Cutter tips are an integral part of your grinder’s performance. If they start to wear down, they can drastically alter your productivity and output. Making sure they’re maintained and checked regularly can lead to a difference in your end product and overall machine efficiency. Read on to learn why you should change them, when to change them and how to do it, along with what kind of cutter tip is the right value for you and the different cutter tip options from Vermeer.
Why you should change your cutter tips
First, let’s talk about why it’s necessary to change your cutter tips out. Running your grinder with worn down cutter tips can lead to:
- An excessive amount of fuel burn
- Loss of productivity
- Wear and tear throughout the entire machine
- Poorer quality end product
These reasons are why it’s important to make sure your cutter tips are in good shape. Cutter tips are a valuable piece of your grinding operation and the impact of them being worn down can be large.
When to change your cutter tips
To help prevent wear and tear on your grinder due to worn down cutter tips, you should check your tips regularly throughout the day. It’s best practice to examine them in the morning before start up, during your midday break and at the end of the day after shut down. Not checking your tips daily can lead to costly wear. Refer to your machine’s operator’s and maintenance manual for safety messages and further instructions.
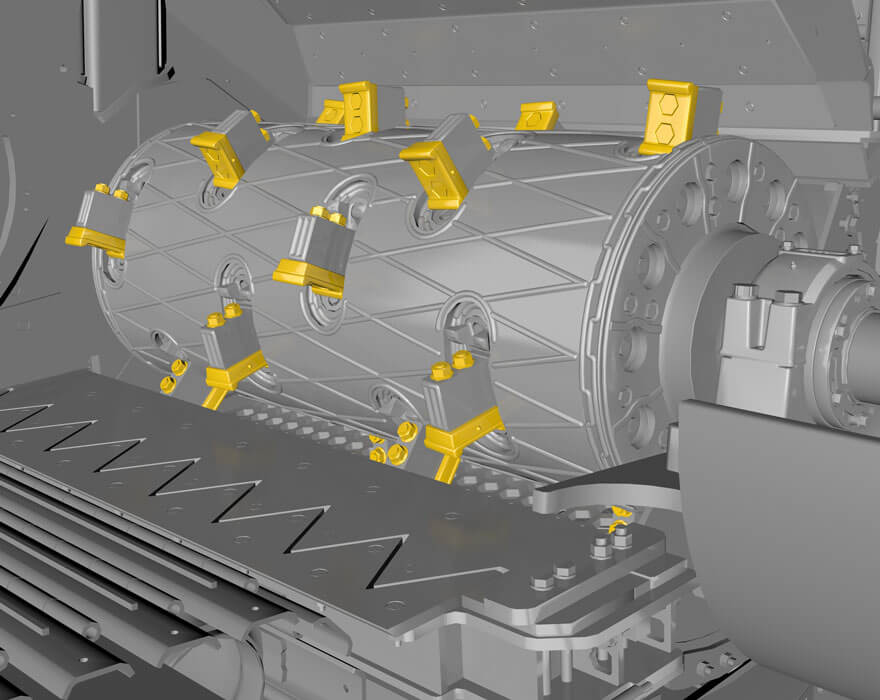
Signs to watch for
During your daily checks, you should know the signs that indicate when it’s time to replace cutter tips. Here are some to look out for:
- On the base block, look for wear on the outside corners
- On the carbide, watch for wear on the top two corners
- A change in output, such as stringier material coming out of the grinder
- Lower grinder productivity
If you notice any of these signs, you should shut down your machine and either flip or replace the worn cutter tips. Ted Dirkx, Vermeer sales manager for recycling and forestry, had some additional insight into what to do when you see wear: “Once you wear through the carbide flakes that are applied to the base block, you should start considering whether you flip the cutter tip, since they’re dual-sided, and wear the other side, or replace it. Once you get through the carbide flake, you get to the base block, which can wear much quicker.”
Cutter tips are designed to help protect the hammer that holds the block in place. In other words, it’s a consumable wear part protecting a much more costly wear part.
“It can be tempting to wait to change your cutter tips and run your grinder as long as possible, but that can mean material eating into the hammer and shortening its overall life,” explained Dirkx.
In the long run, you can be better off from a time perspective when you replace your cutter tips before they start to eat into your hammer.
On average, if you’re grinding on a consistent basis, you’ll likely be wearing through cutter tips on a weekly basis. In that instance, it’s necessary to have a good amount of cutter tips on hand when wear happens.
Screen size and material type matters
The size of your screen factors into your cutter tips’ longevity. If you’re using a large screen, there’s less circulation of material, so there will be less wear on your cutter tips. If you’re using a small screen, there’s more circulation, which can lead to more cutter tips wear.
