Over the past 30 years, technological advances have dramatically expanded horizontal directional drilling (HDD) capabilities. Modern operations rely on sophisticated systems, from specialized drilling fluids that help maintain bore paths to advanced tooling that enables work in challenging ground conditions. Vacuum excavators have become indispensable, allowing crews to verify utility locations and manage drilling fluid.
While these technologies have transformed the industry, new challenges continue to emerge. Manufacturers, including Vermeer, remain committed to developing solutions through ongoing research and innovation.
As infrastructure demands drive industry growth, contractors face mounting pressures. A skilled labor shortage looms as experienced operators retire and industry pioneers depart. Projects grow increasingly complex with crowded rights-of-way while documentation requirements become more demanding.
Today’s directional drill
Drill manufacturers introduced the controller area network communications system (CAN bus) to address skilled labor concerns and minimize complexity. This system connects drill functionality to joystick controls through a simplified network of wires, reducing operator input and improving machine serviceability. Compared to earlier HDD systems that relied on individual switches, CAN bus technology represents a significant advancement in operation and maintenance.
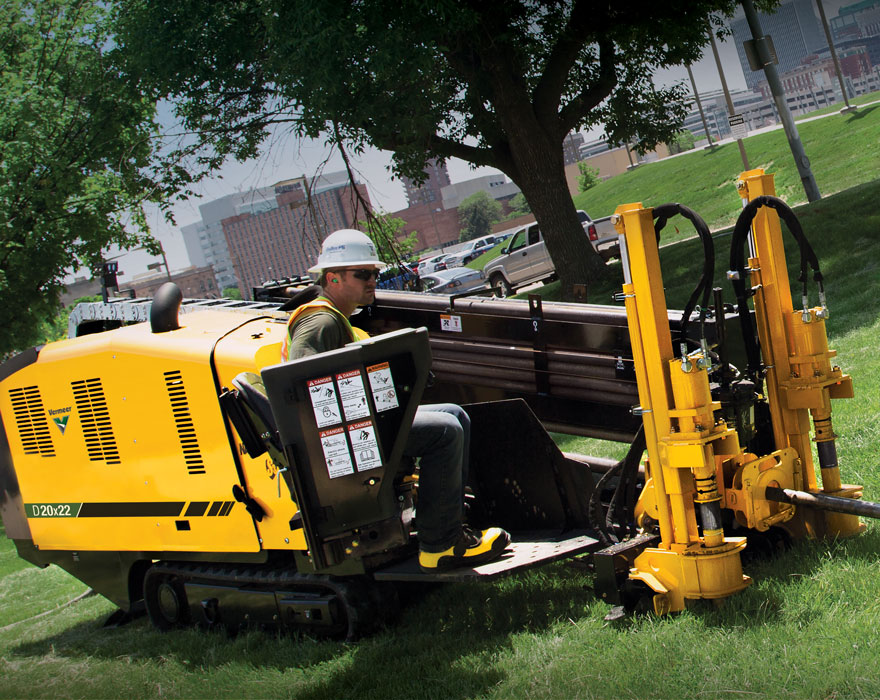
Current Vermeer HDD models equipped with CAN bus systems have 30% fewer wires than traditional models, significantly simplifying troubleshooting and maintenance procedures. The system enables manufacturers to implement standardized controls while incorporating automated features across their drill lines.
The CAN bus enables comprehensive telematics data collection for proactive maintenance and productivity tracking. This allows contractors to manage maintenance schedules better and monitor drill performance metrics for optimal operation.
Future of onboard technology
As HDD technology continues to evolve, manufacturers focus on making drills easier to operate through automated functionality and enhanced access to machine diagnostic information, helping to address labor challenges.
Recent innovations, like those in the Vermeer D24 drill, demonstrate this commitment to simplifying operations while providing deeper insight into machine performance. Advanced systems such as the automated rod exchange (ARE) integrated into the D24 can execute complete rod changeout sequences with minimal operator input, thereby eliminating numerous manual steps that were previously required. This automation helps deliver consistent performance and extends component life through precisely controlled movements. It also addresses workforce challenges by simplifying training and maintaining stable performance standards.
