A crew of 10 horizontal directional drilling (HDD) professionals with D&C Directional Boring, based in Townsend, Georgia, is wrapping up a long summer project outside Savannah’s busy ports. Their work has been part of the Savannah Economic Development Authority’s (SEDA) construction of the Savannah Manufacturing Center — a 2.5 million-square-foot (70,792.1-m3) industrial development that will soon be a logistical transportation hub to many of the country’s largest tech and consumer retail companies. Using the company’s Vermeer D220x300 S3 HDD paired with a Vermeer R250C reclaimer, D&C’s task on this project involved installing 24-in (61-cm) HDPE forced sewer and 30-in (76.2-cm) fusible PVC water mainlines through the area’s wetlands.
Led by the husband and wife team of Dennis and Carla Williams, their oldest son, Tommy, and grandsons, Nathan and Brent, D&C has gone from a one-utility-drill company to the Savannah area’s go-to trenchless water and sewer contractor in the last 10 years. Now, operating as many as three crews at once with multiple utility and maxi drilling rigs, pneumatic boring and bursting tools, D&C specializes in municipality installation and rehabilitation work.
SEDA Savannah Manufacturing Center project
As with any major industrial development project, there is a great deal of planning and construction involved in the SEDA’s Savannah Manufacturing Center project before the first business sign can be hung. For instance, the location of the center presented several challenges for developers because of the amount of wetland area within and near the area. To bring water and sewer services to the site, the SEDA project called for both open-cut and trenchless methods.
“The project was broken down into two phases: onsite SEDA and offsite SEDA,” Dennis explained. “Almost all of the installation work onsite was drilled, while a combination of methods was used for the offsite work to connect the onsite piping with Savannah’s existing infrastructure. Our team handled the HDD work onsite and offsite.”
Onsite SEDA
The bores for the SEDA project were quite involved, said Dennis, so the D&C team needed to pool their resources to complete the work. This project was one of the first for the company’s newly commissioned Vermeer D220x300. “We also own Vermeer D24x40 and D100x120 Series II HDDs,” added Dennis. “The D100x120 Series II has been a workhorse ever since we purchased it. It’s the most productive machine we’ve ever owned, and it’s made us a lot of money. But, for this type of work, we needed something bigger.”
The onsite bores the crew needed the bigger maxi rig for included a 1,800-ft (548.6-m) bore for a 30-in (76.2-cm) water main, a 1,800-ft (548.6-m) bore for a 24-in (61-cm) forced-sewer main and 1,800-ft (548.6-m) bore of 6-in (15.2-cm) forced-sewer main.
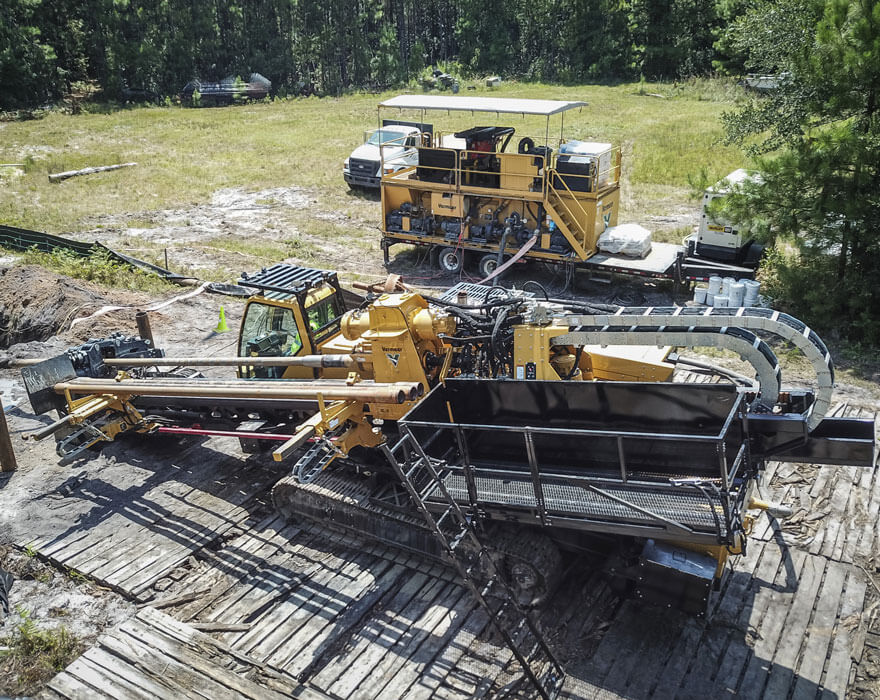
For the mainline work, D&C paired their 242,100-lb (1,076.6-kN) rig with the R250C reclaimer to recycle all of their drilling fluids. Dennis described the ground conditions as a “gumbo” — a mixture of sand and clay — that would swell if the drilling fluid wasn’t mixed just right. “We used 3 – 4 bags of bentonite for every 1,000 gal (3,785.4 L) of water, as well as a polymer to keep the clay from swelling to make a 42-second mud,” he said. “It did a nice job of carrying cuttings, while maintaining the hole integrity and keeping our tooling clean. Also, the R250C kept up just fine through it all during the pilot bore and with every reamer pass.”
