Investing in the latest equipment technology and providing top-notch customer service gives Brookville, Ohio-based Ritter Company a competitive edge in the utility installation market. The company was an early adopter of horizontal directional drill (HDD) technology and continues to lead the way in utility installation.
Ritter specializes in HDD and pneumatic boring of water, gas and conduit lines, as well as sewer pipe utility installation and repair. They also offer hydrovac excavation and open trench services.
“When we got into underground utility installation many years ago, we focused on getting utilities in with minimal impact to the customer — minimal impact to the yards or parking lots,” said Phil Ritter, president of Ritter Company.
Experience and training deliver results
For over 70 years, Ritter Company specialized in underground utility installation, starting with trenching equipment. Philip Ritter Sr. started the company in 1950. It continues as a fourth-generation family-run business with Philip Ritter IV at the helm. With over 75 employees and decades of experience, Ritter Company has the capability to complete the most demanding utility installation jobs.
That experience is backed by a heavy investment in training. Every employee completes an extensive safety training program. Site-specific training is conducted before each assignment starts and employees receive continuing education throughout their career. Staff have been certified through the Board of Certified Safety Professionals as well as an OSHA-authorized 10/30 hour trainer.
This experience and emphasis on safety training helps keep Ritter Company on its A-game.
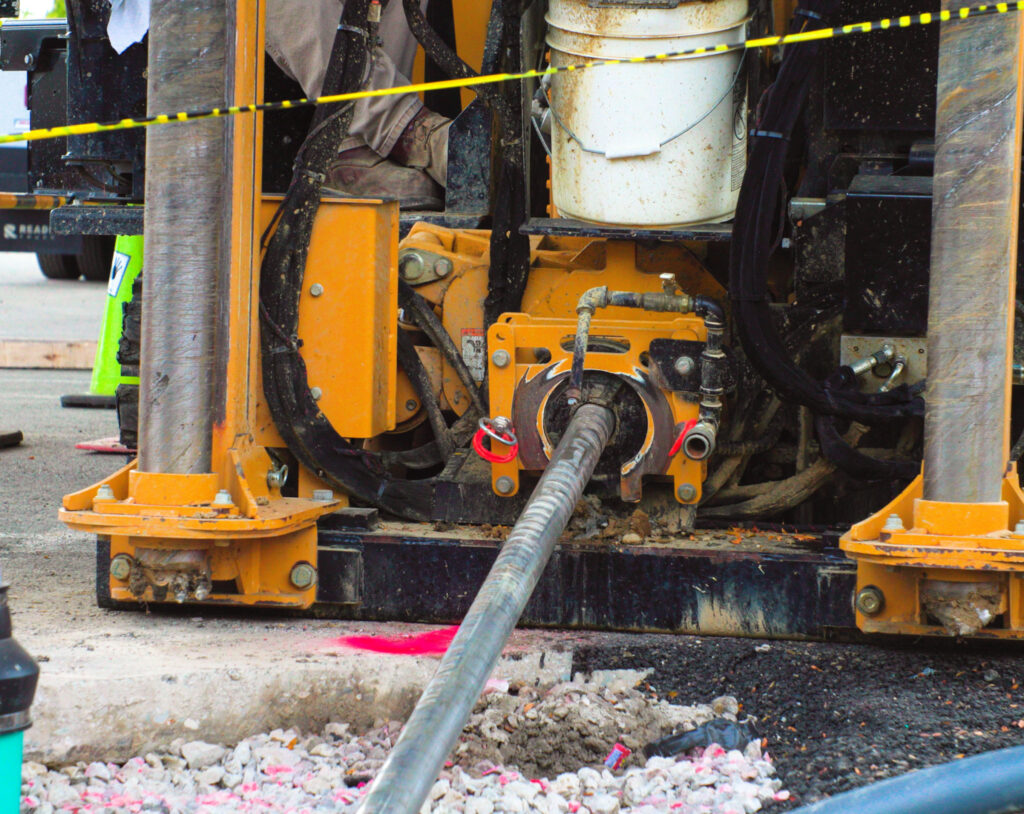
Technology helps Ritter Company do MORE
Ritter invests in the latest underground utility installation technology to drive efficiency and provide customers with the most advanced information, including as-built data.
