When it comes to directional drilling in rock, operators often face numerous challenges. The hardness and unpredictability of rock formations require precise control and consistent power from the drill. Too much or too little force can lead to inefficient drilling, equipment damage and even project failure.
“Drilling inconsistent rock formations is where drill operators are really put to the test,” said Jeff Utter, product manager for Vermeer. “Maintaining a slow, steady pace requires constant adjustments to avoid stalling the drill string. Whether using an automatic mode or drilling manually, the objective is to maintain the maximum allowable weight on the bit while preventing frequent rotational stalls.”
Most horizontal directional drill (HDD) rigs struggle with this balance of power and control, often leading to overcompensation by the operator and inconsistent drilling performance.
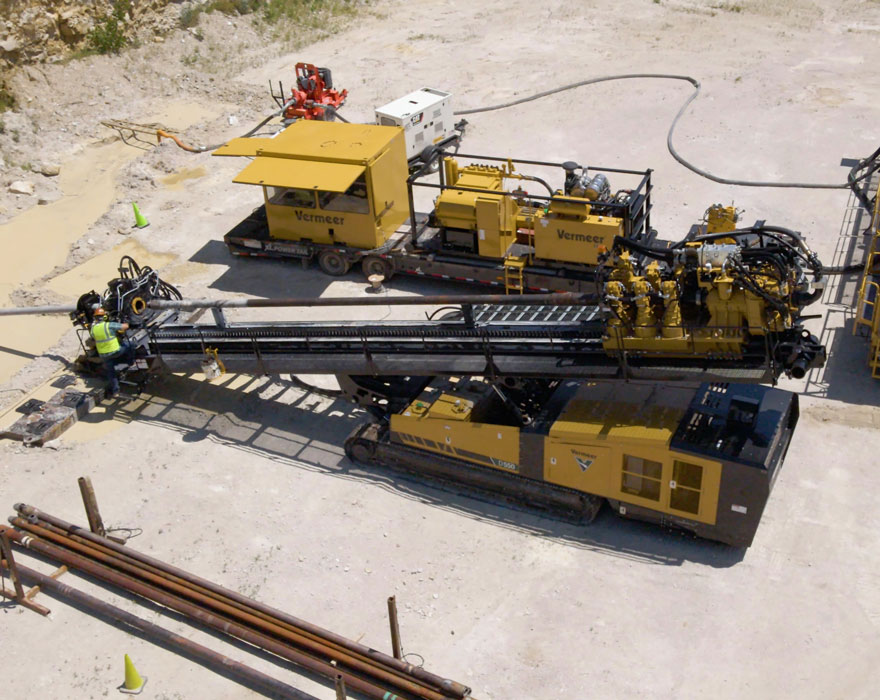
Control is key for directional drilling in rock
Ultra-slow speed control technology fundamentally changes the way HDD operators approach drilling in rock. The technology allows for precise control over the drill’s thrust, optimizing the cutting action for challenging rock bore conditions.
“It’s not necessarily about slow speed; it’s really about controllability,” explained Utter. “Slow speed often lends to controllability. Feathering the thrust manually doesn’t always allow the operator to maintain a consistent weight on the bit. This technology is not about making the drill slower but rather about giving the operator more control over the drilling process. It’s the ability to adjust the speed and power of the drill in order to maintain a constant weight on the drill bit, allowing optimal cutting performance and efficient drilling.”
The Vermeer D550 horizontal directional drill is one of the first HDD rigs to implement ultra-slow speed control technology. It is designed to deliver optimal operational and service experience for contractors.
“With 100,000 ft-lb (135,581.8 Nm) of torque, operators can go from the pilot bore to a larger reamer, reducing the number of passes made on a bore,” said Ed Cutler, Vermeer senior project engineer for pipeline equipment. “The D550’s ultra-slow speed technology delivers precise thrust control, allowing operators to regulate weight-on-bit pressure for optimal cutting action and maximum tooling life.”
The D550 HDD is equipped with smart onboard technology that gives drill operators and service technicians access to important diagnostic information. This allows for real-time adjustments to drilling parameters.