Each of the three bores reached depths between 20 ft and 35 ft (7.6 m and 10.7 m), and the crew averaged around 100 ft (30.5 m) of drilling per hour on their pilot bores. After completing the pilot bore with a 12-in (30.5-cm) bit, the crew made a reamer pass with a 24-in (61-cm) Vermeer fly cutter reamer, followed by a 36-in (91.4-cm) fly cutter they pulled pipe behind.
Dennis said they had some concern about how the reclaimer would handle the thicker returns they were getting while reaming because of the size of cuts they decided to make with each pass. But everything went according to plan. “We rented a 6×3 assist pump to move mud from one pit to another and before it went to the reclaimer,” he explained. “We figured if the mud got too thick, we could thin it out a bit in the pit before it went through the recycler. We really didn’t need to do that, though. The R250C did a great job of keeping up with that big drill.”
Equipment pairing
For the D&C drill operator, Joe Brown, adjusting to the D220x300 from the D100x120 Series II drill was pretty easy. “While the D220x300 is a lot bigger, the controls are almost exactly the same — there’s just a lot more power at my fingertips,” he explained. “In fact, I had a chance to run a rented Vermeer D330x500 horizontal directional drill a couple of weeks before we got our drill on an emergency 24-in water main installation job. I went from one to the other and then back without any issues — they all feel pretty much the same.”
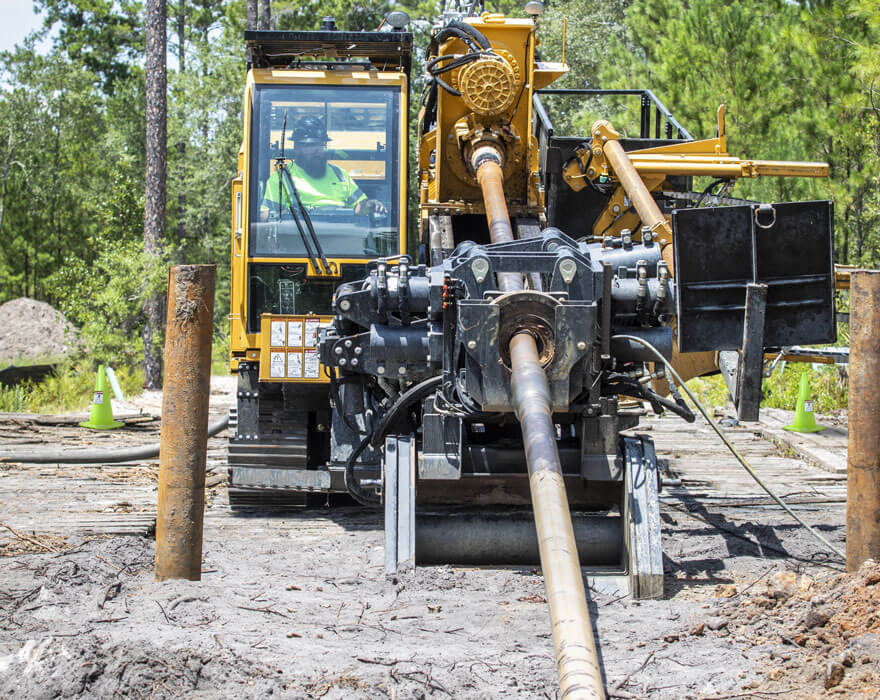
D&C has also used its R250C reclaimer with all three drills. “We originally invested in the reclaimer to pair with our D100x120 Series II because most municipalities around here now require drill crews to recycle their drilling fluids,” said Dennis. “But when we were called out on that emergency water main project, there wasn’t much time to think about finding a larger recycling system. I talked with Ken Coffield at Vermeer Southeast about how he thought the R250C would keep up with D330x500, and he said it could probably handle it in the ground conditions we were working. Ken and Mark Faddis with Vermeer Southeast set us up with everything we needed and helped dial in the R250C for that job. Everything went great. So, when we got our D220x300, we knew it would be able to keep up in similar conditions, and it has.”
While the Vermeer R250C is a 250 gpm (946.4 l/m) recycling unit, it may be possible to pair it with a larger HDD unit in certain environments. However, the drill operator needs to be very disciplined with monitoring pullback speeds to keep solids loading under control in the return fluids.
