Successfully performing large-diameter horizontal directional drilling (HDD) projects often involves running large quantities of drilling fluid, especially on long-distance bores and in rocky conditions. The cost of disposing the returns can be very high and accessing an approved disposal location is difficult. In addition, many new state and local environmental regulations are causing contractors to rethink what they’re going to do with leftover mud/drilling fluid, creating a logistical challenge and adding expenses that may not have been factored into the budget. Mud recycling offers a viable solution to these challenges.
Adding a mud recycling system, like a Vermeer reclaimer, provides a solution for making the best use of the available water supply. Reusing mud on the jobsite cuts down on the amount of water required from sources like groundwater wells and surface water. It can also reduce the amount of additives, like bentonite, soda ash, polyanionic cellulose polymer (PAC) and partially hydrolyzed polyacrylamide (PHPA) polymer aide used to complete a bore.
Benefits of mud recycling include:
- Minimized use of fresh water and additives
- Minimized fluid disposal and trucking costs
- Maximized productivity — fewer shutdowns to mix drilling mud
How mud recycling works
To understand how a mud recycling system works, let’s look at the Vermeer R250C reclaimer. It can be paired with a variety of horizontal directional drills and its mobile design allows the mud recycling system to move where it’s needed.
Making the mud
The process of producing mud begins when drilling fluid additives are mixed with water and agitated in the reclaimer’s clean fluid tank. This drilling fluid is pumped from the mud recycling system to the high-pressure mud pump. From there, the mud travels to the drill and then down the drill string.
Recovering the mud
The returns, containing cuttings, then flow into the recovery pit. A pit pump transfers these spoils back to the mud recovery system. This slurry flows onto the reclaimer’s first-stage shaker deck, which separates larger cuttings from the usable drilling fluid.
The R250C features a balanced elliptical shaker motion, which helps provide optimal conveyance for lower gravity solids across the screens in a rolling motion, helping the de-watering process of solids. The fluids and solids that have passed through the first stage of the process are collected into the scalped tank and sent to the next stage of separation.
The remaining fine solids are separated from the usable drilling fluid when introduced to desilter cones that remove fine sand and coarse silts. The hydrocyclones separate particles from the fluid with a cyclonic motion, drawing solids to the side and the cleaned fluid out the top. The underflow from the hydrocyclones is directed up onto the upper shaker deck for further de-watering.
Hydrocyclones are not absolute filters. To optimize their performance, the fluid must be introduced into the cone with the correct head pressure. The innovative manifold on the R250C addresses many of the inefficiencies found in standard two-manifold configurations. Part one is a 45-degree outlet that reduces pressure and turbulence. The second part is the use of suction breakers, which relieves the undue vacuum. Combining these two features can maximize the separation efficiencies over standard manifold designs.
Meanwhile, the recycled fluid is returned to the clean tank, where it can then be reused in the HDD operation.
The scaled double-deck design offers visibility and accessibility to the lower deck, allowing the operator to keep the screens clean and wet, resulting in an efficient process. The double deck offers an overall surface area of 56 square feet (5.2 m2). The lower deck surface area is 32 square feet (3 m2), allowing for large volumes of drilling fluid to be de-watered and separated, maximizing the efficiency of the hydrocyclones and capitalizing on the ability to separate two distinct cup points.
The innovative design of the scaled double deck provides critical access to the bottom deck without having to remove screens on the top deck, making screen changes quick and efficient.
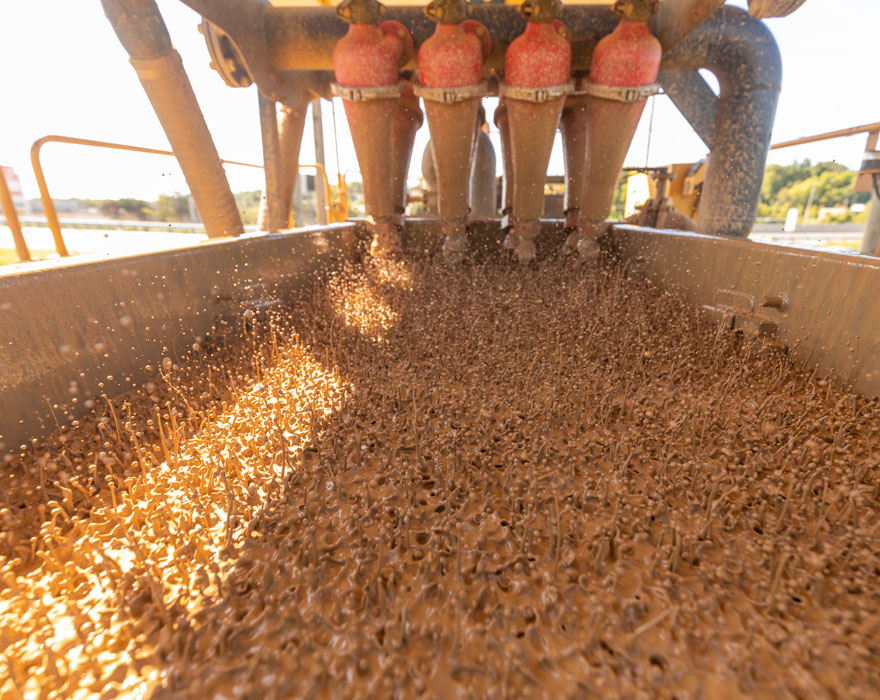
Considering the right solution
As mud recycling systems have made their way into the mid-sized HDD market, so has the number of models available for you to choose from. To determine which size to use, you need to consider the maximum rate you’ll be pumping fluid down the drill string. Knowing that, you’ll then be able to pick out a reclaimer that can keep up with the particular HDD model you’re using. For example, a Vermeer D100x140 S3 horizontal directional drill has an onboard pump with a maximum flow of 230 gallons per minute (870.6 L/min), so the R250C, which can clean up to 250 gallons per minute (946.4 L/min) of fluid, would be the best match.
For help selecting the right mud recycling system for your application, contact your local Vermeer dealer.
Vermeer Corporation reserves the right to make changes in product engineering, design and specifications; add improvements; or discontinue manufacturing or distribution at any time without notice or obligation. Equipment shown is for illustrative purposes only and may display optional accessories or components specific to their global region. Please contact your local Vermeer dealer for more information on machine specifications.
Vermeer and the Vermeer logo are trademarks of Vermeer Manufacturing Company in the U.S. and/or other countries. © 2022 Vermeer Corporation. All Rights Reserved.