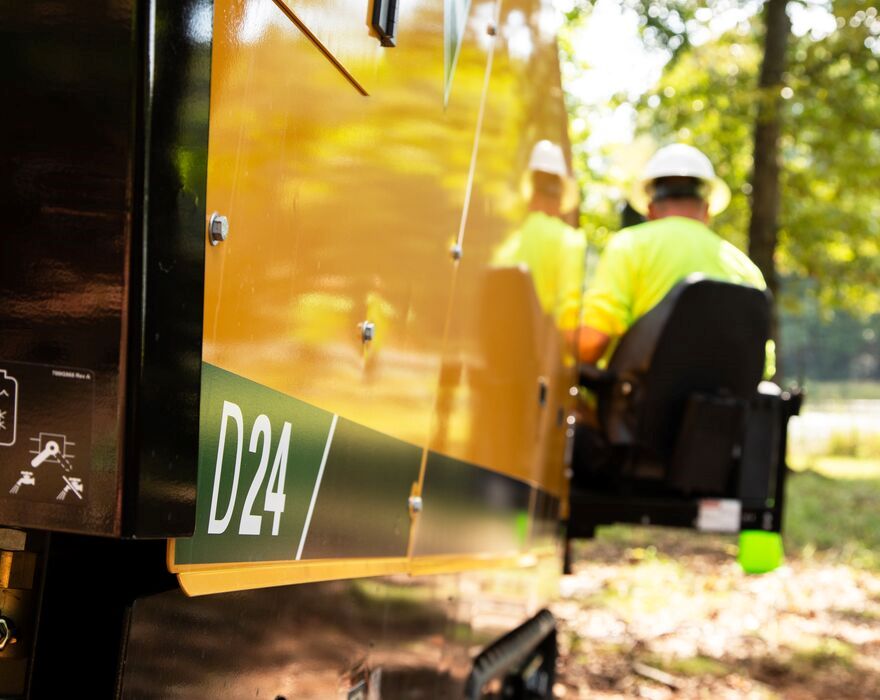
Advanced onboard diagnostic systems represent another significant development in the industry. These systems use intuitive touchscreen displays to guide operators through troubleshooting steps, providing clear instructions for checks and potential solutions. This enhanced diagnostic capability helps quickly identify and resolve issues, minimizing associated downtime that can impact project timelines.
By combining automation with improved diagnostic capabilities, manufacturers are developing machines that better support contractors’ needs. Detailed diagnostic information helps technicians arrive prepared with solutions when service is required, further reducing potential downtime. These innovations demonstrate the industry’s commitment to meeting evolving demands while focusing on operator efficiency and machine reliability.
HDD training technology
On-rig technology isn’t the only area manufacturers focus on to help HDD contractors. While optimizing machine functionality is essential, new crew members still face a steep learning curve. This is where dealer-led training programs and advanced simulators play a crucial role.
While on-the-job training has traditionally been the primary method for teaching HDD operations, it has significant drawbacks. Operating expensive equipment while learning can create unnecessary stress and may cause operators to focus more on avoiding mistakes than absorbing essential knowledge.
Modern HDD simulators offer a solution to these challenges by providing a low-stress learning environment. Using virtual reality (VR) technology and realistic controls that match actual drilling equipment, these simulators allow operators to develop proper techniques without risking equipment damage in a controlled environment.
These sophisticated training systems provide a comprehensive virtual environment. For example, the Vermeer HDD Simulator starts with basic control familiarization, using transparency modes that allow operators to see internal mechanisms like rod loader arms and components. This helps trainees understand the relationship between their control inputs and machine operations.
As training progresses, operators learn underground steering techniques through VR visualization of the drill head’s movement and deflection patterns. The systems show both the physical movement and corresponding display screen indicators, helping operators understand how to avoid overbending rods while maintaining proper bore paths.
