Fluid management on your horizontal directional drill (HDD) jobsite can make or break your crew’s productivity. Not having the correct mixture or volume, along with an efficient disposal plan can significantly impact how many feet per day your crew installs.
John Cope, an applications engineer at Vermeer, sat down with Trenchless Technology magazine to discuss the importance of proper fluid management on an HDD jobsite. Cope started at Vermeer in 2013 developing new reclaimers and high-pressure mud pump models. Along with developing prototypes, Cope helps train Vermeer dealerships and customers on using their equipment to maximize efficiency and productivity on the jobsite.
Why is efficient fluid management essential on an HDD site?
When discussing fluid management on an HDD jobsite, fluid management includes recycling drill fluids, transporting fluids from different jobsites and disposing of spoils.
The purpose of the drill fluid is to cool the drill bit, keep the bore path clear by removing the suspending cuttings and add a filter cake for a layer for filtration. Without the correct fluid mixes or fluid management plan, your crew could experience inadvertent returns — which can be costly. You may also experience slower penetration rates or a collapsed bore path, increasing the price per foot.
Cope explained, “Many people in the industry consider the drilling fluid the lifeblood of the HDD jobsite. With improper fluid mixture or management, the jobsite can become very inefficient, and you will likely experience challenges with installing your product.”
Cope suggests being proactive with your fluid management plans rather than reactive. To do this, ask yourself a few questions to develop a plan before stepping foot on your jobsite:
- What is the fluid volume?
- What are the soil conditions?
- What is the contingency plan for inadvertent returns?
- How will I transport fluid from one end of the bore path to the other?
- How will I manage the fluid while working onsite?
- How will I dispose of the spoils once the job is complete?
If you can create a detailed contingency plan, you can become better prepared for any changes or adjustments that may occur.
Changes in the HDD industry
Throughout Cope’s career, he has seen the productivity demands for equipment increase dramatically. As drills have gotten more robust — from thrust capabilities ranging from 7,850 lb to 1,360,000 lb (3,560.7 kg to 616,885.6 kg) — fluid management equipment needs to change as well. For example, reclaimer performance has increased from 400 gpm to 800 gpm (1,818.4 L/min to 3,636.8 L/min) and larger pipeline reclaimers like the R600T producing a final process rate of 1,200 gpm (4,542.5 L/min) and a recycling rate of 600 gpm (2,271.2 L/min).
Another change Cope has seen is the increased regulations in the HDD industry. With more concerns on the environmental impact of HDD and dumping drilling fluids, there are more regulations and restrictions HDD contractors need to navigate to complete their jobs. These regulations — along with bigger jobs and increased productivity expectations — are some of the reasons why effective fluid management is critical.
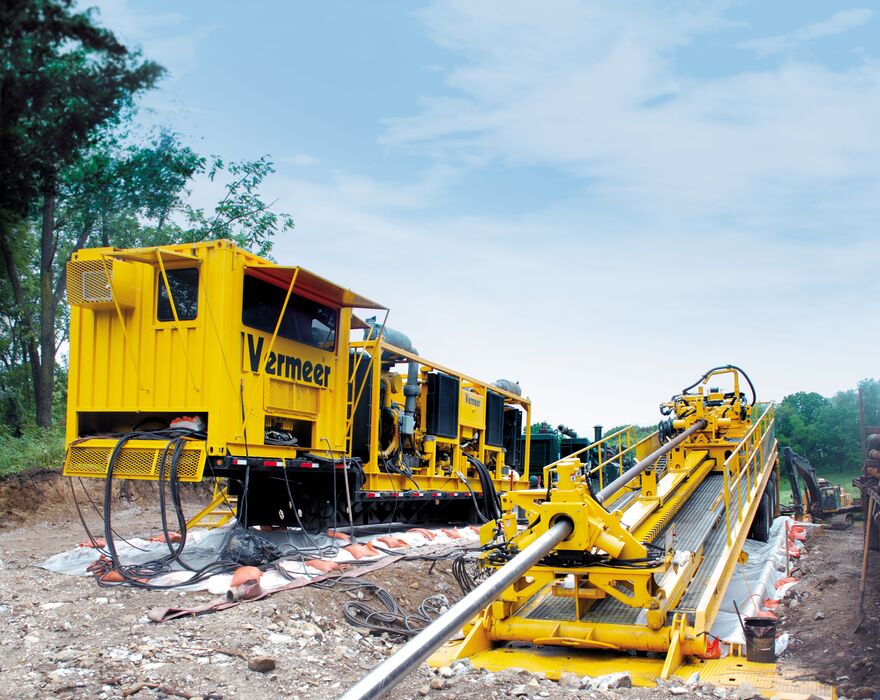
Role of a reclaimer on a jobsite
A reclaimer, sometimes referred to as a recycler, is used in conjunction with a high-pressure mud pump and mix system. A reclaimer allows you to recycle and reutilize fluid multiple times on the jobsite. By doing this, you can save water and only dispose of the fluid that is unusable.
