If you want to maximize your output on large and complex horizontal directional drilling (HDD) projects, a proactive approach is best— because maxi HDD infrastructure projects often have aggressive time lines for completion. Caring for your equipment includes making sure you’re practicing good maintenance habits and planning for issues before they occur.
According to Vermeer Pipeline Solution Specialist Kelly Beller, preventive maintenance and proper drill operations go a long way in maximizing the life of maxi rig wear parts. “The most common cause of premature wear of parts and components is not addressing minor issues before they escalate.”
Beller said maxi crews need to pay attention to the following HDD maxi rig parts:
- Vise dies
- Sub saver
- Drill rod threads
- Sliding head shafts
- Gearbox slides
- Water swivel
Expanding on Beller’s advice, here are ways you can care for these wear parts.
Maxi rig vise dies
Your maxi rig’s vise is responsible for torquing and un-torquing every drill rod going into the ground. Gripping each connection are vise dies, or vise jaws as some in the HDD industry may refer to them. Vise dies start off with small edges, or teeth, to grip the drill rod when making or breaking a connection. Over time, those edges will wear down and can start to slip when torquing a connection. An improperly torqued connection can negatively impact your entire drilling operation because it can cause premature wear to other maxi rig parts.
So, your crew needs to keep an eye on the condition of the vice dies.
- What to look for: Before starting up for the day, inspect the shape of vise dies. If they are becoming dull and round, take the time to swap them out.
- What happens if you wait: If you let vise dies wear too long, rods may start to slip, potentially resulting in premature wear to the threads and your drill’s sub saver. Waiting too long can also make the task of swapping out dies more challenging because they will not slide away from the vise box as easily. And if the dies wear too, you can eventually damage vise boxes.
- Beller’s advice: “Keep your maxi rig’s vise dies clean of debris to get the most life out of them. When it is time to change them, consider investing in an extra set of vise boxes. Trying to slide worn-out dies away from the box on the job can be time consuming, but removing the boxes can be as efficient as spinning out a couple of bolts. So, many HDD maxi rig crews will swap out both components on the job. Then, they will swap out the dies on the removed vise boxes back at the shop.”
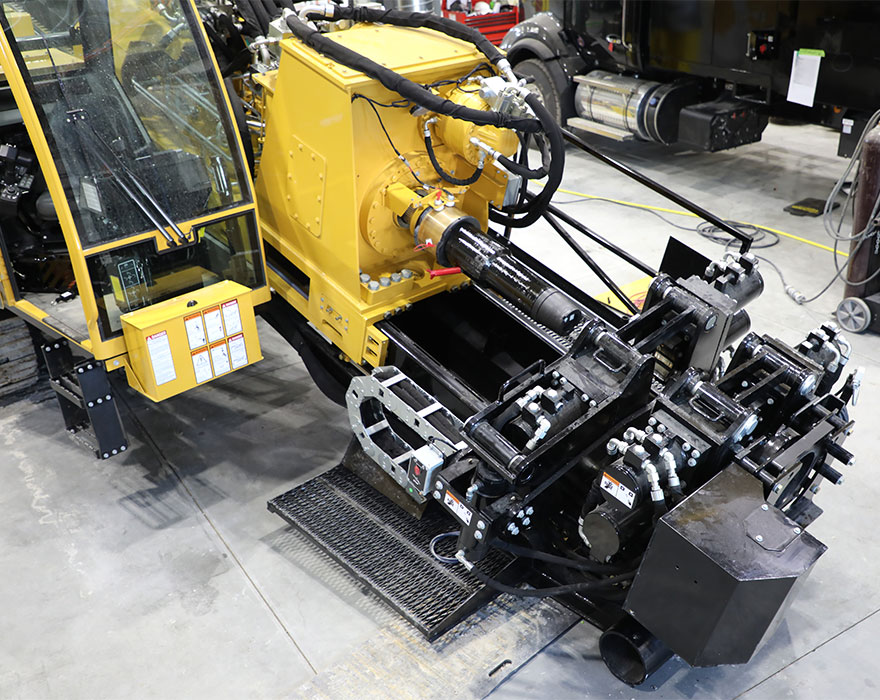
HDD maxi rig sub saver
It is also vital for your crew to keep your sub saver clean of debris to help prevent premature wear. However, excessive debris isn’t the only thing that can impact the operating life of a sub saver. Beller said improperly torqued rod joints, especially if you’re using a tail string, can also adversely affect the conditions of your sub saver. “Play in a few joints can cause damage back to the sub saver. It’s a chain reaction. A gap between the shoulders of one connection can cause excessive wear downhole and back to the sub saver. So, if a crew isn’t getting up to 200 hours of operations consistently from a sub saver, they should probably look for issues further down on the drill string,” he said.