The kind of material being put through the grinder is also a big factor. Dirty material with sand, small rocks and leaves are all common abrasive material that causes tips to dull. That’s why reducing contamination before it goes into the grinder can help maximize cutter tip life.
“You should also think about the surface that the material is sitting on,” said Dirkx. “A solid surface, such as concrete or asphalt, can keep material cleaner, as opposed to dirt.”
Another consideration is how you’re loading the material into the grinder. Using a wheel loader to scoop from the bottom of the pile, you’re more likely to pick up dirty material. If you use an excavator with a clam shell grapple that grabs material from the top, you can shake the material before you put it in the grinder. With an excavator, the operator is also more likely to see other heavy contaminates in the material, like a fence post, that could lead to excessive wear or failure to the cutter tip.
On average, if you’re grinding on a consistent basis, you’ll likely be wearing through cutter tips on a weekly basis.
How to change your cutter tips
Now that you know why and when you should change your cutter tips, let’s focus on how it’s done. Thankfully, it can be a relatively smooth and efficient process. Based on the experience of product specialists, two experienced operators with the proper tools can flip or replace the cutter tips in less than an hour. Refer to your machine’s operator’s and maintenance manual for safety messages and further instructions.
First, the bolt on the cutter tip goes through the hammer, and there’s a nut on the back. Vermeer cutter tips have a hardened bolt with a locking flange nut. If a regular nut is used, it can wriggle loose and come off, so it’s crucial to use Vermeer-recommended bolts and locking flange nuts.
Next, make sure the nuts are torqued on. Using an impact drill to put them on can lead to an improperly torqued cutter tip. It’s highly recommended to use a torque wrench to allow a properly torqued cutter tip. The torque should also be rechecked after one hour of grinding.
Pro tip: When replacing or flipping multiple cutter tips at a time, use a paint marker so you can quickly identify which tips you’ve already torqued properly.
“Another issue to watch out for is over-torquing,” said Dirkx. “If you overtighten the nut, you can stretch the bolt, which leads to premature bolt fatigue and can cause it to break.”
Reference your grinder’s operator’s manual for the proper torque specifications.
As you’re changing out cutter tips, keep in mind that wear can make the tips change shape and weight. The drum is spinning at 1200 rpm at times and changing out one tip can change the balance of the drum.
“When you change out tips, make sure you change the tip at the opposite end at the same time to maintain proper balance of the hammer,” explained Dirkx. “Otherwise, it can lead to the machine vibrating and create a greater weight imbalance.”
What kind of cutter tips you should buy
There are a variety of different styles of cutter tips you can use on your grinder. Whatever kind you go with, it’s helpful to consider the value it provides you. For instance, Vermeer cutter tips are designed to provide maximum value and cutter life.
Vermeer cutter tips are designed and tested by Vermeer engineers to meet customer expectations for wear and productivity, as well as a quality fit. “It’s recommended to use Vermeer parts for such a critical part of the grinder,” said Dirkx. “Other brands may not fit properly.” Vermeer cutter tips fit close to the skin of the drum for a quality fit.
With 20 tips on most Vermeer grinders (or 14 tips on some smaller models), it’s helpful to have an extra set of tips on hand at all times. “If there’s a contaminate strike and you damage some tips, an extra set allows you to minimize lost productivity.”
With an extra set, you can be ready to handle unexpected wear. Work with your local Vermeer dealer on a stocking plan, so you don’t run out of cutter tips.
Vermeer cutter tip options
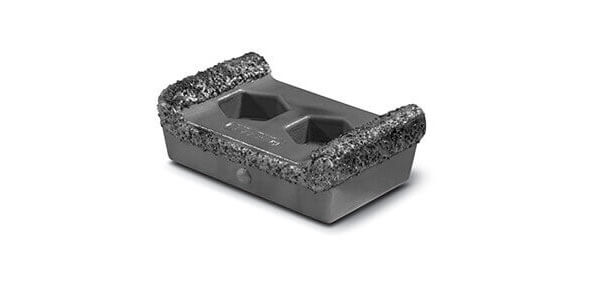
Wide block tips
Wide block tips are the most common in the industry. They can be used in a variety of applications, such as land clearing, regrind, pallets, compost and green waste. Wide block tips can be flipped for extended life.
