As the underground utility space becomes increasingly crowded, bore planning takes on a pivotal role in the safety and efficiency of drilling operations. With the growing congestion of right-of-ways and the trend of utilities moving from aerial to underground placement, the risk of utility strikes during drilling has increased. Proper bore planning is essential to help avoid these incidents.
Importance of bore planning
Bore planning involves thoroughly mapping out the proposed drilling path, taking into account the location of existing utilities, the required clearances, and the specific characteristics of the horizontal directional drill (HDD) and the product being installed. By carefully planning the bore ahead of time, contractors can avoid potential conflicts with existing infrastructure and help ensure a smooth installation process.
Municipalities are increasingly requiring detailed bore plans before approving projects, and many expect as-built records after completion. Failure to provide this documentation may jeopardize future work opportunities. However, beyond just meeting requirements, effective bore planning is simply good practice.
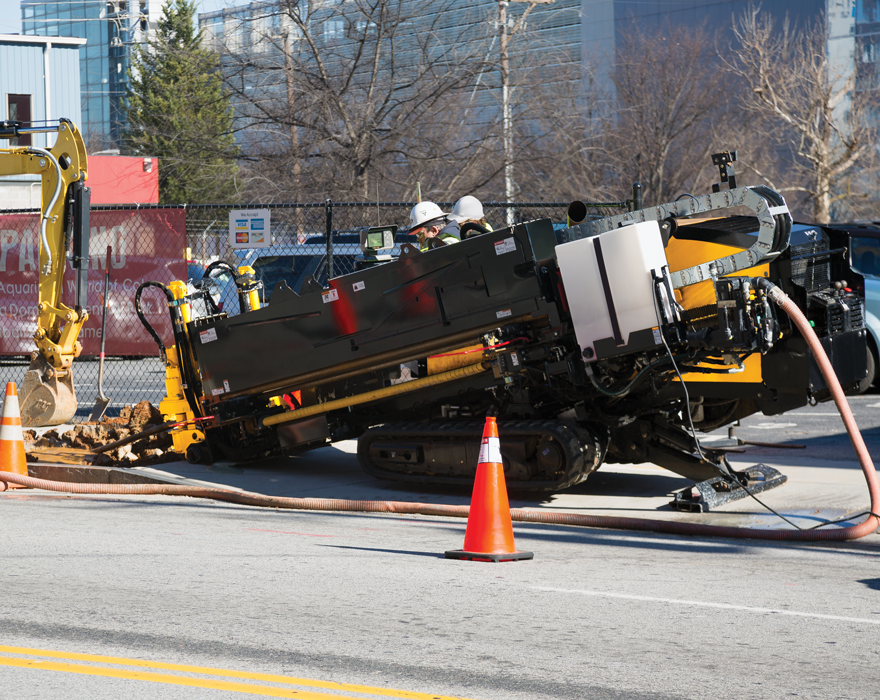
Key considerations in bore planning
One of the most critical aspects of bore planning is knowing exactly where the drill will enter and exit the ground, as well as the entry angle and setback distance needed to reach the required depth. The depth of the bore path must account for not only the diameter of the product being installed but also the bend radius of the drill rods.
Maintaining proper clearance from existing utilities is paramount. Many municipalities have established minimum clearance requirements that must be adhered to.
Another crucial consideration is the pullback process. The bore plan must account for the size of the reamer, existing utility crossings and the product being installed. Failing to provide sufficient clearance can result in the product getting stuck or damaged during pullback.
Traditional vs. digital bore planning methods
Traditionally, bore planning has involved manually sketching out the proposed drill path based on visual surveys of the site and available utility maps. While this method can be effective for simple projects, it becomes more challenging as the project’s complexity increases.
Digital bore planning tools have emerged as a powerful alternative. Solutions like the Vermeer BorePlan mobile app allow contractors to map out the bore path using GPS data and other digital information sources. The resulting plans are usually more accurate, detailed and easily shareable with project stakeholders.
Digital bore planning tools can also integrate data on the specific drill rig being used, the product being installed and required clearances from existing utilities. This contributes to the feasibility of the planned bore in the field. Real-time updates between the office and field via cloud connectivity maintains constant communication, keeping everyone on the same page as the project progresses.
Furthermore, digital bore planning offers significant advantages over manual methods in terms of speed and accuracy. A skilled technician using a bore planner tool with an integrated GPS receiver can map out a bore in roughly the same amount of time it takes the crew to set up the drill rig and mixing system. Revisions and adjustments to the plan can be made, and the tool will provide instant feedback on clearances and bend radius limitations.
On the other hand, manual sketching is far more time-consuming and can be subject to errors and oversights. Depending solely on visually inspecting the jobsite and using available utility maps leaves significant room for potentially severe miscalculations.
Value of as-built documentation
Beyond the efficiency and accuracy advantages, one of the greatest benefits of digital bore planning is the permanent record it provides. As-built data can be seamlessly captured while executing the bore, providing an indisputable record of where the product was installed. This documentation is invaluable for facilitating future work in the same area.
Accounting for utilities
Correctly identifying and revealing existing utilities along the proposed drill path is a vital part of bore planning, regardless of whether traditional or digital bore planning methods are employed. Crews should use a vacuum excavator for this task, as it causes minimal ground disturbance and carefully removes soil around the utilities.
Another emerging best practice is to install a tracer wire with the product during the initial installation. This allows future contractors to locate the utility by connecting to the tracer wire without the need for extensive potholing or excavation.
Overcoming resistance to adoption
Despite the clear advantages of digital bore planning, some contractors have been hesitant to adopt the technology. Reasons include the learning curve associated with new software, reluctance to change entrenched processes and a belief that traditional methods are sufficient.
However, as project owners and municipalities increasingly mandate the use of digital bore plans and as-builts, contractors who are not on board will find themselves at a severe competitive disadvantage. The technology has matured to the point where it is user-friendly and can integrate seamlessly with existing business processes. With the right training and support, any drilling crew can quickly get up to speed.
Looking ahead
Digital bore planning is rapidly becoming a key tool for HDD contractors aiming for efficiency. Manual methods are finding it challenging to match the pace of today’s increasingly congested and tightly regulated underground environment. Embracing bore planning best practices and technologies allows contractors to help mitigate risk, streamline operations and deliver the high-quality results that project owners demand.
For bore planning assistance, contact your Vermeer dealer.
Vermeer Corporation reserves the right to make changes in engineering, design and specifications; add improvements; or discontinue manufacturing at any time without notice or obligation. Equipment shown is for illustrative purposes only and may display optional accessories or components specific to their global region. Please contact your local Vermeer dealer for more information on machine specifications.
Vermeer and the Vermeer logo are trademarks of Vermeer Manufacturing Company in the U.S. and/or other countries.
© 2025 Vermeer Corporation. All Rights Reserved.