Here is how you can determine when to replace the sub saver on your HDD maxi rig.
- What to look for: Jagged edges or rounded thread profiles indicate that it’s time to swap out sub savers. However, don’t just trust your eyes to determine the condition of threads. Instead, make sure your crew has a set of thread profile gauges. This will give them a more accurate visual of the sub saver’s condition.
You should also keep an eye on where the sub saver connects to the drill’s drive chuck. Any play in that joint indicates that your thread locking compound did not set up correctly. You may need to pull the sub saver off and start the process again if that happens. - What happens if you wait: Worn threads on an HDD maxi rig can potentially damage the threads on every piece of drill rod it interacts with. It can also lead to weaker joint connections up and down the drill string, which could cause a connection to fail downhole.
- Beller’s advice: “Crews should do their best to anticipate when it’s time to replace a sub saver by keeping on thread conditions during drilling operations. Since most thread-locking compounds require 12 hours of setup, swapping subs out at the end of the shift is best.”
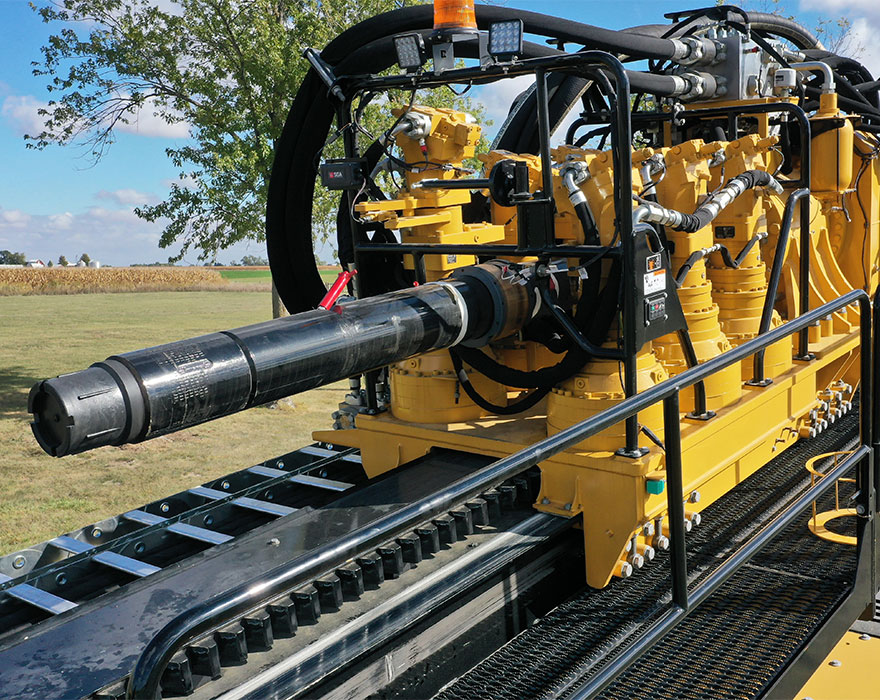
Maxi rig drill rod threads
The sub saver isn’t the only maxi rig part where thread conditions can impact your HDD operations. Your crews need to keep drill rod threads clean, covered when not in use and greased. Doing so will help crews get the maximum life out of their drill rods.
