require maintenance. Monitoring the threads on the end of each rod and lubricating each end regularly can prolong the life of a drill rod.
“Thread lubrication is also important on every joint. Every time you thread the rod together and every time you put a tool joint together, you need to apply the recommended amount of lubricant,” Fontana says.
Completing a visual inspection of the threads on a regular basis is a smart first step toward familiarizing oneself with the difference between healthy and worn drill rods. However, Fontana recommends utilizing one simple tool to help identify issues early.
“We recommend always using thread gauges as an augment of visual inspection. A thread gauge is a very small, easy-to-operate tool that can be placed on the keychain of the rig. If you just rely on appearance, it’s probably too late when you finally notice an issue,” Fontana says. “Also, each upset needs to be inspected. Ideally, the rods would wear out from the outside in and the upset will wear before the thread.”
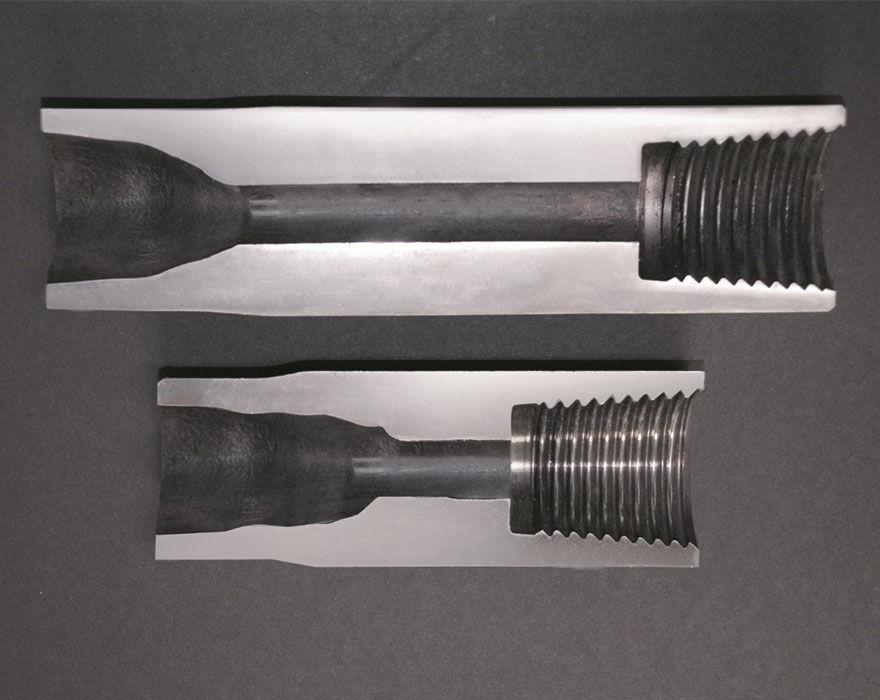
The components of the drill that stay above ground and come into contact with the rod should be closely monitored for wear or damage. Along with the upset and the threads, the sub saver and drive chuck should also be monitored frequently. Refer to the drill’s manuals for the manufacturer’s recommendations.
“The first thing that touches the rod is the drive chuck and sub saver. Sub saver maintenance is crucial. Changing the sub saver often to preserve the thread will help to prevent thread damage from rod to rod,” Fontana says.
Sub savers are manufactured to handle the tolerance of HDD rigs. Much like the drill rods, sub savers feature specifically forged threads that are meant to create a strong tool joint with each rod placed on the rack. The drive chuck is created from a special alloy to provide increased strength where it connects to the head-shaft. Together, the sub saver and drive chuck help ensure proper torque.
While it is not an exact science, drill rod life cycles tend to be correlated to the ground conditions in which they often drill. Ground conditions impact every facet of a boring project and the HDD rig.
For drill rods, it is especially important for the operator to efficiently remove cuttings from the bore. If the hole is not cleaned, the residual cuttings can hasten the wear on the outside of the drill rod.
The engineering and care required to maintain quality drill rods demands great precision. From the metals used to create a drill rod to the checkpoints inspected as part of a routine maintenance schedule, the depth of specialized care involved is key to maximizing the productive life of drill rods.
Vermeer Corporation reserves the right to make changes in product engineering, design and specifications; add improvements; or discontinue manufacturing or distribution at any time without notice or obligation. Equipment shown is for illustrative purposes only and may display optional accessories or components specific to their global region. Please contact your local Vermeer dealer for more information on machine specifications.
Vermeer and the Vermeer logo are trademarks of Vermeer Manufacturing Company in the U.S. and/or other countries. © 2022 Vermeer Corporation. All Rights Reserved.