Horizontal grinders and tub grinders endure some of the toughest jobsite conditions as they turn waste into a useful byproduct. Grinder tips take the brunt of the force during the sizing process. Selecting the best tip for the application will have a large influence on the production process and the quality of the end product. When using grit tips you must choose the correct grit coverage option to match the materials being processed for best results.
“Grit options help determine the useful life of the grinder tips. Vermeer now sells three grit coverage options — max, premium or pro — to match the life of the cutter tips to the application,” said Vermeer Recycling and Forestry Product Manager Jeff Bradley. “The max grinder tips deliver the longest life. The premium grinder tips feature additional welds on the ends and a single weld on the sides for an extended life span. Pro grinder tips have both ends and sides welded to provide a standard life span. The difference is the amount of carbide that is put on during the welding process. The max has a higher carbide content, which results in longer wear life.”
“Many grinder owners prefer to use a premium product and spend less time changing out tips,” continued Bradley. “They’re paying a little extra upfront for longer run times. And in most cases, changing tips can take anywhere from an hour to two hours. On a machine like the Vermeer HG6000 horizontal grinder, there are 20 tips held in place by two bolts each. So, changing out tips involves unscrewing 40 bolts, removing the tips, cleaning off the mounting surface, putting the new bolts on and torquing them.”
Most applications favor the use of premium grinder tips. Although in cases where the material to be processed may be contaminated — such as land clearing materials and construction and demolition (C&D) materials — a premium grinder tip coverage option might not be the best choice. “You can take a tip out by hitting a piece of steel or another hard contaminant,” explained Bradley. “In these working environments, a tip may have to be replaced before it’s worn out. So, there may be more value in choosing a pro grinder tip option.”
Select the best grinder tip style
Selecting the appropriate style of grinder tip depends on the material and geography. Different regions of the country have different types of trees and materials varying in hardness and abrasiveness. Here’s an overview of the grinder tip styles most widely used on horizontal and tub grinders.
- Wide block grinder tips are the most common in the industry. They can be used for several applications, such as land clearing materials, regrind, pallets, compost and green waste. “This is a more generalized tip,” noted Bradley. Other types of tips provide coverage options to address specific applications.
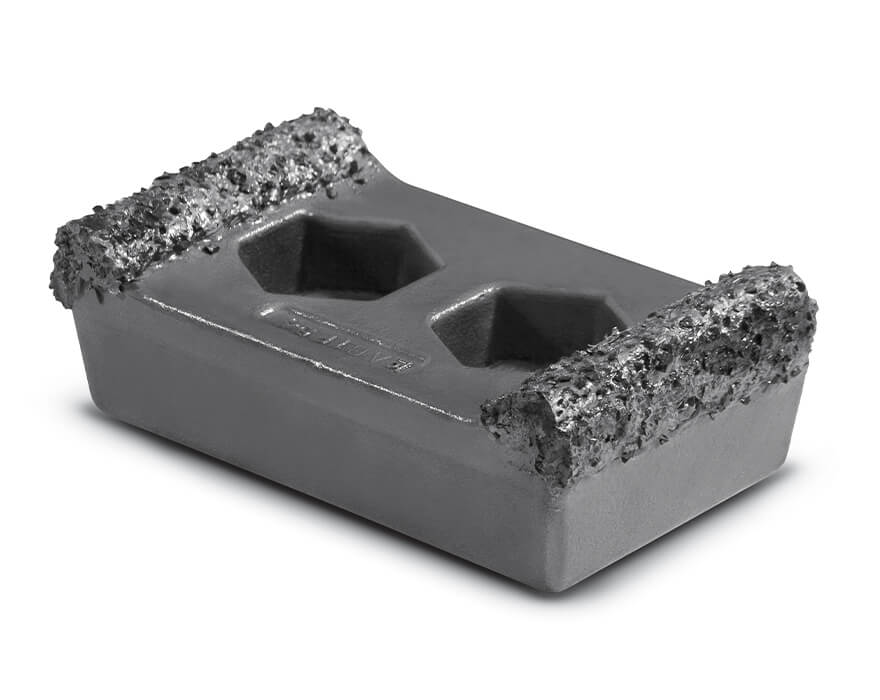
- Abrasion-resistant (AR) grinder tips are used when highly abrasive material is being processed. “This tip can best be used when working in sandy soil or with a regrind material,” noted Bradley. “From a life perspective, it performs well in these applications, but materials must be free of contaminants.”