However, over time, threads will wear out, which can cause joint damage to other rods in the process. So, it’s important to recognize when it’s time to retire a drill rod.
- What to look for: Using a thread profile gauge, you can quickly determine the condition of your drill threads. Make sure no gaps exist between the gauge and the threads you’re testing. You should also look for any jagged edges or cracks in the metal.
- What happens if you wait: Threads that don’t tightly lock together may not maintain torque during operations. This excessive play within a joint can create a weak spot in your drill string and lead to a break downhole.
- Beller’s advice: “When removing a rod from the drill string, crews should use a steel brush to clean the threads and remove excessive grease. After that, new grease should be applied, and cap each end before placing it back on a rack or the ground.”
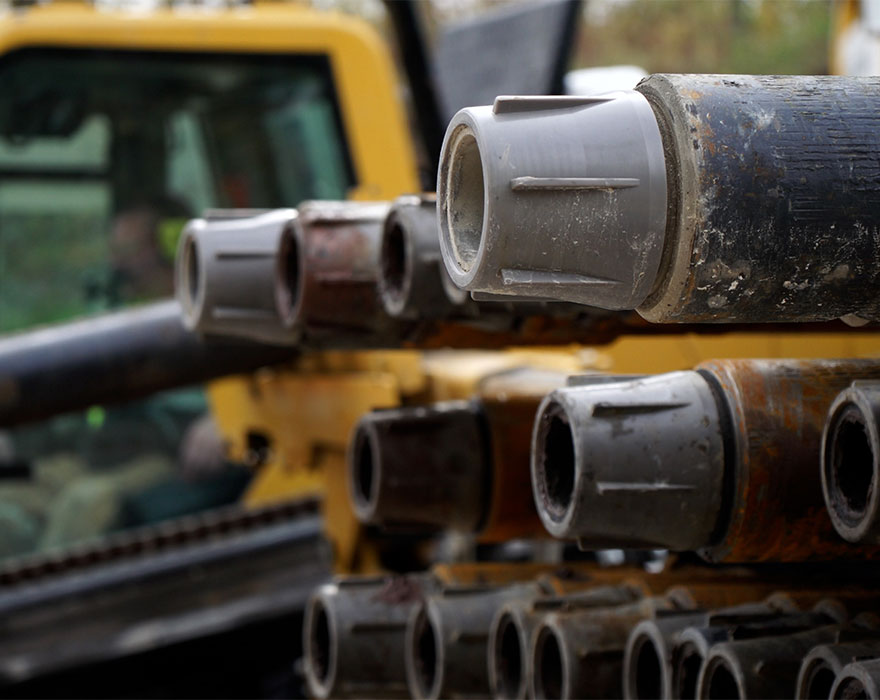
Maxi rig sliding head shaft
Some maxi rigs have a sliding head shaft with a full-travel vise. It is essential to keep this maxi rig part greased for optimal performance.
- What to look for: Without adequate grease, the sliding head shaft will start to stick during operations. Everything will feel a little choppy for the operator.
- What happens if you wait: Not regularly greasing the sliding head shaft on an HDD maxi rig can result in premature wear and impact joint alignment when adding drill rods.
- Beller’s advice: “Consult the machine’s maintenance manual for greasing intervals.”