The first step to this process is adding the bentonite, polymers or whatever ingredients your fluid mixture is required based on soil conditions into your reclaimer. This mixture will then be sent to the high-pressure mud pump. The mud pump will be used down on the drill string, which then creates cuttings. After the cuttings are created a pit pump will collect the cuttings to then be transported to the scalping shaker. The scalping shaker will remove the larger solids in the fluid mixture — rocks, roots, mud or large sand grains.
Depending on the size of your drill and jobsite, you will either have a two-stage or three-stage reclaimer system. For the small or medium-sized drills, it is a two-stage system with a scalper shaker and desilter. For larger drills, the three-stage system includes desilters, scalper shakers and desanders. This multi-stage system, along with hydrocyclones, separates the larger particles from usable drilling fluid.
When using a reclaimer, you typically want to recycle fluid at least two times. For example, if you want to recycle 400 gpm (1,818.4 L/min), you need to process at least 800 gpm (3,636.8 L/min).
New R125 reclaimer to support utility work
Vermeer has recently launched the newest addition to the fluid management lineup — the R125 reclaimer.
The R125 was designed for smaller utility crews working with a range of drills from the D24 up to the D40x55.
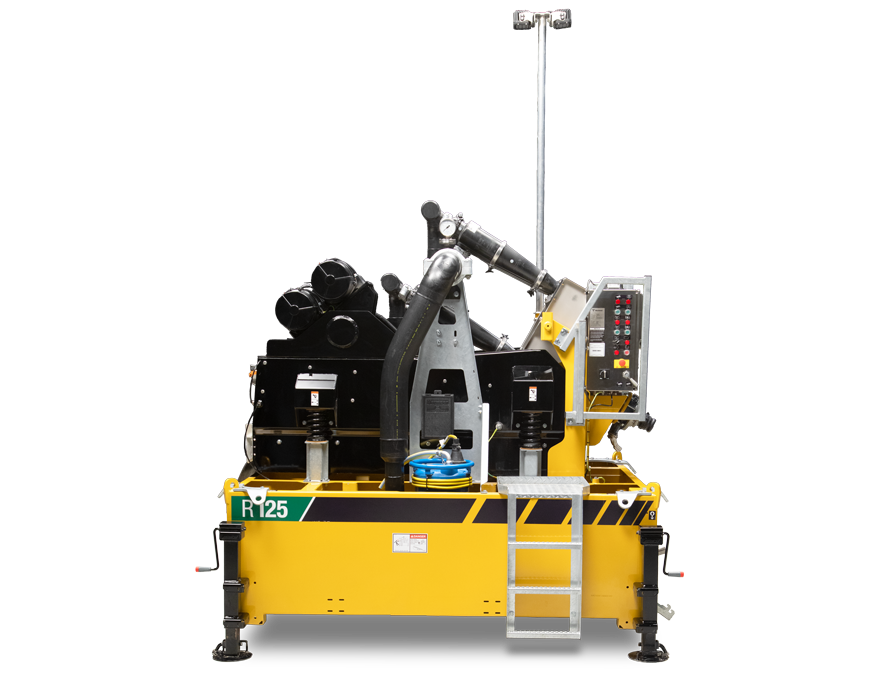
For smaller utility crews, it may not be clear when a reclaimer is needed onsite. Some questions you may want to ask to determine if you need a reclaimer are:
- How far away is your water source?
- Will there be harder ground conditioners, where penetration rate might be slow?
- What is the volume of drilling fluid being used per day?
- How far away is your disposal site?
Cope’s pro tip: “When you answer those questions and find that your crews are often waiting for water or fluid to complete their task at hand, that could be an opportunity for a reclaimer to help reduce downtime on the jobsite.”
Cope explained that if you are working in rural areas where a water source maybe be 30 minutes or more away, having a reclaimer onsite becomes very efficient. When traveling to get water, then fill your tank, and drive back — that time adds up for crews to not be actively drilling. Much of this decision will simply fall to the jobsite logistics and water access and how quickly and consistently you need your crews to keep drilling.
For more information on fluid management equipment or other support equipment for your utility jobsite, get in touch with your local Vermeer dealer.
Vermeer Corporation reserves the right to make changes in engineering, design and specifications; add improvements; or discontinue manufacturing at any time without notice or obligation.
Equipment shown is for illustrative purposes only and may display optional accessories or components specific to their global region. Please contact your local Vermeer dealer for more information on machine specifications.
Vermeer, the Vermeer logo and Equipped to Do More are trademarks of Vermeer Manufacturing Company in the U.S. and/or other countries.
© 2025 Vermeer Corporation. All Rights Reserved.