The Vermeer D24 horizontal directional drill was engineered to solve modern-day drilling problems.
Intuitive features, like the single-button auto rod exchange? It’s got that.
Specific diagnostics to help reduce downtime? That too.
Next Generation components, such as hydraulics system, wire harnesses, thrust motors, vise clamp force and a redesigned rack and carriage?
You get the point.
Vermeer, the market leader in utility directional drilling for over three decades, knows the headwinds operators encounter. The D24 was built specifically to reduce those headaches.
“When a customer purchases a top-of-the-line machine like the D24, they have extremely high expectations — and we frankly want them to have those high expectations,” said Spenser Remick, a sales manager at Vermeer. “Customers are really expecting an integrated operator experience. They want to be able to increase the effectiveness of that operator on the machine, whether that’s a control perspective or a diagnostic perspective. They want to be able to have their operator understand exactly what’s going on with the machine, which really turns the operator and the machine into a force-multiplier on the job site.
“They’re able to get more done, more consistently, with more predictability than what we’ve ever seen.”
The D24 fulfils those expectations. Find out how this next generation drill from Vermeer was created in our latest “Behind the Design.”
“To bring the D24 to market, it’s required a diligent team of engineers and thousands of hours of work,” said Clint Recker, the product manager for utility HDD equipment at Vermeer.
Horizontal directional drilling market problems
When Vermeer team members speak with HDD customers, the problems they heard about are remarkably consistent: Customers need machines that optimize operator training needs and are increasingly productive and reliable.
“My role at the company is product manager, and my responsibility is working with our customers to understand their wants and needs,” Recker said. “We call this process ‘voice of the customer.’ This is the first step in the sequence of designing a new machine. As we understand the changes that they desire compared to predecessor models, we’re able to put those into action. Our customers have been asking for a compact, reliable, productive machine — and we deliver that with a D24.”
Horizontal directional drilling need: Labor constraints
Remick: “One of the biggest issues in the industry is labor. So being able to bring a new crew member into the crew, get them up to speed and improve the effectiveness of that crew quickly is a huge deal for them.”
Mike Byram, vice president of Infrastructure Solutions at Vermeer: “There’s a lot of HDD work going on right now between the fiber build out for the internet, for power undergrounding, for storms and fires and grid upgrades, that type of thing. There’s a lot of work out there. A market problem is uptime and productivity. … Labor is a constraint for our customers and a problem, so how we want to address that problem is through making our equipment easier to use and more productive.”
Horizontal directional drilling need: Productivity advantage
Recker: “When I talk to our customers in the market, their main challenges are around productivity and reliability. They need a machine that allows them to get work done quickly, a very capable machine. They also need a machine that’s very reliable. If they’re not working on the jobsite, they’re not getting paid. Our crews are dealing with the challenge of finding skilled workforce, so features that make it easier to train a new operator or features that help retain their current skilled workforce are beneficial to our customers.”
Remick: “(Customers) want the machine to perform when they need it to perform. And if there is a need for downtime or any scheduled maintenance, they want to be able to plan that ahead versus unplanned downtime, which is a huge pain point for a lot of customers that we interact with. They understand that machines require maintenance and normal upkeep, but the more we can schedule that, and the more that can be predictive, the more efficient their operation will be.”
Recker: “Some of the main market problems that our customers have is that in some certain utility types, it’s pay. They’re challenged in some of those markets based off what they get paid, and with those lower rates, they’re really focused around getting more product installed in a day, so they have to get more footage installed in a day, and the machine has to be reliable. It has to be working.”