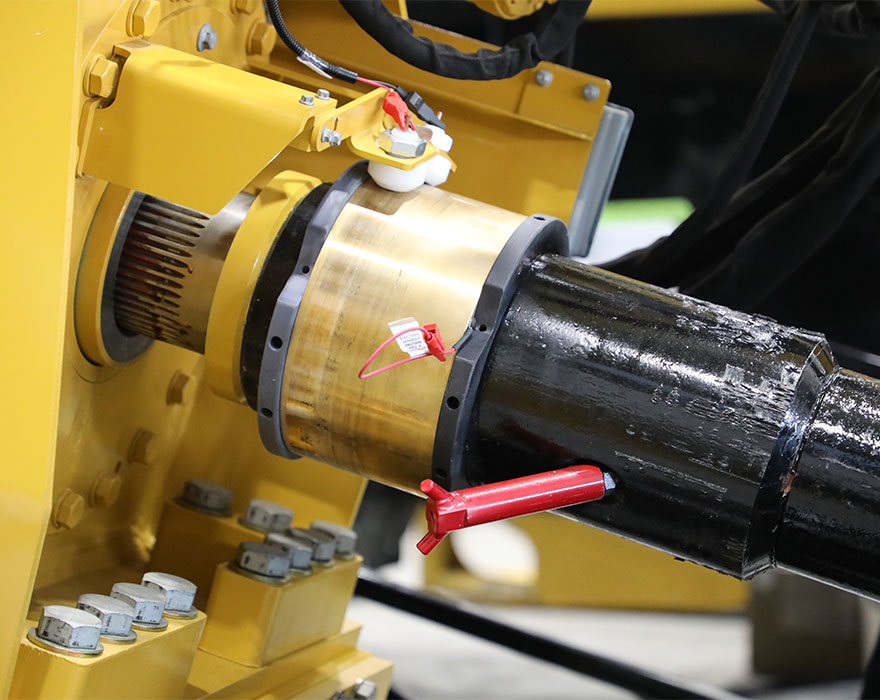
Maxi rig gearbox slide
Over time, the gearbox pads in contact with the rack will wear down and need replacement.
- What to look for: Regularly check the condition of the pads on the bottom side of the gearbox slide. If they are wearing thin, it’s time to replace them. The first set on a new drill can last up to 200 hours, depending on operating conditions. Future sets could last up to 400 hours. If you’re not getting that kind of life, rust or other debris sticking to the rack may be the cause.
- What happens if you wait: Not replacing pads leads to play in the carriage. The gearbox slide will not function smoothly coming down the rail, and pressures can rise when functionality gets sticky. Eventually, this can alter the alignment of your sub saver and drill rods when making a new connection. This can subsequently lead to thread damage.
- Beller’s advice: “Keep the slide clean and do not grease because it will attract dust and other materials to stick. Also, when the drill sits for a while, you should remove any rust with a steel brush or wire wheel before getting to work. That rust can contribute to prematurely eroding pads.”
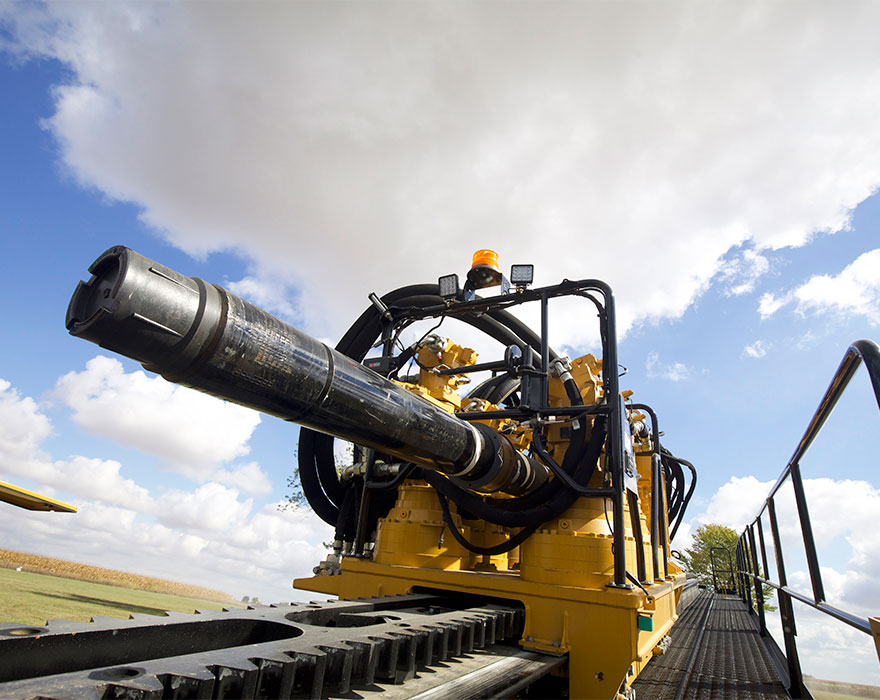
Water swivel on a maxi rig
The water swivel on the backend of the maxi rig is under constant pressure during drilling operations. To get the maximum performance from and optimize the life of this maxi rig part, you need to grease it approximately every eight hours of rotational operation. Grease helps to keep the internal packing glands in place to help prevent fluid leaks. There are also adjustment screws that can be repositioned if there are minor leaks, even after greasing.
