High-pressure stand-alone mud pumps such as the SA400 are constantly tackling tough pipeline drilling projects alongside horizontal directional drills, or HDDs. Tough jobs mean operators should take extra steps when possible to maximize the life of the machine. These steps can vary from visual inspections of the machine to performing preventative maintenance tasks on schedule. Refer to your machines operator’s and maintenance manual for safety messages and further information. Now we will go over some operator best practices that can help extend the life of your mud pump.
Daily wear
With the jobsites that these mud pumps encounter, it is no surprise that some parts of the machine can experience considerable wear. High sand content and mud weight on a jobsite will affect the life span of fluid-end components on your pump. Parts on the mud pump that may experience heavy wear include, but are not limited to:
- Pistons
- Liners
- Valves
- Valve springs
- Valve seats
After finishing up on a jobsite, it is a good practice to inspect these parts to look for signs of wear.
Another area of the mud pump operators should diligently monitor are the intermediate rod seals. If a leakage occurs, these seals will need to be adjusted periodically by following the steps outlined in your machines operator’s manual.
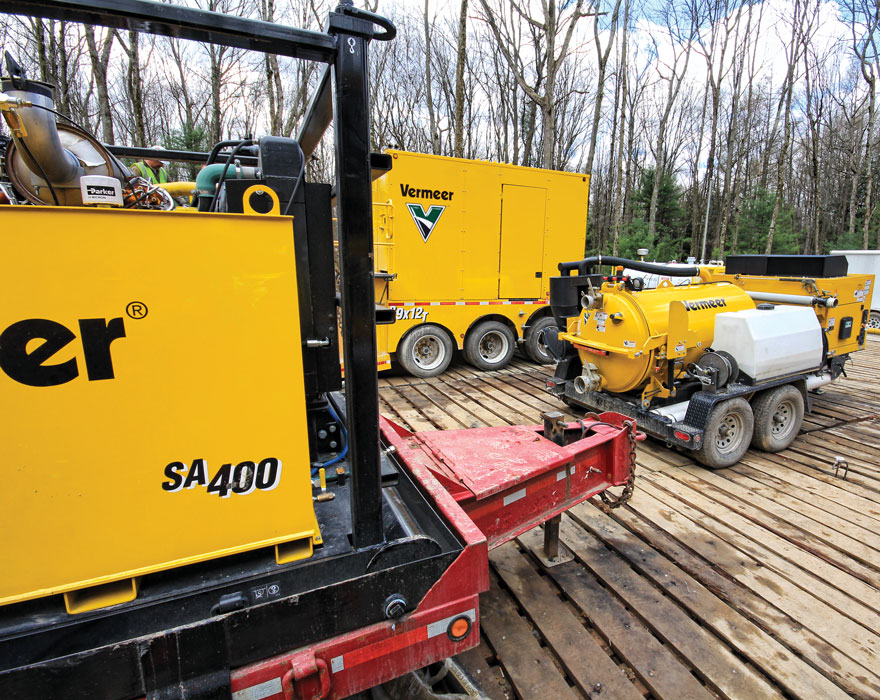
Maximizing machine life
Performing preventative maintenance is a game-changer when it comes to helping extend the life of your mud pump. It is recommended to check lubrication levels daily and inspect the transmission, gear reducer and drive motor. After a job is complete, flush the pump so that it is ready to head to the next jobsite. If the pump will not be used for an extended period of time between jobs, it is recommended to lubricate liners, pistons and valve seats. Doing this will help prevent the liners and seats from becoming pitted due to condensation.
When temps begin to drop, operators will want to remove all drilling fluids from the pump, hoses and any exposed drill string. After that is complete, fill the end of the mud pump with antifreeze, which will offer protection from freezing temperatures beyond what is anticipated. Planning and performing this maintenance before temperatures drop is key to optimizing machine performance.
Operator best practices
These pumps are typically used on large-diameter projects, which means going at a slower rpm can maximize machine longevity and productivity. While the pump is processing heavy material, if it is run too quickly, it could affect machine performance. Keeping an eye on the rpm and adjusting when needed can help avoid plugging the pump with heavy material.
When setting up at the jobsite, remember to set the mud pump onto a level area of ground. Inside the pump many internal components only receive splash lubrication and if the pump is working on uneven ground, it is more difficult for those components to receive the adequate amount of lubrication.
Developing a consistent routine to check fluid levels and the condition of highly wearable parts will go a long way when it comes to maximizing the life of your mud pump. It is essential that operators take the time to inspect the pump between jobs and utilize the operator’s and maintenance manual for further instructions and safety messages.
For more information on Vermeer high-pressure mud pumps, contact your local dealer.
Prior to performing service or maintenance on Vermeer equipment, always refer to the product’s operator’s and/or maintenance manual for safety messages and further instructions. Vermeer Corporation reserves the right to make changes in product engineering, design and specifications; add improvements; or discontinue manufacturing or distribution at any time without notice or obligation. Equipment shown is for illustrative purposes only and may display optional accessories or components specific to their global region. Please contact your local Vermeer dealer for more information on machine specifications.
Vermeer and the Vermeer logo are trademarks of Vermeer Manufacturing Company in the U.S. and/or other countries. © 2022 Vermeer Corporation. All Rights Reserved.