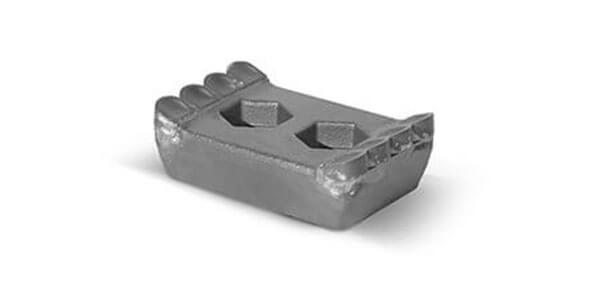
Abrasion-resistant tips
Abrasion-resistant (A/R) tips are used when highly abrasive material is being processed. Their flat face design, infused with tungsten carbide crystals in the casting block, is best suited for applications that contain sand, dirt and other highly abrasive materials. A/R tips can be flipped for extended life.
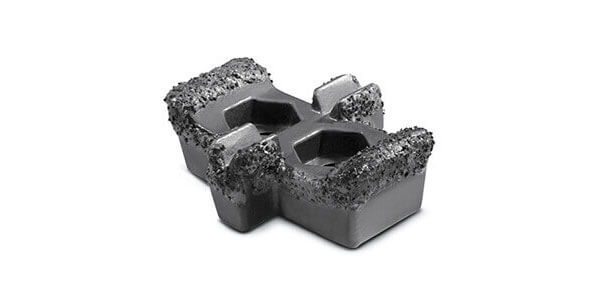
Wing tips
Wing tips have a unique design with an overlay of carbide that provides an effective solution for processing large-diameter woody material — a narrow center section helps the tip penetrate the log, then the wings clean out the remainder. Wing tips can be flipped for extended life.
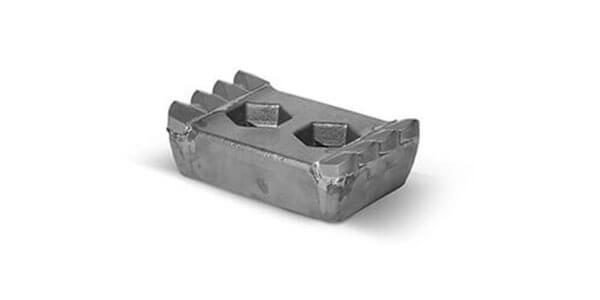
Impact-resistant tips
Impact-resistant (I/R) tips offer an alternative to wing tips and are used to process large-diameter material. Their carbide inserts are very hard, but also brittle, and are not intended to be used when contaminants are prevalent. I/R tips are cost-effective, offering dual side use.
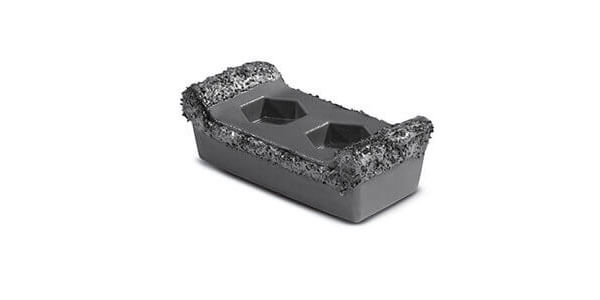
Narrow block tips
Narrow block tips only in the standard configuration are available for tub grinders and select horizontal grinders. They have an overlay of carbide along the sides of the block, making them an effective solution for processing large-diameter woody material. They’re cost-effective, offering dual side use.
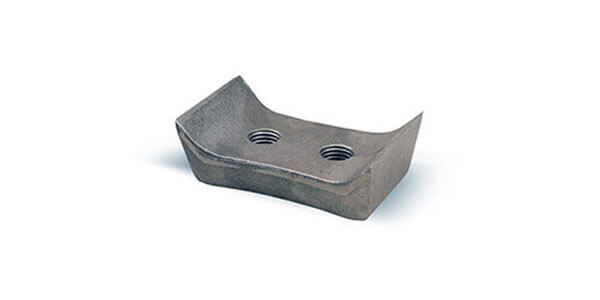
Sharp tips
Sharp tips are precisely designed for cutting. They are most commonly used on large diameter wood for max production and minimal fines. With a sharp leading edge these tips don’t handle high contamination and will wear out sooner when compared to our other tips. Sharp tips can be flipped for extended life.
With daily checks, regular change-outs, quality parts and a stocking plan in place, you can be confident that you’re getting the most out of your grinder cutter tips. For more information about Vermeer cutter tips and grinders, reach out to your local Vermeer dealer today.
Prior to performing service or maintenance on Vermeer equipment, always refer to the product’s maintenance and/or operator’s manual for safety messages and further instructions.
Vermeer Corporation reserves the right to make changes in engineering, design and specifications; add improvements; or discontinue manufacturing at any time without notice or obligation. Please contact your local Vermeer dealer for more information on machine specifications.
Vermeer and the Vermeer logo are trademarks of Vermeer Manufacturing Company in the U.S. and/or other countries. © 2022 Vermeer Corporation. All Rights Reserved.