Offsite SEDA
D&C crews worked in similar ground conditions for the offsite SEDA work, so they stuck with the same drilling fluid mixture that worked onsite. “The bores were shorter, but there were more of them to do, and we weren’t just crossing under wetlands — there were highways, too,” said Dennis.
The offsite SEDA bores included a pair of 1,100-ft (335.3-m) bores for 30-in (76.2-cm) water and 30-in (76.2-cm) sewer mains. The crew also did four 800-ft (243.8-m) long connection bores for 24-in (61 cm) forced-sewer lines. Everything went according to plan for the D&C HDD professionals.
“Our team did an excellent job on this project. Most of our people have been with Carla and me since almost the beginning. They show up ready to work every day, and when it’s time to go home and relax, we all seem to hang out with each other then, too. We’re all pretty close,” said Dennis.
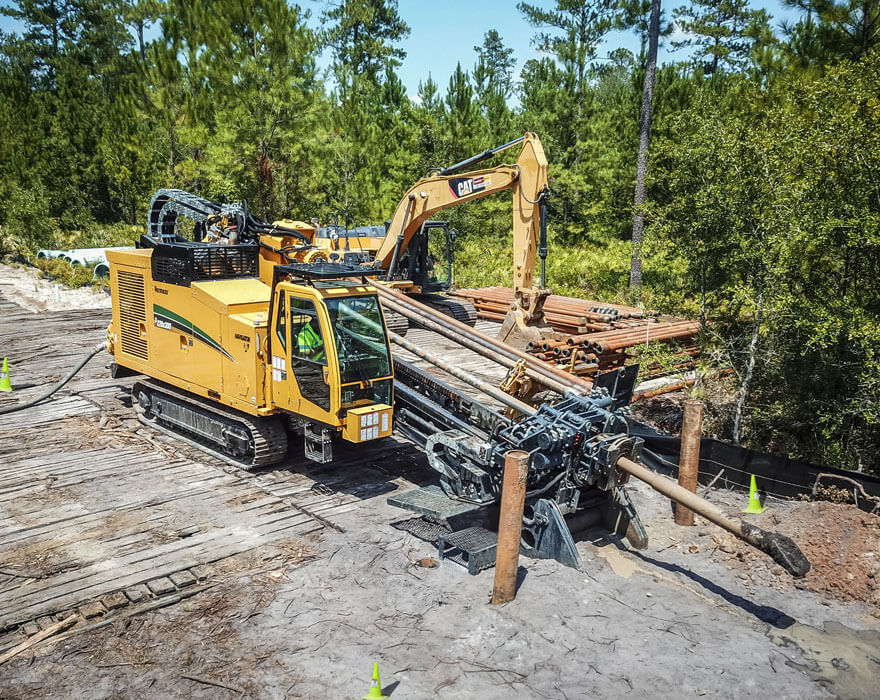
Looking back
According to Carla, her husband Dennis has always been one of the best contractors in the business, but it wasn’t until they made the shift from small-diameter utility installs to large-diameter water and sewer work that he found his true calling. “He was asked to bid on a water and sewer project around 10 years ago and got it. Soon after, we put every penny of our savings into the business, so they would have what they needed to get the job done. Those were scary days, but it’s all been worth it. We’ve been able to spend our time with great people doing what we love. Dennis handles the bidding and managing the crews, and I help out with the books and wherever else I’m needed,” Carla said.
Dennis added that they have built a great business as a family. “It’s been a huge blessing to have our kids and grandchildren as part of the business, as well as my very supportive wife,” he explained. “Carla works full time running a convenience store and makes sure all our business paperwork is getting done. She’s always been supportive of what I want to do and understands when we need to add new equipment to make that next step as a company. I don’t think we’ll ever grow too much beyond the kind of work we do now, but whatever we do, I know we’ll do it as a family.”
For more information about Vermeer drills and reclaimers, contact your local Vermeer dealer today.
This article contains third-party observations, advice or experiences that do not necessarily reflect the opinions of Vermeer Corporation, its affiliates or its dealers. Testimonials and/or endorsements by contractors in specific circumstances may not be representative of normal circumstances experienced by all customers.
Vermeer Corporation reserves the right to make changes in product engineering, design and specifications; add improvements; or discontinue manufacturing or distribution at any time without notice or obligation. Equipment shown is for illustrative purposes only and may display optional accessories or components specific to their global region. Please contact your local Vermeer dealer for more information on machine specifications. Vermeer, the Vermeer logo and Navigator are trademarks of Vermeer Manufacturing Company in the U.S. and/or other countries. © 2020 Vermeer Corporation. All Rights Reserved.