Continuous bore shots of 800 feet (243.8 m) in the sandy soils of Long Island, New York, and all the machinery needed to be taken off the road at the end of each day — these were just a few of the challenges that Eastern Utilities Services LLC faced on a recent 18,400-foot (5,608.3-m) electrical transmission conduit project on Long Island. The electrical transmission line upgrade project was located next to a busy highway, which connects the Long Island Rail Road (LIRR) Ronkonkoma Station and Long Island’s MacArthur Airport, requiring that the footprint left by Eastern Utilities’ crews avoided disrupting traffic flow and caused minimal public interference. The result was longer bore shots and a creative fluid management plan.
When the electrical transmission conduit project opened for bid, Jon and Tom Schumchyk, vice presidents of Eastern Utilities and Haugland Group LLC, had several general contractors reach out to them, as other local horizontal directional drill (HDD) contractors were not capable of the longer bore distances. “Manholes were spaced out to 800 feet (243.8 m) on this project, and most contractors wanted to do each install in two shots, but it was the owner’s preference to do them in one to minimize disruptions,” Jon explained, “Each bore diameter needed to be between 18 inches and 20 inches (45.7 cm and 50.8 cm) to accommodate dual or triple 6-inch (15.2-cm) conduit bundles. Those specifications quickly reduced the number of contractors who had the personnel or machinery to do the job.”
Having recently joined forces with its long-time customer, Haugland Group, Jon and Tom had the experienced team and right equipment to complete the project successfully. “We started our business in 2001, running small HDDs, and we pushed them to their limits,” Tom said, “As we grew, we focused on increasing our expertise on larger diameter work. We’ve worked alongside the team at Grace Industries LLC (Haugland Group’s civil construction division) on many of the most challenging jobs we’ve done. Joining their organization allowed us to grow quickly and safely, and to operate more efficiently.”
Planning considerations
Eastern Utilities got to work on the planning process immediately after the project was awarded. “We recently expanded our fleet with the addition of a Vermeer D100x140 S3 Navigator® HDD to complement our growing line of drills,” said Tom. “We’ve run several brands of drills over the years, and still operate a bit of a mixed fleet, but we’ve been impressed by the performance and ease of use of this latest addition.”
With the addition of the larger drill, the Schumchyks also added a Vermeer R250C reclaimer to keep pace. That unit is capable of recycling up to 250 gallons per minute (946.4 L/min), and the machine’s two-deck shaker design helps decrease the sand content levels, which is essential for Long Island ground conditions.
“The two key challenges Eastern Utilities encountered during the planning phase were to determine how much fluid needed to be delivered to the drill each day, and how we were going to manage the recycling process, given that we had to pull equipment off the road at the end of each day,” said Tom. “We ran the numbers to determine what kind of rate was needed to get enough fluid down the hole and keep our sand levels as low as possible. To do the footage required, we needed to manage around 65,000 gallons (246,051.8 L) of fluid per day, which is a lot of fluid to make up, transport and recycle daily.”
After determining how much fluid the crews needed to run, Tom developed a fluid management plan and machine configuration. “Since setting up the R250C on the job each day wasn’t a feasible option, we established a mud recycling site, where we would bring used drill slurry for processing,” he explained. “Once clean, we would then use large water trucks to bring mud back to the drill.”
With those details worked out, it was time to put the plan into action. During the first week of March, Eastern Utilities began staging equipment.
On the job
For most large-diameter projects, Eastern Utilities usually divides their team into three crews: drilling, fluid management and test pitting. Given the scale of this project and their responsibilities onsite, pipe fusing and traffic control crews were also added, building the team to approximately 30 people. The Eastern Utilities team was supported by several other Haugland Group companies, including Eastern Utilities’ Vacuum Excavator Truck Division, Grace Industries and Midnight Trucking. Handheld radios were used to keep the overall operation running smoothly and efficiently.