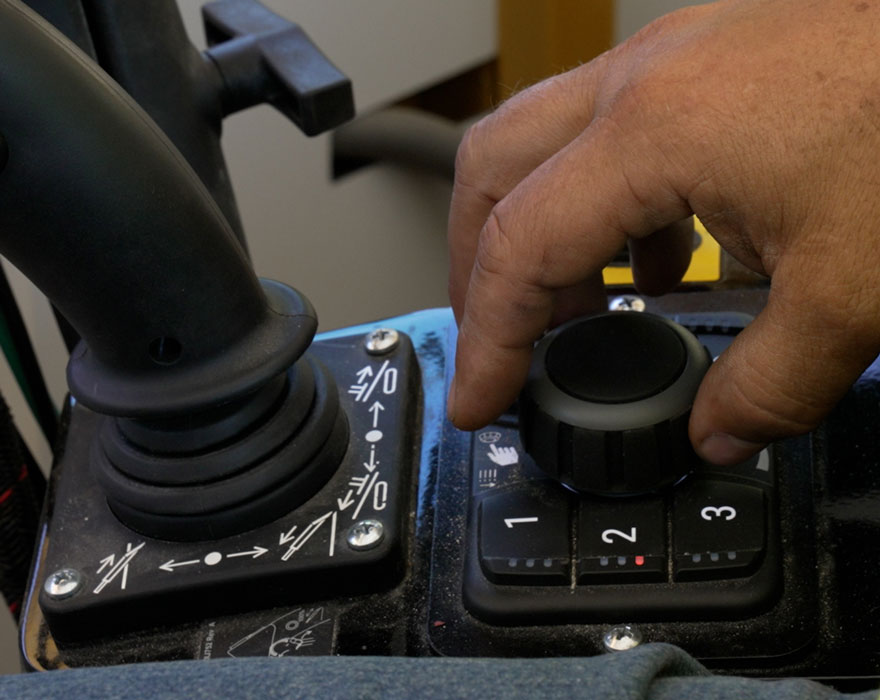
Benefits of ultra-slow speed control
The introduction of ultra-slow speed control technology in the Vermeer D550 HDD has several benefits for contractors using directional drilling in rock.
1. Enhanced operator control: Ultra-slow speed control technology also enhances operator control. With this technology, the operator can better manage the balance between power and control, leading to more efficient drilling. This enhanced control allows the operator to push the drill closer to its limits while limiting the risk of stalling, helping lead to more efficient and productive drilling.
2. Reduction in equipment stalls: One of the most significant benefits of ultra-slow speed control is the reduction in equipment stalls.
“The ultimate thing that we’re trying to avoid is stalling the machine out,” said Utter. “Once an operator stalls the drill, they have to then take control from the automatic drilling system to reengage it and get the machine running smoothly again. That’s all, of course, lost production while the machine is stalled and subsequently reengaging the rock face.”
With ultra-slow speed control, the drill is able to maintain a consistent pace, minimizing the likelihood of a stall. This helps optimize productivity on the jobsite.
3. Maximize tooling life: Another benefit of ultra-slow speed control is it can help operators extend the life of drill tooling.
“There are certain amounts of weight an operator can put on the tooling. Without slow speed control, the drill operator may try to put too much thrust on the tooling that is rotating downhole,” explained Cutler. “That can lead to excessive wear and shortening the life of reamers and rock bits. With optimal control, tooling can last a long time.”
By maintaining a consistent weight on the bit, the drill is able to optimize the cutting action, minimizing wear and tear on the tooling and extending its life.
Enhancing rock drilling
Ultra-slow speed control is an innovative technology that can enhance the process of directional drilling in rock. By providing precise control over the drill’s thrust, this technology allows for optimal cutting action, minimized equipment stalls, improved tooling life and enhanced operator control.
The Vermeer D550 HDD is at the forefront of this technology, providing contractors with a powerful and efficient tool for directional drilling in rock. As this technology continues to evolve and be implemented in more HDD rigs, the industry can look forward to even more efficient and productive drilling operations.
If you want to learn more about the Vermeer D550 HDD and how it can help you with productive directional drilling in rock, contact your local Vermeer dealer.
Vermeer Corporation reserves the right to make changes in engineering, design and specifications; add improvements; or discontinue manufacturing at any time without notice or obligation. Equipment shown is for illustrative purposes only and may display optional accessories or components specific to their global region. Please contact your local Vermeer dealer for more information on machine specifications.
Vermeer and the Vermeer logo are trademarks of Vermeer Manufacturing Company in the U.S. and/or other countries. © 2023 Vermeer Corporation. All Rights Reserved.