The best jobsite tooling solutions often come from addressing the challenges contractors face in the field. When Vermeer noticed recurring issues with bit retention across various horizontal directional drilling (HDD) crews, including Mears Group Inc. in South Florida, the team set out to develop a solution. Drawing on real-world feedback and field testing, Vermeer created the Bit Boss retention system — a reliable, jobsite-driven solution that helps optimize productivity and minimize downtime for HDD operations.
Challenge: Persistent bit retention issues with HDD tooling
In South Florida’s coral rock terrain, Mears’ HDD crews struggled with recurring bit retention issues. The dense and abrasive nature of coral rock caused frequent bit mount failures, forcing crews to stop operations, retrieve broken bits and replace components. This not only disrupted productivity but also increased repair costs and project timelines.
“Coral rock is one of the toughest materials we deal with,” said Jose Diaz, HDD supervisor for Mears. “When a bolt snaps and a bit is lost, we lose steering control and often face additional downtime to excavate and replace the broken parts.”
The challenges faced by Mears in South Florida were not unique. HDD contractors across various regions experience similar issues in abrasive ground conditions. Recognizing this widespread issue, Vermeer proactively engaged with contractors to better understand the root causes of bit retention failures in HDD tooling and began working toward a solution.
Approach: Jobsite-inspired innovation in HDD tooling
To address these challenges, Vermeer leveraged its Cutting Edge team to design a retention system capable of handling the most demanding drilling environments. Through its Vermeer Southeast dealership and direct feedback from contractors like Mears, Vermeer developed and refined the Bit Boss system.
“Our team approached Vermeer with some of the difficulties we were experiencing,” said Blas Riesgo, director of Mears’ South Florida operations. “They took that feedback seriously and worked to create a solution that could hold up under pressure.”
The result was the Bit Boss shoulder screw retention system. By incorporating three additional shoulder screws into the traditional six-bolt design, the Bit Boss system significantly improved bit retention and durability. Vermeer tested the system extensively in the field, including during projects in South Florida’s challenging coral rock conditions.
“The Bit Boss system helps improve bit retention and reliability,” said Cody Mecham, product manager for Vermeer Lifecycle. “It’s designed to help HDD crews maintain productivity and minimize maintenance delays.”
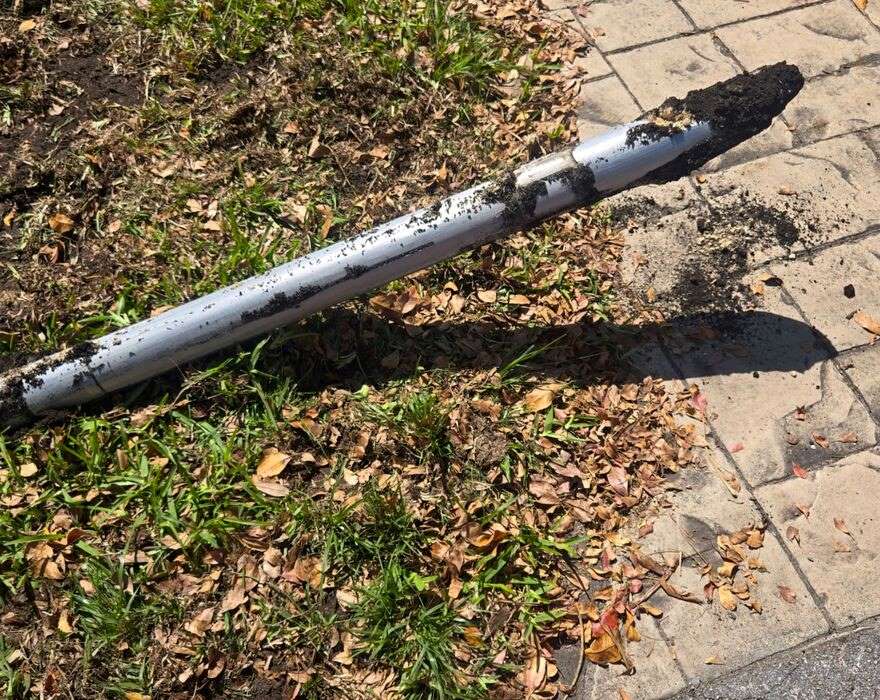
Results: Reliable HDD tooling that delivers
The Bit Boss system has proven highly effective for contractors working in tough conditions. Mears crews quickly noticed the system’s reliability and reduced downtime.
“With the Bit Boss system, bits only need replacing due to regular wear, not unexpected failures,” said Diaz. “That’s exactly what we needed to stay productive in South Florida.”
After seeing the benefits, Mears has begun to standardize the Bit Boss system across their fleet of Vermeer HDD rigs, including the D24x40 S3, D10x15 S3 and D23x30 S3 models. They paired the system with Vermeer premium transmitter housings, QuickFire® connection systems, and ACE™ Pro Extreme bits to create a consistent, efficient setup across all their HDD tooling operations.
“Standardizing our tooling setup has helped us streamline maintenance and keep projects on track,” said Riesgo. “Having reliable equipment means we can adapt to changing conditions without worrying about breakdowns.”
Turning contractor challenges into innovative HDD tooling solutions
The Bit Boss system demonstrates how the team at Vermeer listens to contractors and turns field challenges into innovative solutions. By collaborating with crews like those at Mears and applying jobsite feedback, the team at Vermeer created a system that helps address bit retention challenges in HDD operations.
“Contractors play a vital role in the innovation process,” said Mecham. “By paying attention to what they experience in the field, we can design tools that make a real difference on the jobsite.”
The Bit Boss system shows a proactive approach to solving problems and dedication to improving HDD tooling. As more contractors put the system to work, it demonstrates how effective solutions emerge from real jobsite experience.
Want to learn more?
Explore how the Bit Boss system can make a difference on your HDD jobsites. Contact your local Vermeer dealer for more information.
This article contains third-party observations, advice or experiences that do not necessarily reflect the opinions of Vermeer Corporation, its affiliates or its dealers. Testimonials and/or endorsements by contractors in specific circumstances may not be representative of normal circumstances experienced by all customers.
Vermeer Corporation reserves the right to make changes in engineering, design and specifications; add improvements; or discontinue manufacturing at any time without notice or obligation. Equipment shown is for illustrative purposes only and may display optional accessories or components specific to their global region. Please contact your local Vermeer dealer for more information on machine specifications. Vermeer, the Vermeer logo, Bit Boss, QuickFire and Ace are trademarks of Vermeer Manufacturing Company in the U.S. and/or other countries.
© 2025 Vermeer Corporation. All Rights Reserved.