Demand for new solar projects is high, and skilled labor availability is low. So, how do you, a general contractor, give your crews the support they need to get all the work done on new solar construction projects?
That’s a question many contractors are asking themselves these days. And most will agree that adding automation to the solar construction process is critical. Enlisting equipment that requires less operator input and support labor can help crews maintain high production rates throughout the construction process.
As a leading equipment provider for renewable energy construction and utility work, Vermeer has been hard at work developing new onboard technology to help make the time-consuming and labor-intensive application of driving piles more automated. And at the beginning of 2022, Vermeer introduced the optional point-to-point (PTP) system for Vermeer PD10R pile drivers.
“The Vermeer PTP system helps minimize the number of manual steps involved with positioning and aligning the pile driver on solar projects,” said Bo Howell, product specialist at Vermeer. “Throughout the course of a normal day, where many rows of piles are being installed, PTP technology can help operators maintain precise accuracy and work more efficiently.”
What is the point-to-point system?
The Vermeer point-to-point system allows PD10R pile drivers to reposition themselves automatically using onboard GPS. After one pile is driven, the operator presses a button on the remote control, and the pile driver travels to the next coordinate and aligns to go to the next pile. This technology helps minimize the number of steps required from the operator during the pile driving process on solar construction projects.
So why is that a big deal?
If you’re asking that question, you need to compare what’s required of the operator using a pile driver with or without GPS and a PD10R outfitted with the optional PTP system.
Driving piles with lasers and levels on solar projects
While most large-scale solar projects use pile drivers equipped with GPS for installing piles, not every machine integrates it to perform machine functions like Vermeer pile drivers do.
Pile drivers that do not integrate GPS with functionality require significant operator input to get piles aligned vertically and horizontally. In many cases, a laser is used to set up a string line to keep rows of piles aligned and maintain pile spacing. Then levels are used to check that the pile is plumb while being driven into the ground.
“It’s a time-consuming process and not efficient on large solar projects,” said Howell. “So, early on, when we developed our first PD10 pile driver, we worked with GPS technology experts to integrate information with machine functionality. Doing this allows PD10, PD10R and PD5R pile drivers equipped with GPS to align piles vertically using the auto plumb feature.”
Driving piles with a Vermeer pile driver equipped with GPS
A GPS-equipped Vermeer pile driver helps crews work more efficiently on solar projects and maximize accuracy. Operators are required to manually position the pile driver near the location where the pile needs to be installed. But then the onboard GPS takes over the process of precisely aligning the pile vertically and horizontally using auto plumb and auto-target integration between the GPS and Vermeer pile driver technology. From there, the crew loads the post into the guides, and then manually engages the hammer. Once the pile is at the desired height, the hammer automatically disengages, and the GPS logs the data.
After that, the operator lifts the hammer, retracts the mast from the post and navigates the machine to the next target. “All this can be done using joysticks and a few button pushes,” said Howell. “It’s not time consuming or labor intensive, but it does demand a lot of operator input and attention to do this type of work for several hours a day.”
Automating pile driving with the point-to-point system
While the technology incorporated into Vermeer pile drivers significantly minimizes the steps involved in driving piles on solar projects, the PTP system takes things to another level.
A PD10R using PTP technology minimizes the number of operator input steps from 11 to 4 per cycle. “The pile driver can automatically perform seven machine functions that used to require manual input,” said Howell. “This helps keep operators and crews working efficiently and minimizes the number of laborers required to load piles throughout the process.”
With the point-to-point system, the machine automatically navigates to the next pile location, aligns the mast vertically and horizontally, then lowers the hammer so the next pile can be lifted and loaded. The operator then raises the hammer with the push of a button and places the pile in the machine’s guide. From there, the push of a button engages the hammer floats. When the pile is at the desired height, the PD10R automatically starts and stops the hammer.
Once a pile is driven, a single button push raises the hammer, slides the mast away from the pile, moves the pile driver to the next pile site and lowers the hammer so the next pile can be loaded and lifted. “During this repositioning time, operators still need to monitor the pile driver’s functionality, but they can also help get the next pile ready to be lifted. This can help minimize the number of people needed to support pile driving operations,” Howell explained.
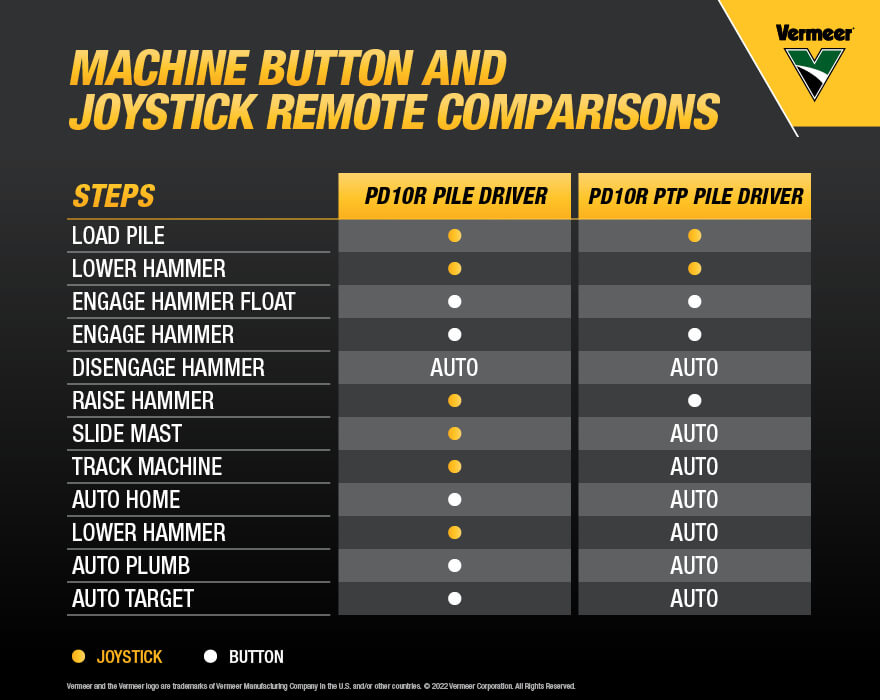
Advantage of automation
As you can see, many advanced technologies are being incorporated into pile driving equipment to maximize productivity on solar construction projects. The Vermeer PTP system is a significant step forward in automating the process. The PD10R recognizes the next waypoint (pile location) and moves into position by syncing GPS coordinates with digital project maps of pile sites. This minimizes operator input and allows everything to be installed according to specs.
Talk to your Vermeer dealer for more on PTP technology and to discuss options for adding optional PTP technology to your new or existing PD10R.
Vermeer Corporation reserves the right to make changes in engineering, design and specifications; add improvements; or discontinue manufacturing at any time without notice or obligation. Equipment shown is for illustrative purposes only and may display optional accessories or components specific to their global region. Please contact your local Vermeer dealer for more information on machine specifications.
Vermeer and the Vermeer logo are trademarks of Vermeer Manufacturing Company in the U.S. and/or other countries. © 2022 Vermeer Corporation. All Rights Reserved.