Are you using the right reamer when drilling in reactive ground conditions such as sticky clay or sandy loam?
Fluted or packing reamers will work in self-supporting soils with the right fluid mix, additives and drilling techniques, but the better option to consider would be mixing reamers. In reactive soil such as sticky clay, mixing-style reamers create a more manageable slurry and prevent mud from balling up in the hole. They mix cuttings with drilling fluid to help you create a stable hole that meets the required product installation size. While drilling, slurry created by these mixing reamers needs to consistently flow out the borehole.
“You want cuttings thoroughly hydrated and mixed. Ideally, the slurry you see coming out of the bore path created by the reamer would be the consistency of a smooth milkshake,” said Jeremy Knepper, design engineer at Vermeer.
Controlling the amount and placement of the drilling fluid affects slurry quality and the resulting horizontal directional drill (HDD) production and bore quality when drilling in reactive ground conditions.
Vermeer Mix MasterTM HD (MXHD) reamers take the previous Mix Master reamer design a step forward in fluid management. Their unique design directs fluid where you need it — to the cutting teeth. Directional fluid control hydrates the bore path and cutting teeth while maintaining bore integrity. Spray bars located on the plates of mid-size and larger MXHD reamers directly hydrate the path of the plate spinning next to it.
“We really want to make sure the surface is being hydrated as it is being cut,” said Knepper.
Fluid where you need it with hydro distribution
The hydro distribution (HD) design is unique to Vermeer MXHD reamers. It minimizes the risk you will outrun the mud created during the reaming process when drilling in reactive ground conditions.
The number of fluid distribution ports on the spray bars scales with the plate size. Larger plates feature spray bars with more fluid ports for greater fluid distribution. “One of the key benefits of this design is it brings the fluid ports much closer to the cutting teeth, regardless of the cut size. When fluid is just coming out of the reamer shaft, it may not always get to the cutting teeth where you need it,” said Knepper.
A common issue with mixing reamers is mud packing around the plates — the reamer gets balled up. MXHD reamers address this challenge by providing fluid distribution throughout the bore to minimize areas where mud can build up on the plates.
On mid-size and larger reamers, the direction of the fluid distribution relative to the bore path makes a difference when drilling in reactive ground conditions. If the fluid is directed perpendicular to the reamer shaft’s axis of rotation, it has the potential to wash out your bore, especially when drilling in sandy loam ground conditions. With the MXHD, the fluid is directed to hydrate the bore path as the teeth cut it.
The intentional spray pattern design hydrates cuttings taken off the bore wall to give you an ideal slurry mix, which aids in the management of the cuttings.
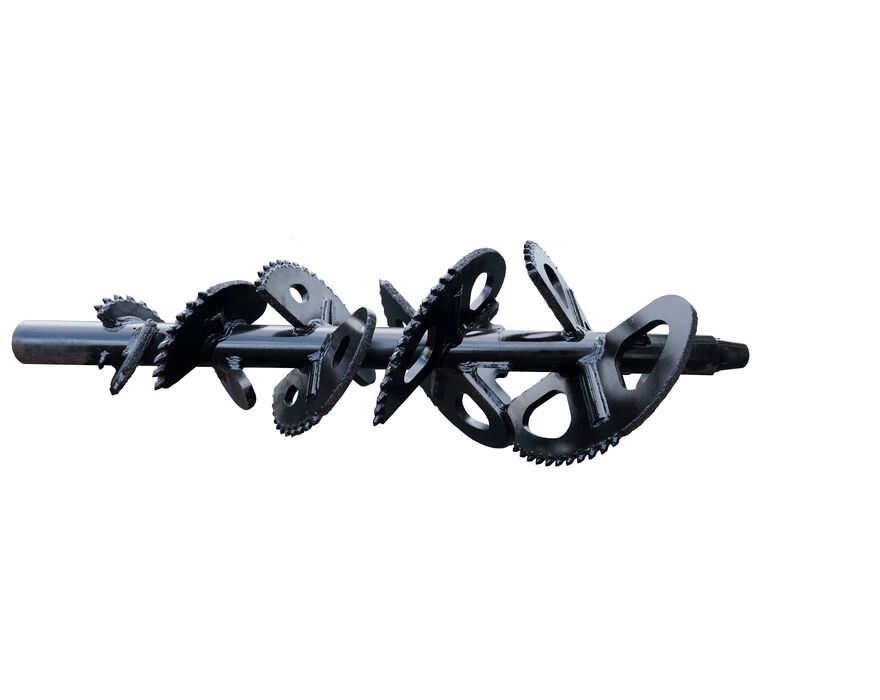
Keep the slurry moving
Plate openings on mid-size and larger MXHD reamers combined with the optimized angle of the plates promote slurry flow and help move cuttings behind the reamer. Openings in the plates have been purposely sized to balance slurry pass-through and durability.
“The angle of the plates helps push cuttings toward the backside of the reamer, similar to an auger,” said Knepper.
Maintain accuracy when drilling in reactive ground conditions
Tooth selection and the geometry of a reamer can affect the accuracy of your bore path and shape when drilling in reactive ground conditions.
The Vermeer Mix Master HD reamer uses small rotary teeth to minimize overcut and maintain bore wall integrity. The teeth are strategically mounted to the plates to form an intentional spiral tooth pattern. The efficient mixing action and circular spiral tooth pattern help you produce smoother pullback and a cleaner cut. This updated geometry also helps minimize wandering while cutting a more accurate bore path.
An efficient progressive plate design steps the hole up to the full diameter. The initial plates increase the hole diameter in 4-in (10-cm) increments while the final plates finish cutting the hole in 2-in (5-cm) increments.
These enhancements help make the MXHD durable, accurate and productive. To accommodate a variety of product installations from utility through pipeline, Vermeer MXHD reamers are available in a variety of threaded shaft sizes and 6-in to 36-in (15.2-cm to 91.4-cm) cut diameters.
Contact your local Vermeer dealer to discuss whether the MXHD reamer is right for you.
Vermeer Corporation reserves the right to make changes in product engineering, design and specifications; add improvements; or discontinue manufacturing or distribution at any time without notice or obligation. Equipment shown is for illustrative purposes only and may display optional accessories or components specific to their global region. Please contact your local Vermeer dealer for more information on machine specifications.
Vermeer, the Vermeer logo and Mix Master are trademarks of Vermeer Manufacturing Company in the U.S. and/or other countries. © 2023 Vermeer Corporation. All Rights Reserved.