Modern simulators feature comprehensive training modules covering everything from basic operations to advanced techniques. These systems provide real-time feedback on performance, track operator progress, and generate detailed reports on proficiency levels. This structured approach helps ensure consistent, high-quality training across organizations while accelerating the learning curve for new operators.
Bore planning and documentation
Planning a bore is also critical for HDD contractors. Crews must calculate specifications based on their drill rig, drill rod and the product’s allowable bend radius. Additionally, municipalities increasingly require contractors to submit as-built documentation after project completion. New software solutions are emerging to address these challenges to streamline planning and documentation processes.
Modern bore planning applications combine GPS technology, aerial imagery and sophisticated calculation tools to help contractors develop accurate bore plans. These tools allow crews to map utilities, calculate complex geometries and generate detailed documentation. The BorePlan application from Vermeer offers features like straight-line bore planning, utility mapping and rod-by-rod plans accessible directly on mobile devices. Other industry solutions provide similar capabilities, with premium versions offering advanced features like compound curve planning and CAD exports.
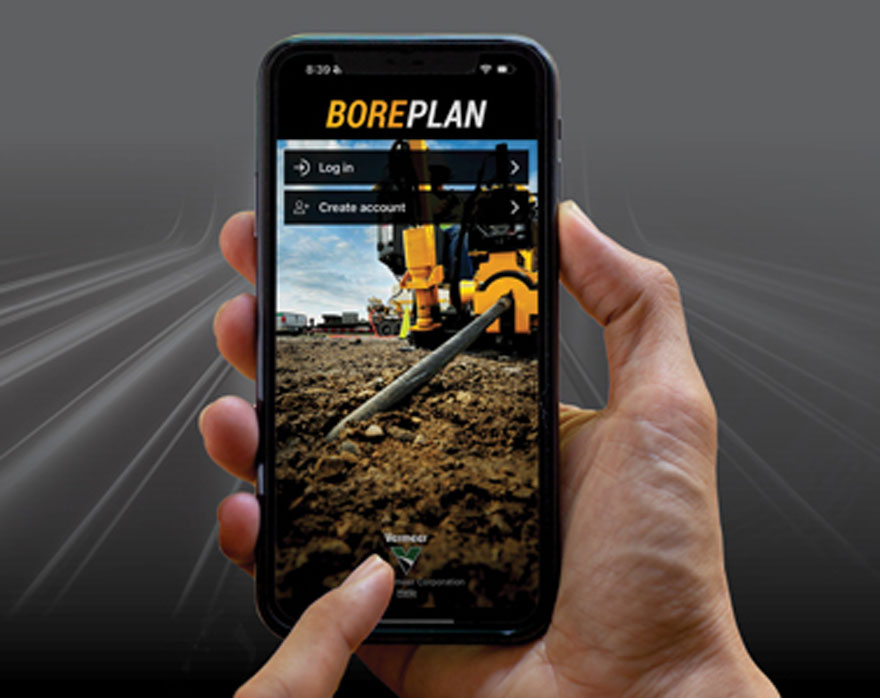
These digital tools are particularly valuable for managing complex projects in congested urban environments. They help contractors visualize potential obstacles, calculate optimal bore paths and maintain detailed records throughout the project lifecycle. As documentation requirements continue to evolve, these applications are becoming essential tools for modern HDD operations, helping crews work more efficiently while meeting increasingly stringent industry standards.
Advancing through innovation
The horizontal directional drilling industry has transformed from its labor-intensive beginnings through continuous innovation in automation, training technology and digital planning tools. These advances help address critical challenges like skilled labor shortages while enabling contractors to tackle increasingly complex projects. Modern HDD technology is well-positioned to support the next generation of underground construction projects, from sophisticated onboard systems to comprehensive planning software.
Vermeer Corporation reserves the right to make changes in engineering, design and specifications; add improvements; or discontinue manufacturing at any time without notice or obligation. Equipment shown is for illustrative purposes only and may display optional accessories or components specific to their global region. Please contact your local Vermeer dealer for more information on machine specifications. Vermeer and the Vermeer logo are trademarks of Vermeer Manufacturing Company in the U.S. and/or other countries.