A surge in the solar energy industry is driving demand for lightweight, remote-controlled pile drivers that can move from pile to pile accurately, efficiently and with safe jobsite practices. Pile driving safety technology continues to advance, with GPS capability and optional automation allowing precise placement of piles with minimal operator input.
To meet diverse jobsite needs, Vermeer offers a range of pile drivers — from lightweight, remote-controlled machines that can move from pile to pile accurately and efficiently to models with seated operator’s stations.
One of the challenges faced by the solar energy industry is the transitory nature of the work. “Contractors are in Georgia this month doing solar pile installation, and they might be in Arizona next month,” Vermeer utility segment manager Ed Savage said. This makes pile driving safety training a priority. Remote control and automation are just two options that make it efficient for operators to place piles with safe jobsite practices.
Popular remote control capability
The pile driver industry is moving toward remote control. “More of our pile drivers are going out the factory door with remotes,” said Savage. With a wireless remote, crews can operate the pile driver and gain visibility around the machine. The operator can control most machine functions like hammer engagement, pile accuracy, auto plumb and ground drive. Remote control also enables automation, which can help improve jobsite efficiency and minimize the number of steps the operator needs to take to complete the install.
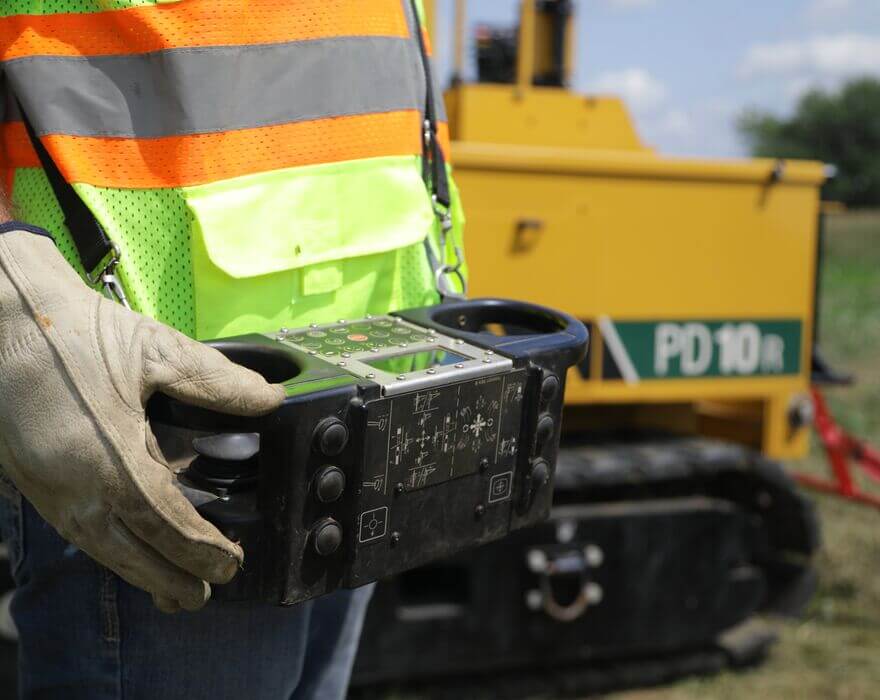
The move toward remote control allows several advantages from a safety perspective, including removing the need for an operator on the machine. The operator can now move to a position that provides the best visibility.
Several features have been designed with safety in mind in the remote-control pile drivers. For instance, if remote communication is lost with the machine, a non-communication symbol displays and functions cease until the connection is reestablished. The communications symbol displays as soon as the remote control comes back within range.
Built-in pile driving features for safe jobsite practices
Vermeer pile drivers have many built-in features for safe jobsite practices. To start, all machine controls must be in the proper position. “Controls have to be in neutral before you can start the machine,” Savage explained. “No control will be engaged when that engine starts.” If the remote control is enabled and any control is out of neutral, the engine will start but machine functions will not engage until all controls are reset to neutral. The display on the machine and on the remote control will both show “reset controls to neutral.”
The machines also include emergency stops. Red buttons on the machine and remote control stop all functions —including the track movement, the hammer coming down and any hydraulic system movements.
The optional point-to-point (PTP) technology recently released for the PD10R pile driver will allow the machine to automatically move from one pile to the next with minimal operator input. “As we get into more automation, like our PTP system, bump bars are on both ends of that machine,” Savage said. “If it encounters a person’s leg, a tree stump or something else, it stops movement of the machine. As we get more into automation, we’ll likely be adding more features like this.”
Bump bars only function and affect operation of the machine if automation is enabled. No automation track movement is allowed when one or both bars are down, which is the tripped position. No manual movement is allowed in the direction of the tripped bar.