“We always have the latest and greatest to take care of our customers. The biggest challenge is keeping up with technology. All of the new documentation requirements that we see, customers are always expecting more,” said Ritter.
To meet customer expectations, Ritter Company relies on Vermeer equipment. The company purchased its first Vermeer trencher in 1990. Ritter took note of emerging HDD technology while attending the International Construction & Utility Equipment Exposition (now known as The Utility Expo). This led to the company’s purchase of a Vermeer D24 Navigator® horizontal directional drill in 1994. Since then, the company has purchased 10 Vermeer HDD units, which played a critical role in the company’s continued expansion.
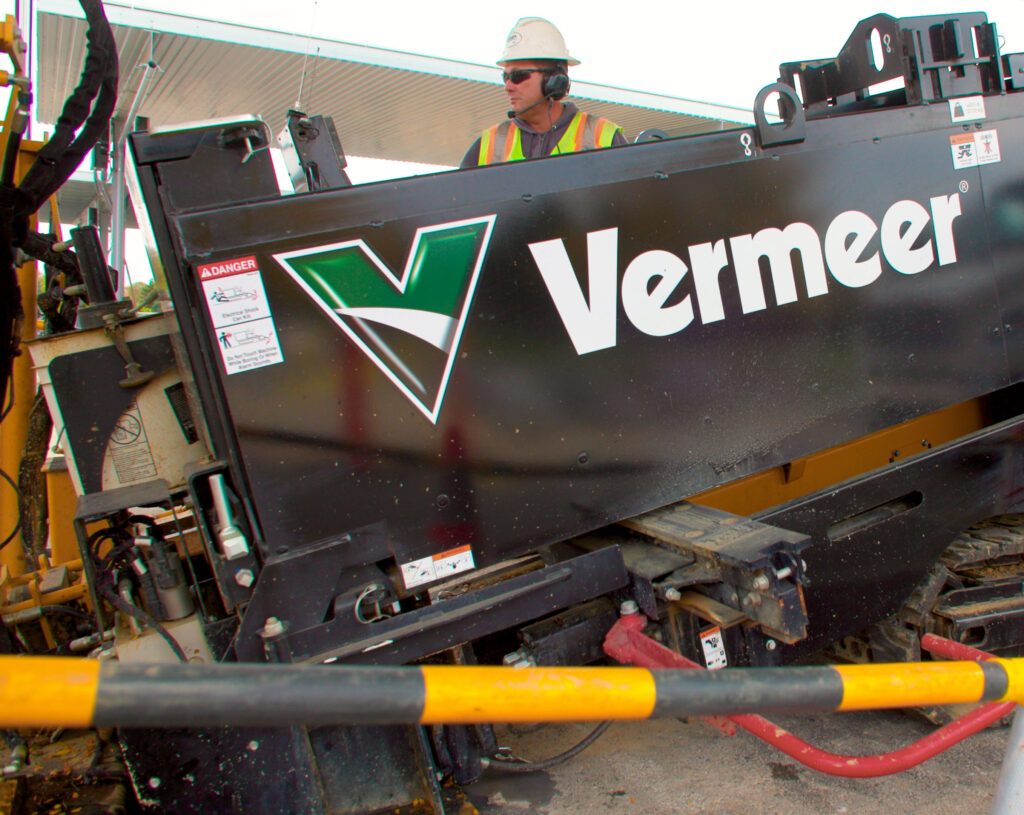
Ritter Company now has an extensive fleet of Vermeer equipment from a Vermeer D7x11 HDD up to a D40x55 HDD. This includes a D36x50 HDD and a few D24x40 HDDs. The company also uses a couple of Vermeer trailer-mounted vacuum excavators to locate utilities and for hydro excavation.
Increased reliability equals more productivity
Ritter Company has built a successful business by providing quality services and relying on dependable equipment to get more done efficiently and effectively.
“Vermeer offers more reliability. To me, reliability impacts productivity so much when you are talking about these kinds of machines,” said Ritter.
This reliability is enhanced with dealer service and support. Vermeer Heartland has helped Ritter Company meet the growing demand for utility installation through the years.