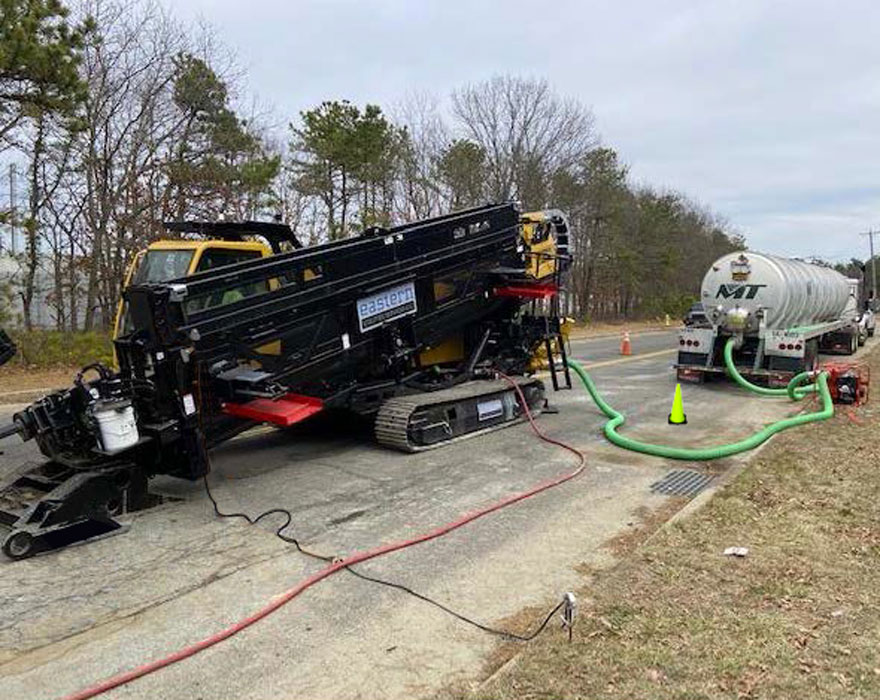
Drilling operations
On the Vermeer D100x140 S3 was George Schultz. It was the responsibility of everyone on the team to keep him in position to consistently be putting rods in the ground. “George is one of the smoothest drill operators I’ve ever worked with, and the whole drill crew maintained an ambitious drill rate,” said Tom. “At first, they were completing the 800-foot (243.8-m) bores in around 12 hours, but after the first few bores, they were getting them done in eight hours flat!”
Each day, the drill crew walked the machine into position, aligned the rod loading boom truck and tanker trailers, drilled out 800 feet (243.8 m) followed by a back ream with small reamer, drilled back out 800 feet, then finally pulled the conduits in on the fourth pass. Each day, they were drilling 3,200 feet (975.4 m) of rod in only eight hours, which included swapping out rod baskets several times every pass. “The footage we were able to do in a day speaks volumes of the folks we have working for us and how easy that big D100x140 S3 is to use,” added Jon.
A DigiTrak® Falcon® F5® locating system was also used on this project. The locator’s software logged the 22 bore paths, allowing Eastern Utilities to easily produce a precise as-built drawing and CAD overlay for the customer as soon as the job was done, without retaining an engineering firm. “Good equipment almost always translates to cost savings!” said Jon.
The Eastern Utilities drill crew achieved an average bore speed of 25 feet per minute (7.6 m/min) on the 8-inch (20.3-cm) pilot bore, 10 feet per minute (3 m/min) on the pre-ream pass and 30 feet per minute (9.1 m/min) on the ream and pipe pullback. Each drill path was bored to 18 inches or 20 inches (45.7 or 50.8 cm), depending on whether a double or triple 6-inch (15.2-cm) conduit bundle was being installed. Well over one million gallons (3.8 million L) of fluid were used on the 18,400-foot (5,608.3-m) project with a 125-gallon per minute (473.2-L/min) pumping average. The R250C supplied a sufficient amount of cleaned drilling fluid to maximize production.
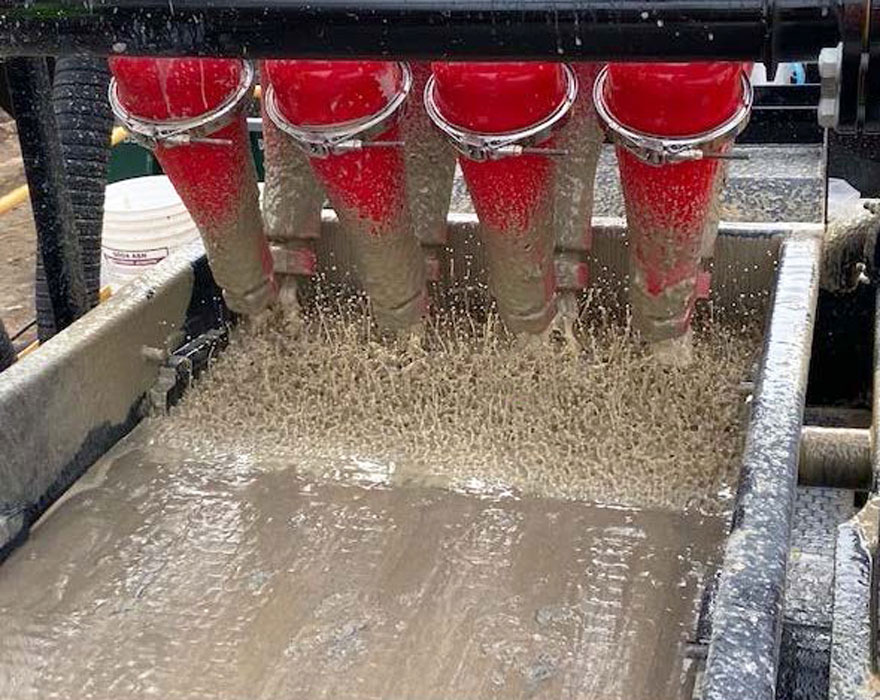
Fluid management
Eastern Utilities mud experts oversaw the fluid management of the operation. To maintain the bore path integrity, the team delivered a mud viscosity that Tom describes as, “considerably higher than 90-second mud.”
