In the early 1950s, Gary Vermeer was facing a formidable foe: tree stumps. Millions of them were entrenched in agricultural fields across the corn belt. Gary was grinding his teeth in search of a better way to remove them. Anything but digging them out — a highly labor-intensive process.
In 1957, a Vermeer test crew pitted a novel machine against that common adversary. The crew quickly discovered the best way to grind a tree stump is with a side-to-side cutting motion, sweeping across back and forth.
It was an innovation in tree care equipment. Their approach still drives modern stump cutter technology. And the desire to find solutions still drives product development at Vermeer.
“Our testing methods are designed around solving a problem,” said Randy Runquist, manager of cutting edge research and development at Vermeer. “They are designed for a particular product.”
Once a new product is introduced, the enhancements never stop.
“Researching, refining and improving upon our high-quality products is part of the core culture at Vermeer. We are constantly looking for ways to improve every machine component to enhance our customers’ experience,” continued Runquist.
A solution to minimize change-out of grinder tips
An example of the Vermeer problem-solving approach to continually improve product design is the max grinder teeth for horizontal and tub grinders.
When it comes to tree care equipment, horizontal grinders and tub grinders endure some of the toughest jobsite conditions as they turn waste into a useful byproduct. Grinder tips take the brunt of the force during the product sizing process. The Vermeer team wanted to address demand for a longer-lasting grinder tip.
Enter the Vermeer max grinder tips, containing the maximum coverage amount of carbide. This translates into more time on the job and less time changing tips. Designed to extend the time between change-outs, max grinder tips will be included on the duplex drum with purchase of a horizontal or tub grinder.
“Many grinder owners prefer to use a more premium product and spend less time changing out tips,” explained Vermeer Recycling and Forestry Product Manager Jeff Bradley. “In most cases, changing tips can take anywhere from an hour to two hours.”
Vermeer recognizes that one solution isn’t the best fit for every application. That’s why there are different grit coverage options for customers. The key difference is the amount of carbide coverage applied during the welding process.
“Grit options help determine the useful life of the grinder tips,” said Bradley. “Vermeer now sells three grit coverage options — max, premium or pro — to match the life of the cutter tips to the application.”
Grit coverage options can be paired with six different tip styles to meet almost any customer requirement. These include wide block grinder tips, abrasion-resistant (AR) grinder tips, wing grinder tips, impact-resistant (IR) grinder tips, narrow block grinder tips and sharp grinder tips. This allows customers to tailor their choices to match their unique requirements.
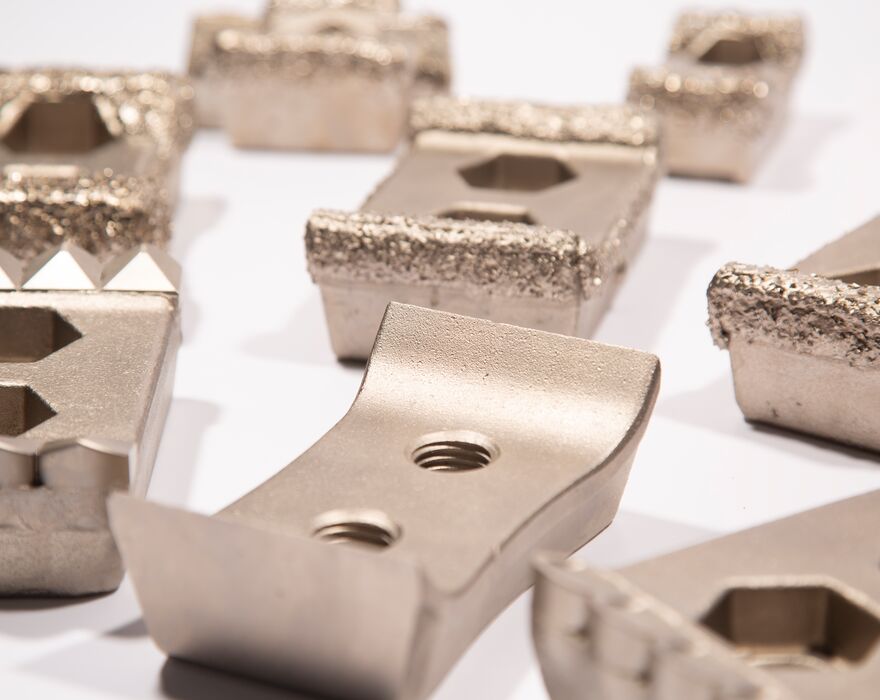
Focused on solutions
Vermeer continually innovates to provide tree care and recycling equipment solutions that solve customer challenges. Products are relentlessly refined in the never-ending search to find a better way. Contact your local Vermeer dealer today to discover how they can help find solutions for your job site.
Vermeer Corporation reserves the right to make changes in product engineering, design and specifications; add improvements; or discontinue manufacturing or distribution at any time without notice or obligation. Equipment shown is for illustrative purposes only and may display optional accessories or components specific to their global region. Please contact your local Vermeer dealer for more information on machine specifications.
Vermeer and the Vermeer logo are trademarks of Vermeer Manufacturing Company in the U.S. and/or other countries. © 2023 Vermeer Corporation. All Rights Reserved.