Being prepared to drill in rock with the correct tooling will help maximize your productivity on the jobsite.
If you are expecting hard ground or soft rock, come equipped with a specialty plate bit such as the Vermeer Ace™ bit, Armor drilling system or Ultra X3 system. Ace bits are developed with carbide inserts. This allows contractors to push boundaries of what a plate bit can do. With the Armor drilling system and Ultra X3 system you can select from a wide range of specialty bits that are efficiently switched out as ground conditions change. Ace, Armor and Ultra X3 are economical ways to handle difficult conditions without investing in more dedicated rock systems.
Drilling in medium rock? Armor drilling system, Ultra X3 system or a dual rod system — such as a D23x30DR S3 Navigator® horizontal directional drill (HDD) or a D40x55DR S3 Navigator HDD — will set you up for efficient work. The dual-rod technology uses an inner rod to provide torque to the drill bit, while the outer rod offers steering capability and rotational torque for reaming. That combination provides powerful downhole cutting action and the flexibility to select the appropriate tooling to best match the ground conditions, which can allow the entire install to be completed with one machine.
When drilling in hard rock a dual-rod machine can also be a great option, but if you have a conventional HDD, it is beneficial to have a mud motor or air hammer.
Drilling into fractured or solid rock also makes a difference. For fractured rock, you’ll want to be equipped with a tricone. For solid rock, using a polycrystalline diamond compact (PDC) hole opener will provide performance and reliability to consolidated rock bores.
View the chart below to discover which tooling is best for different kinds of rock.
Still not sure what kind of tooling is best for the rock you’re drilling into? Sending a sample from your jobsite to the Vermeer Rock Lab can help you determine the right tooling to use. Contact your local HDD specialists with any additional questions.
Learn more about rock tooling and your options by visiting borestore.com.
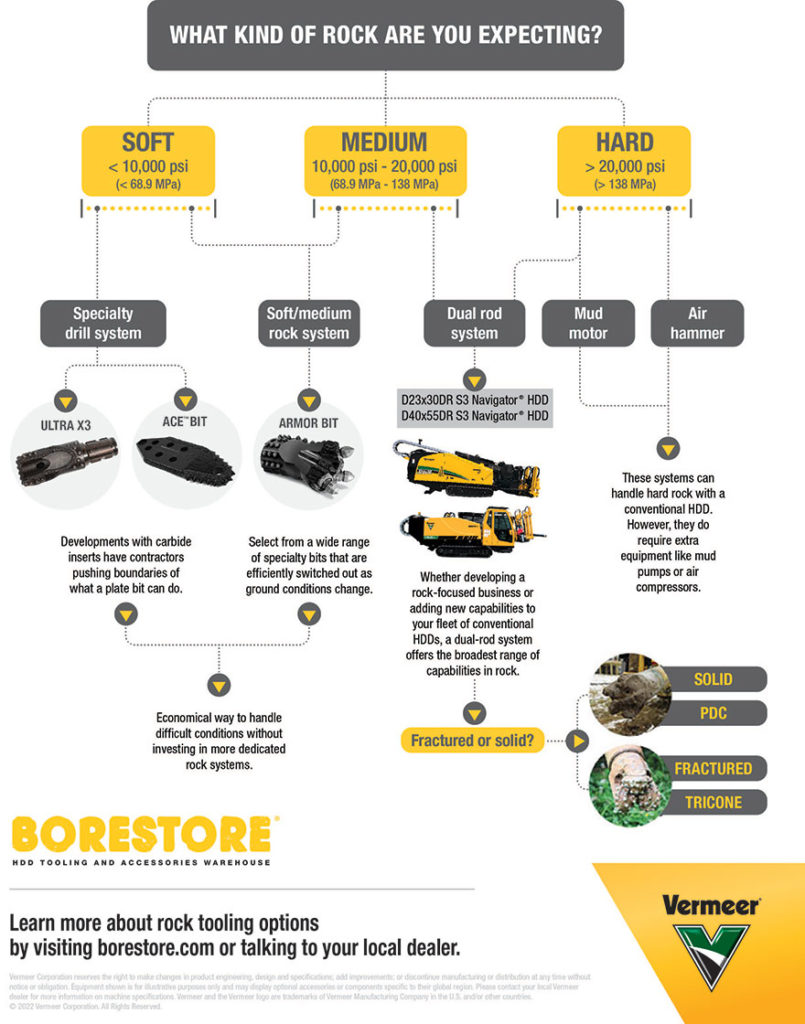
Vermeer Corporation reserves the right to make changes in product engineering, design and specifications; add improvements; or discontinue manufacturing or distribution at any time without notice or obligation. Equipment shown is for illustrative purposes only and may display optional accessories or components specific to their global region. Please contact your local Vermeer dealer for more information on machine specifications.
Vermeer and the Vermeer logo are trademarks of Vermeer Manufacturing Company in the U.S. and/or other countries. © 2022 Vermeer Corporation. All Rights Reserved.