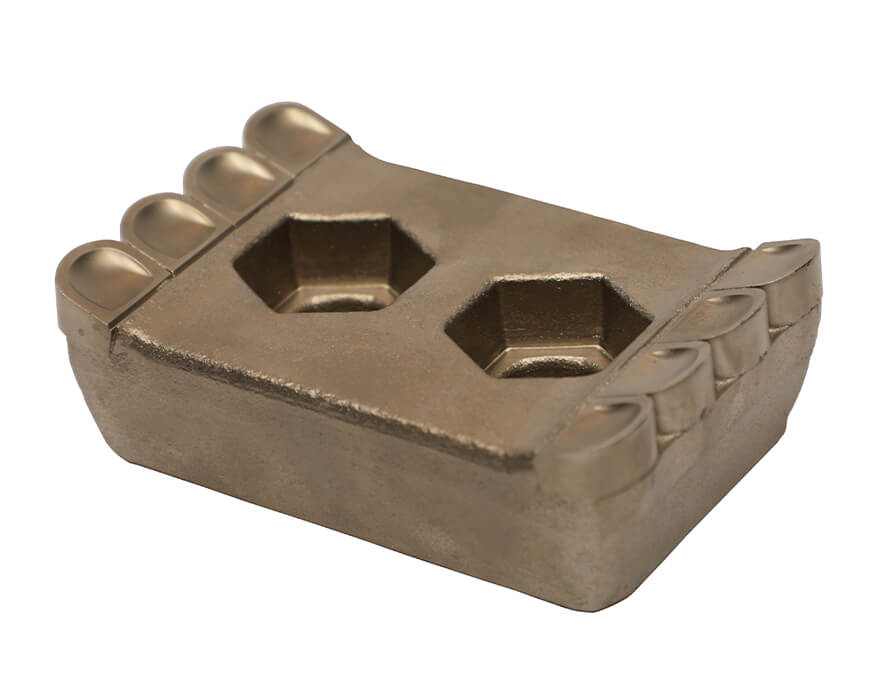
- Wing grinder tips have a unique design with an overlay of carbide that provides an effective solution for processing large-diameter woody material. A narrow center section helps the tip penetrate the log, then the wings clean out the remainder. “Traditionally, on a horizontal grinder, the wing-tip design allows penetration into the big woods,” said Bradley. “You’re taking a narrower chunk out of the material, which is easier to process. The narrow tip goes through the wood and splinters it easier. You can maximize your productivity by using the wing-tip design.”
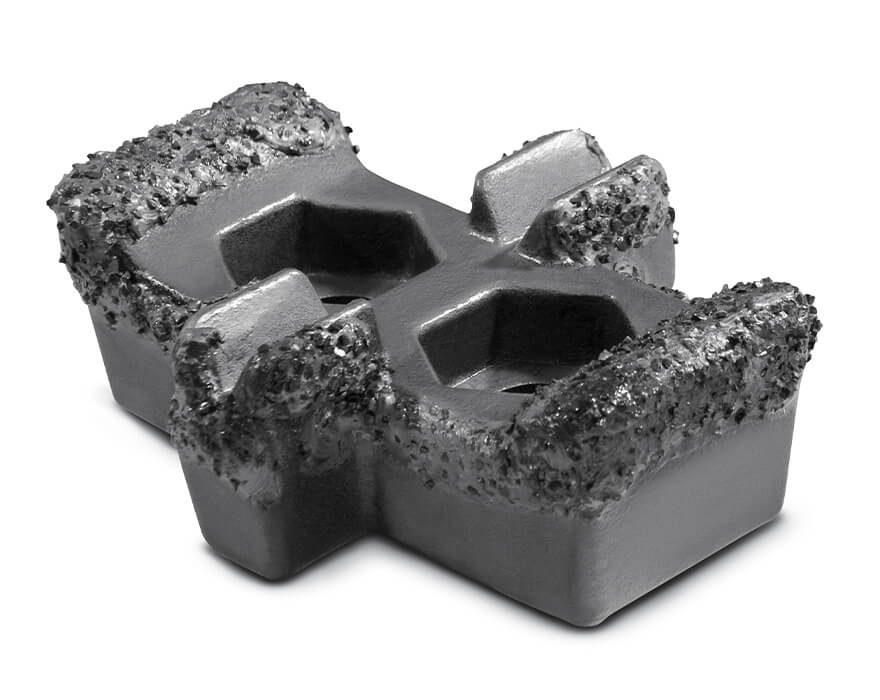
- Impact-resistant (IR) grinder tips offer an alternative to wing tips and are used to process large-diameter material. Their carbide inserts are very hard. “These tips are to give maximum longevity when dealing with hard wood that may contain small rocks or light contaminants in your material,” said Bradley.