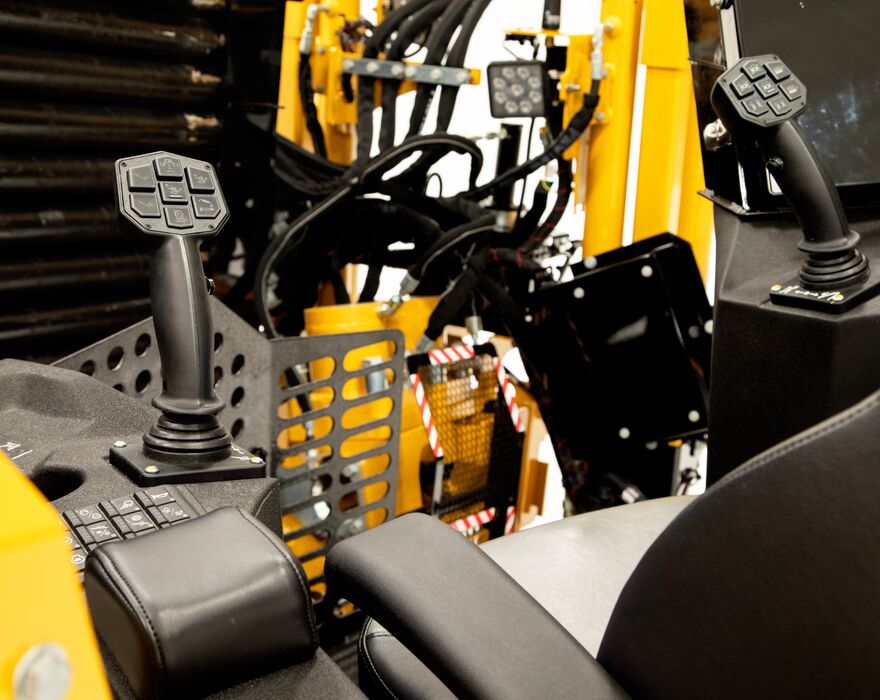
Solution to directional drilling headaches? Meet the D24
Faced with answering these customer needs, the infrastructure solutions team at Vermeer engineered the D24 horizontal directional drill.
The D24 features Vermeer Next Generation technology: On-rig intelligent diagnostics that provide a specific explanation and prescriptive troubleshooting steps, one-button automated rod exchange that completes the entire rod changeout sequence and eliminates up to 19 steps and a patented, sliding, open-side vise to minimize the number of steps to change out a rod.
Automated rod exchange: ‘A big game-changer’
Lee Schroeder, Vermeer product support manager: “We looked at, ‘How do we drive efficiency throughout the operator’s process?’ Being able to automate the drill out and pull back rod exchange sequence is a critical component of that. With the automated rod exchange, a customer literally hits one button and sits back and watches that whole process take place in front of them — something that we’ve never done and something that the market doesn’t have today. And that’s pretty exciting and a big game-changer for us.”
Remick: “The machine is going to do the rod exchange sequence the same every time, and anybody in the HDD market knows that the sequence in which rods are added or pulled back is critical. So the machine is able to do all of those things, basically, simultaneously in the same order every single time.”
Kevin Sebolt, the Vermeer new product coordinator on the D24: “We’ve spent a lot of time testing the automated features. The D24 has had (extensive) cycle testing of rod exchange make and break cycles done.”
Next-level reliability, industry-leading on-rig diagnostics
Jason Morgan, Vermeer engineering manager: “There was a lot of focus on making (the D24) transmissions extremely rugged and reliable. So those transmissions have the ability to transmit a lot of power for a long time, very reliably, even in really rough ground conditions. …
“Every system on the machine was scrutinized and tested to deliver reliability.”
Schroeder: “With the new user interface on the Gen4 controls, we’ve integrated more onboard diagnostics and troubleshooting capabilities with an integrated service tool. This allows for our customers to have more visibility to the machine controls and really optimize the performance on rig.”
Recker: “Our onboard diagnostics — the ability for our customer to do what used to require a service tech coming and plugging in a laptop — (allows operators) to understand and diagnose certain issues on a machine if they were to arise.”
Future of horizontal directional drilling: Vermeer Next Generation technology
The D24 represents more than a new machine for Vermeer; it’s the future of directional drilling at Vermeer. The D24 and the D550 HDD were the first Next Generation drills launched by Vermeer.
“We want to be the technology leader within the HDD market, and we’re going to continue to strive for that,” Byram said.
Expect productivity and reliability to be front and center for the Vermeer product development team, Recker said.
“Vermeer has continued to drive the industry forward for more than 30 years because of constant innovation and our desire to provide our customers with productive and profitable equipment,” he said. “Like Gary Vermeer said: Find a need. Fill that need with a product built to last, and simply build the best.”
To inquire about purchasing the new D24, reach out to your local Vermeer dealer.
Vermeer Corporation reserves the right to make changes in product engineering, design and specifications; add improvements; or discontinue manufacturing or distribution at any time without notice or obligation. Equipment shown is for illustrative purposes only and may display optional accessories or components specific to their global region. Please contact your local Vermeer dealer for more information on machine specifications.
Vermeer and the Vermeer logo are trademarks of Vermeer Manufacturing Company in the U.S. and/or other countries.
© 2025 Vermeer Corporation. All Rights Reserved.