Also known as fluid mixing systems, mud mixing systems for directional drilling are essential to efficient boring operations. Choosing the right system or systems to support your horizontal directional drill (HDD) will help keep crews working efficiently all day.
Size and horsepower, system configuration, tank capacities and ease of use are a few variables you should consider when purchasing a mud mixing system for directional drilling. The ideal configuration should be convenient to transport and able to support your drilling operations with minimal delays. That often means pairing multiple fluid mixing systems with larger drills or on bores with higher volume requirements.
System size
According to Clint Recker, product manager for trenchless products at Vermeer, the first place to start when purchasing a mud mixing system is to select the size that complements your drill size.
“Powerful systems like the Vermeer MX300 mixing system will work with smaller utility drills through midsize rigs,” he said. “However, systems like the Vermeer MX125 mixing system pair nicely with smaller drills. It’s important to find a good balance between mixing production needs with the transportation requirements of the mud mixing system.”
Tank selection
Next, you need to determine how much fluid your crew needs on the job. Tank sizes range from 300 gal to 1,000 gal (1,135.6 L to 3,785.4 L), and systems like the Vermeer MX300 can be paired with one or two tank options to provide even more fluid on a project. Larger-capacity tanks require higher flow rates to allow the liquid to be mixed correctly. When projects require higher fluid volumes, you may want to consider having two complete MX300 mud mixing systems or a mud recycling system like the R250C reclaimer for efficient operation.
“Choosing the appropriate tank capacities is tied to drill sizes and the required fluid flow and volume needed to support the borehole and reaming size adequately,” explained Recker. “Contractors also need to think about the distance water is from the work they are doing each day. How feasible is it to put drilling operations on hold if a new batch of mud needs to be mixed during the day? Those considerations will not only help them decide what tank size is appropriate, but also if they need to consider using two complete systems.”
System configuration
Recker went on to say that available trailer or truck bed space is also a significant factor in most contractors’ purchase decisions. “With many mud mixing systems, contractors have limited mounting options because the power unit and the tank are built on a single skid,” he explained. “They may be able to fit two systems on one standard flatbed truck, but those same units will not fit within an enclosed truck or van-body. We addressed those limitations when developing the MX300 by making it modular and redesigning the shape of the tanks.”
The modular design of the MX300 will give you the ability to optimize the trailer or truck body’s space. The power unit mounts independently from the tanks for flexibility, and the narrow rectangular tanks take up less horizontal space than similar-sized systems. “It’s now much more convenient for contractors to fit multiple tanks or systems in an enclosed truck,” added Recker.
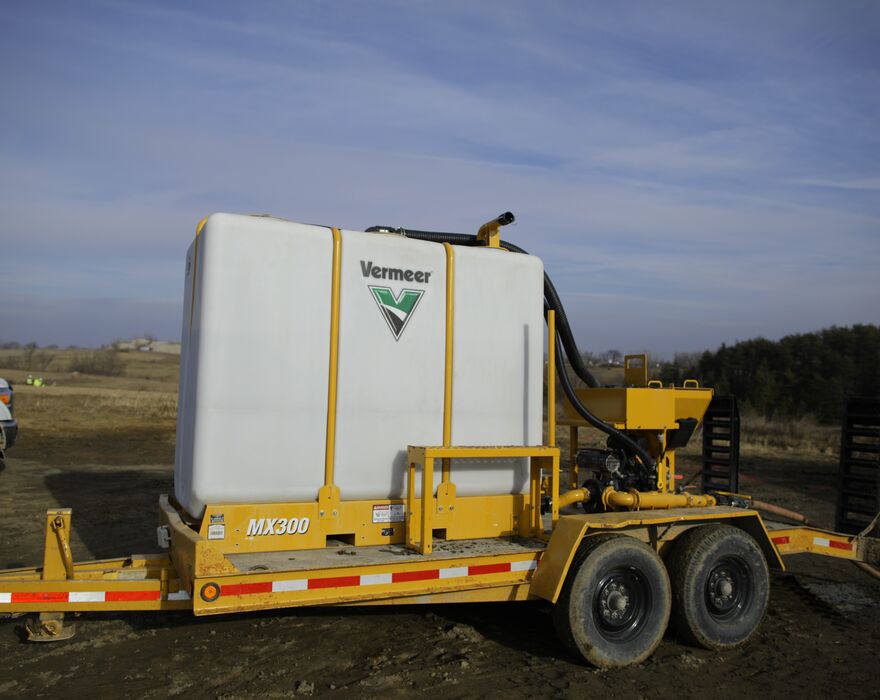
Gas or Diesel
Do you have other gasoline-powered equipment on your jobsite, or does all the other equipment run on diesel? You may gain efficiency by consolidating to a single fuel source.
Vermeer offers a choice of diesel or gas engine power on its MX300 mixing systems. One of the industry’s most widely used mixing system, the MX300 is available with a 23-hp (17.2-kW) Kohler ECH 730 EFI gasoline. The MX300D variant has a Caterpillar 3-cylinder 24.7-hp (18.4-kW) diesel engine.
Recker explained that a diesel-powered mud mixing system for directional drilling can help eliminate the need to keep gasoline on site. “Most equipment found on a typical HDD jobsite is powered by diesel engines,” he said. “While having a few extra gas cans on site is easy to do, crews appreciate the ability to use the same fuel type across their entire equipment fleet.”
Daily usage and serviceability
One last thing to consider when choosing a mud mixing system for directional drilling is daily ease of use, cleaning and serviceability. Details like the feed hopper design, fuel tank capacity and drain valve locations, along with access to replacement items like roll jets, make a difference in how happy your crew will be with a system long term. “It’s important for contractors to choose a system that is convenient to use and clean between jobs,” said Recker. “Bentonite-packed feed hoppers are an issue many crews face, which is why Vermeer mud mixing systems are outfitted with wide-mouth hoppers and suction hoses for the convenient pouring of drilling additives. Also, the fluid tanks on the MX300 have tapered bottoms to help prevent additives from settling and building up over time. It’s the small details that can help crews get more done every day.”
Mud mixing systems will continue to be an essential piece to getting the most from your equipment and crew. Make sure you take the time to choose the right system for your needs.
If you need more information about HDD fluid mixing systems, contact your local Vermeer dealer.
Vermeer Corporation reserves the right to make changes in product engineering, design and specifications; add improvements; or discontinue manufacturing or distribution at any time without notice or obligation. Equipment shown is for illustrative purposes only and may display optional accessories or components specific to their global region. Please contact your local Vermeer dealer for more information on machine specifications.
Vermeer and the Vermeer logo are trademarks of Vermeer Manufacturing Company in the U.S. and/or other countries. Kohler is a trademark of Kohler Co. Caterpillar is a trademark of Caterpillar, Inc. © 2022 Vermeer Corporation. All Rights Reserved.