- What to look for: Leaks are a sure sign that your water swivel is not functioning correctly. To troubleshoot the issue, start by giving the water swivel’s grease point two pumps of grease. You may need to tighten the packing gland if it’s still leaking. If that doesn’t fix the issue, it may be time to replace the water swivel packing gland.
- What happens if you wait: Drilling fluid leaks affect the cleanliness of a jobsite. And if a leak is left unchecked, it could lead to a major waterline blowout.
- Beller’s advice: “Assign a person to keep an eye out for leaks in the drill fluid system and be sure to address small leaks before they become major issues later on.”
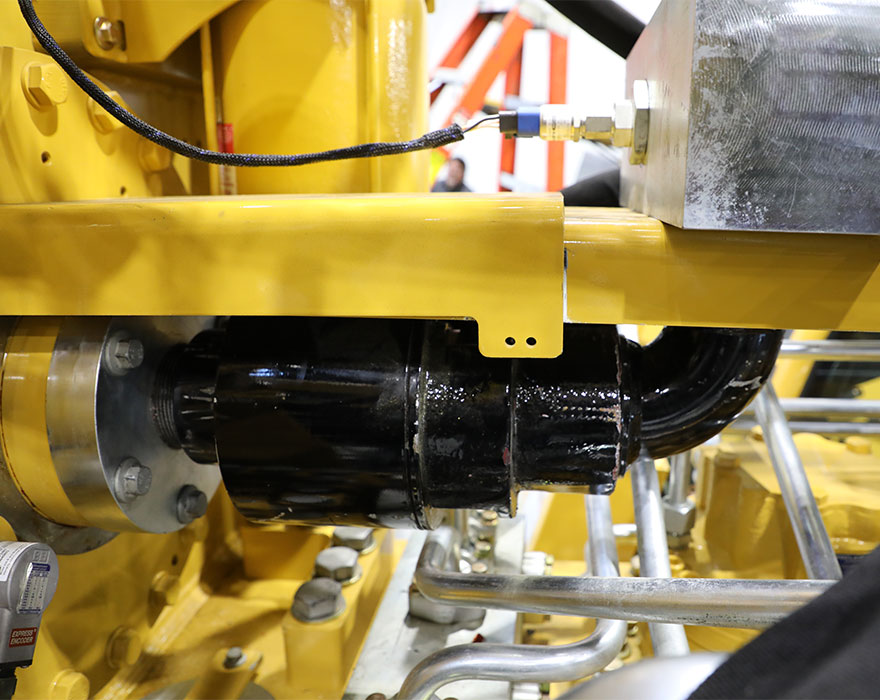
Follow good maintenance practices and keep a watchful eye
Vise dies, sub savers, drill pipe threads, sliding head shafts, gearbox slides and water swivels are six of the main maxi rig parts that need regular care to help minimize more significant machine issues down the road. Practice the advice outlined above and in your machine’s maintenance manual to help keep your HDD maxi rig crew productive. And if you have any additional questions about maintenance, be sure to contact your local Vermeer dealer.
Vermeer Corporation reserves the right to make changes in engineering, design and specifications; add improvements; or discontinue manufacturing at any time without notice or obligation. Equipment shown is for illustrative purposes only and may display optional accessories or components specific to their global region.
Please contact your local Vermeer dealer for more information on machine specifications. Vermeer and the Vermeer logo are trademarks of Vermeer Manufacturing Company in the U.S. and/or other countries. © 2023 Vermeer Corporation. All Rights Reserved.