Do you have a comprehensive mud management plan? Creating one could help you more accurately estimate projects while keeping crews productive on jobs.
Large-diameter horizontal directional drill (HDD) bores often require large quantities of drilling fluid. A drilling fluid management plan can help you understand how you’ll manage it for a successful project.
“The drilling fluid is the bloodline of HDD. Without a good mud management program in place, it can reduce the rate of success,” said Marv Klein, solution specialist at Vermeer Corporation. “If you don’t have the right mud mixture or you are not pumping the right volume, everything can come to a halt pretty quickly.”
Commit to a written plan
It’s not uncommon for engineering companies or clients to ask for a pre-planned mud management program. It shows them your crew understands the proper drilling fluid management protocols for the project.
With larger drills and maxi rigs — those 100,000 lb (444.8 kN) thrust and above — managing the significant volume of mud is a distinct challenge. Long-distance or large-diameter bores deal with a significant volume of mud. Effectively managing these fluids in a cost-efficient manner is essential for success.
A drilling fluid management plan can also help mitigate the risk of inadvertent returns. Inadvertent returns can occur unexpectedly in any unknown location along the bore path. Having a good contingency and mitigation plan can help address this potential issue.
Consider your options
An effective game plan to manage drilling fluid can significantly influence overall project cost. A well-designed drilling fluid management plan can reduce fresh water and additive needs while minimizing disposal expenses. Conversely, when the mud is merely suctioned up and transported offsite, costs can escalate rapidly.
“It is not just the dumping fees, you have transportation, you have fuel cost, you’re paying a truck driver to haul up and down the road, back and forth from the jobsite to the disposal site. Those costs all factor in,” said Klein.
Vermeer reclaimers offer a solution. A reclaimer can be cost-effective because it allows for the retention and reuse of drilling fluid. You don’t have the added costs of continually mixing mud and hauling it off. There are certain parts of the country where standards for dumping sites are stricter — potentially limiting your disposal options.
“If you can use reclaimers and retain 70% to 80% of the drilling fluid that is being pumped down the hole and reuse 90% to 100% of that recycled fluid, you’ve reduced those dumping costs dramatically,” said Klein.
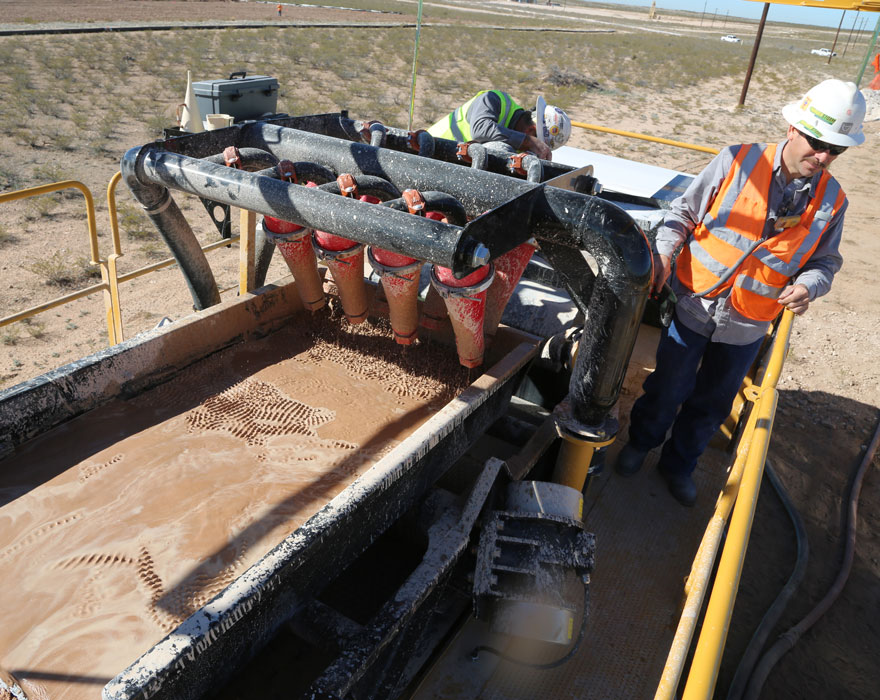
Drilling fluid management takes on a more significant role when using bigger drills to install larger diameter products due to the higher volume of drilling fluid being pumped. In urban environments and other tight jobsites, a reclaimer can play a key role in mud management by minimizing the need for fresh water, the cost to transport fresh water, the need to transport dirty fluid and the disposal cost.
Utilizing a reclaimer on the entry side of the bore can help minimize the need to haul in fresh water and the use of mixing fluid additives. This setup requires a relatively small footprint.
The bigger challenge arises in managing fluid on the exit side of the bore. When back reaming with high volumes of drilling fluid, that fluid must be controlled on the exit side. In some large-diameter projects with ample space, reclaimers may be set up on the exit side to recycle the fluid and bring it back to the drill.
However, in urban areas there may not be room for a reclaimer on the exit side of the borehole and shuttling the fluid from the exit pit to the entry side can prove challenging.
“The utilization of large vac trucks to transfer fluid is a very common practice. However, in some cases due to the high volume of fluid being pumped down the borehole on the entry side, it may be challenging for vac trucks to keep up when transferring mud from the exit side,” said Klein. “In this case, the drill may sit waiting for more mud to be transferred back to the entry side.”
Identifying these challenges and developing a plan before the work begins can improve your project results. Consult your Vermeer dealer to help resolve challenges when developing your next drilling fluid management plan.
Vermeer Corporation reserves the right to make changes in engineering, design and specifications; add improvements; or discontinue manufacturing at any time without notice or obligation. Equipment shown is for illustrative purposes only and may display optional accessories or components specific to their global region.
Please contact your local Vermeer dealer for more information on machine specifications.
Vermeer and the Vermeer logo are trademarks of Vermeer Manufacturing Company in the U.S. and/or other countries.
© 2024 Vermeer Corporation. All Rights Reserved.