“I see Vermeer as a partner. The service department is always there to help us out. They have the parts there when we need them. The sales guys are right there alongside of us when we need them. Having a piece of equipment that holds up and gets the job done makes your day go so much better. With the service and the salesmen and the equipment, it’s all there and it’s all right,” said Ritter.
Ritter Company plans to continue to grow its business with the help of Vermeer Heartland. The company recently relied on the dealer’s expertise to expand into a new market, recycling wood waste into mulch. Ritter Company trusted Vermeer Heartland to provide the appropriate grinding equipment and training to diversify its business. The dealer is also a source of information to keep Ritter on the leading edge of HDD technology.
“We know Vermeer is going to be straight with us about what we need. We have a good thing with Vermeer and we don’t want to mess with it,” said Ritter.
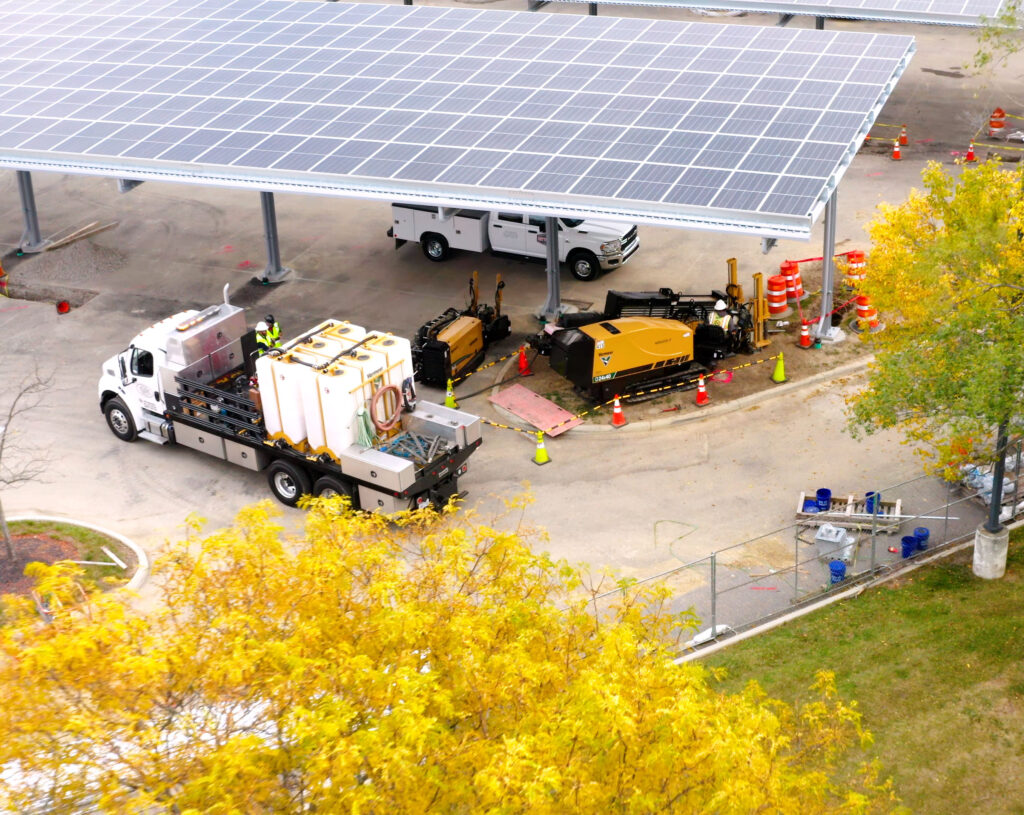
This article contains third-party observations, advice or experiences that do not necessarily reflect the opinions of Vermeer Corporation, its affiliates or its dealers. Testimonials and/or endorsements by customers in specific circumstances may not be representative of normal circumstances experienced by all customers.
Vermeer Corporation reserves the right to make changes in engineering, design and specifications; add improvements; or discontinue manufacturing at any time without notice or obligation. Equipment shown is for illustrative purposes only and may display optional accessories or components specific to their global region. Please contact your local Vermeer dealer for more information on machine specifications.
Vermeer and the Vermeer logo are trademarks of Vermeer Manufacturing Company in the U.S. and/or other countries. © 2023 Vermeer Corporation. All Rights Reserved.