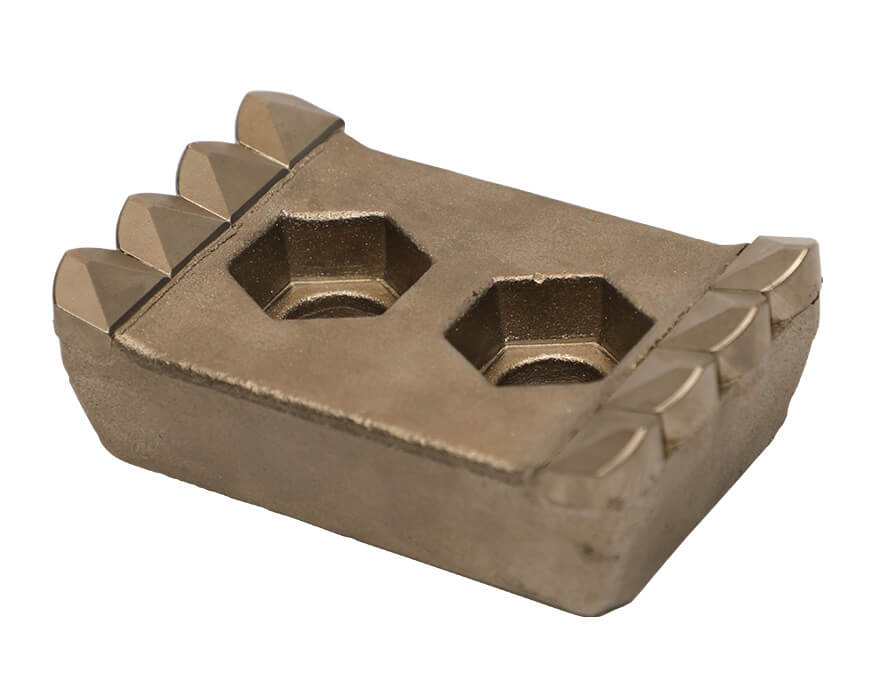
- Narrow block grinder tips have an overlay of carbide along the sides of the block, making them an effective solution for processing large-diameter woody material. “Depending upon your material type — if you’re doing stumps, if you’re doing big wood in a tub grinder — that narrow tip has a better processing capability,” said Bradley.
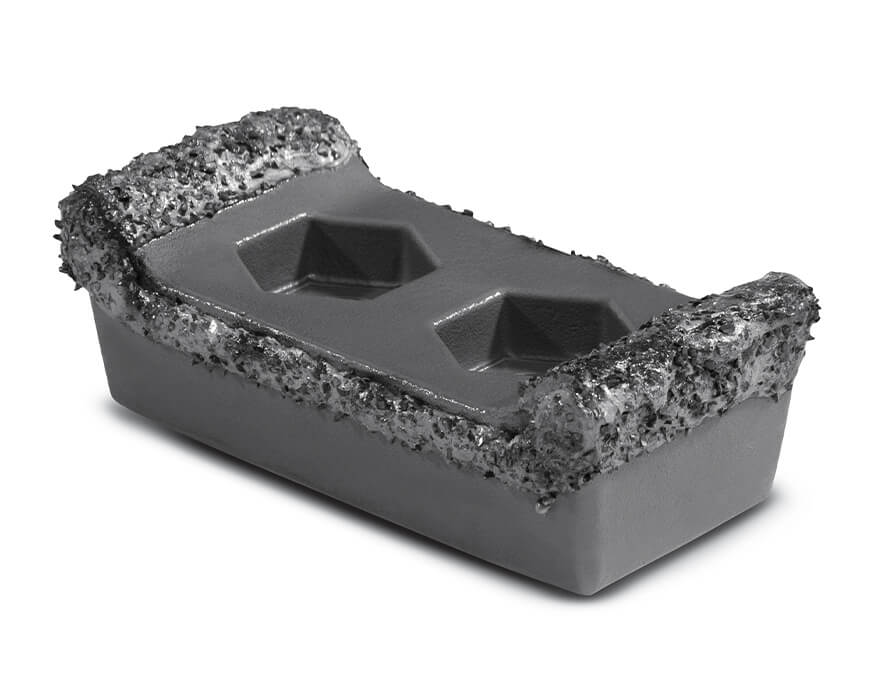
- Sharp grinder tips are precisely designed for cutting. They’re most commonly used on large-diameter wood for maximized production and a low amount of fines. With a sharp leading edge, these tips are for clean material only. The end product will be a little chunkier than a traditional wide block tip produces.