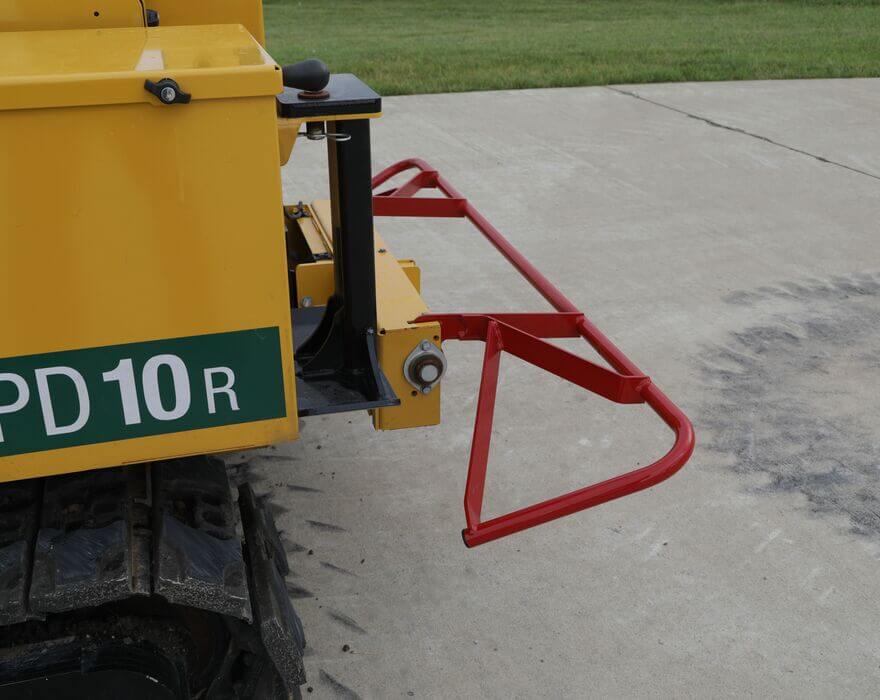
Operators need to be cautious when operating on slopes. Another feature for jobsite safety built into Vermeer pile drivers is the inclinometer. It monitors the machine’s orientation and can restrict mass tilt and ground drive speed. “Many solar sites are not graded anymore,” explained Savage. “Early on, the solar industry graded a lot of these sites. You didn’t have a lot of hills and swales. It is more virgin ground that you’re in now. When you have that 20-ft mast sticking up in the air, you need to be very aware of how fast you’re going on hillsides. We limit speed when we’re in work mode, which is when that mast is up.”
On remote-control machines, never operate the machine faster than you can comfortably walk. Keep the hammer lower when driving the machine. If driving over uneven ground, fold the mast and keep weight balanced over the tracks.
Safe setup considerations
Proper planning for a pile driving operation can help offset pile driving safety concerns. “One of the bigger safety concerns is raising that pile up,” Savage explained. “Operators often use the hammer box to raise the pile from a horizontal to vertical position before driving it. They either wrap a strap or chain around the pile or use a magnet to latch onto that pile. Then the pile is pulled off the ground from horizontal to vertical so it can be driven in the ground.” This handling process can lead to hand and foot injuries if proper precautions are not taken.
“These piles weigh up to 400 lbs,” noted Savage. That can create challenges with magnets if they’re not rated for the load. “Many customers are going away from magnets,” Savage added. Several customers are also trying to minimize the crew size so there are fewer people working in the vicinity of the pile.
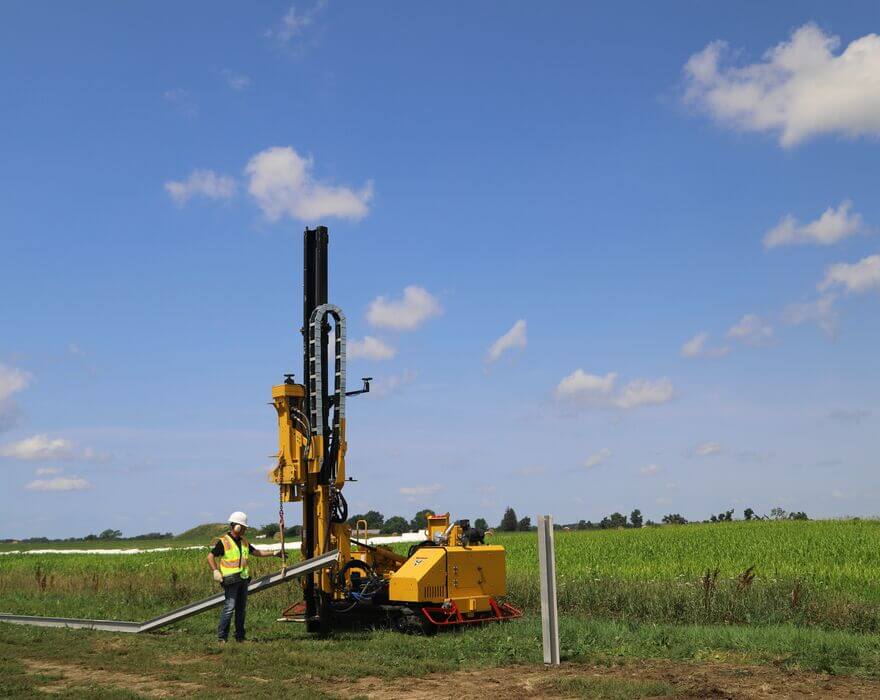
Other setup considerations include performing routine inspections and ensuring the proper use of personal protective equipment (PPE). “We do recommend that at the beginning of every shift you do a walkaround and make sure everything is working correctly before you start running for that shift,” Savage said.
For additional information about the proper way to operate your Vermeer pile driver and PPE requirements, visit vermeer.com/safety or contact your local Vermeer dealer.
Vermeer Corporation reserves the right to make changes in product engineering, design and specifications; add improvements; or discontinue manufacturing or distribution at any time without notice or obligation. Equipment shown is for illustrative purposes only and may display optional accessories or components specific to their global region. Please contact your local Vermeer dealer for more information on machine specifications.
Vermeer and the Vermeer logo are trademarks of Vermeer Manufacturing Company in the U.S. and/or other countries.© 2022 Vermeer Corporation. All Rights Reserved.