“Keeping the hole open is always a fight in the sandy soil conditions found on Long Island,” said Tom. “We needed to make sure the mud is thick enough to maintain the bore walls, but if it gets too thick it can’t be recycled, and recycling the fluids is essential to the job. There aren’t many fluid disposal sites in the area, and those that exist can be costly. It would have taken more than ten large vacuum excavator trucks on a project of this size and scope, pumping and dumping to keep pace with the drill. The costs would have been exorbitant.”
Chris Root and Carlos Jayme with Vermeer North Atlantic helped the crew dial in the mud recycling system. “Eastern Utilities was one of the first contractors in the region to use mud recycling systems, and continues to innovate in that area, which helps keep operational costs in check,” said Jayme. “The unique setup for this project allowed them to see recycling returns that were 20% to 40% sand down to a reclaimed sand content of .25%.”
Spoils from the exit pits were hauled to the mud recycling site in a nearby staging yard and offloaded into dumpsters for processing. “This arrangement allows extra settling time, and if the sand levels were running on the high side, additional clean drilling fluid could be added to help with dilution,” said Chris. “We also made some adjustments to the shaker deck’s screen sizes to achieve our desired sand content output levels. Some of those adjustments were ongoing because the soil conditions varied.”
Eastern Utilities used another manufacturer’s mud recycling system briefly on the project. “We heard good things about the shaker on the other unit, so we gave it a try,” said Tom. “The shaker worked great, but the Vermeer R250C was easier to dial in, and gave us a lower sand content output percentage. After a few days on the project, the other unit just sat there.”
Haugland Group was also able to haul away and use the reclaimed solid sand materials. Clean sand that came off the R250C shaker decks could be used as fill or to make concrete on other Haugland Group projects. “We would have traditionally paid to haul and dump that material, but with the reclaimer, we’re not only saving on the disposal, we’re making money on what used to be waste” said Jon.
On and off the job quickly
A few weeks into the job, much of New York was under a shelter-in-place order due to COVID-19. However, this particular project was deemed essential and allowed to continue by the local authorities. As a result, commuter congestion was greatly reduced, allowing crews to take advantage of fewer cars on and around the project. “The drilling portion of the project was completed three times faster than expected,” said Jon. From start to finish, Eastern Utilities completed 22 drill shots, most in excess of 800 feet (243.8 m), in less than two months, with a total of 35 drilling days. “It all went extremely smooth considering the limited time each day we were allowed to occupy the roadway, the implementation of additional safety requirements for COVID-19 and the sandy ground conditions of our local Long Island soil. We are proud of everyone on our team for their efforts on this project, and look forward to our next endeavor with the help of our local and nation-wide Vermeer team!” concluded Tom and Jon.
This article contains third-party observations, advice or experiences that do not necessarily reflect the opinions of Vermeer Corporation, its affiliates or its dealers. Testimonials and/or endorsements by contractors in specific circumstances may not be representative of normal circumstances experienced by all customers.
Vermeer Corporation reserves the right to make changes in product engineering, design and specifications; add improvements; or discontinue manufacturing or distribution at any time without notice or obligation. Equipment shown is for illustrative purposes only and may display optional accessories or components specific to their global region. Please contact your local Vermeer dealer for more information on machine specifications. Vermeer, the Vermeer logo and Navigator are trademarks of Vermeer Manufacturing Company in the U.S. and/or other countries. DigiTrack, F5 and Falcon are trademarks of Digital Control Incorporated.
© 2020 Vermeer Corporation. All Rights Reserved.