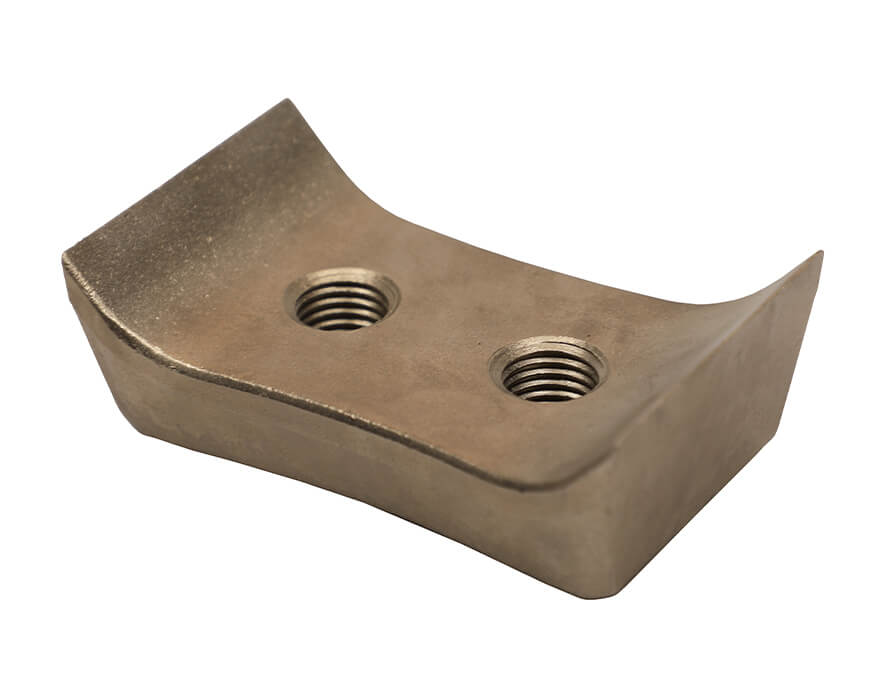
Grinder tip selection is influenced by the production rate and the end product desired. “The product produced by the grinder tips must match the end market for the material,” explained Bradley. “Several factors come into play. As a general rule, Vermeer would suggest starting with the wide block grinder tips, especially if they are doing a wide variety of projects. The wide block tips are the most universal tips that work with a large variety of materials and conditions. But, if someone has very defined or consistent material streams, they may want to use a specialized grinder tip style. For grinding primarily big wood in a horizontal grinder, Vermeer recommends wing tips.”
Pair grinder tips with grinder screens
Another point to consider is that grinder tip selection can influence proper screen selection. “Using sharp grinder tips may allow an operator to get by with using larger screen sizes,” Bradley said. This would allow them to maximize productivity because they’re not restricting the flow of material with the screen. More sizing is done right at the tip versus in the screening area.
“Optimization is key,” said Bradley. To make the right choice and for help optimizing production rates, consult a trained Vermeer Recycling and Forestry specialist at your local dealership.
Vermeer Corporation reserves the right to make changes in product engineering, design and specifications; add improvements; or discontinue manufacturing or distribution at any time without notice or obligation. Equipment shown is for illustrative purposes only and may display optional accessories or components specific to their global region. Please contact your local Vermeer dealer for more information on machine specifications.
Vermeer and the Vermeer logo are trademarks of Vermeer Manufacturing Company in the U.S. and/or other countries. © 2022 Vermeer Corporation. All Rights Reserved.